Сергей Иноземцев: «Асфальтобетон со свойством самовосстановления»
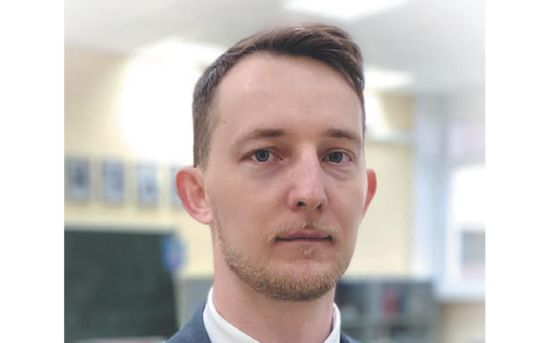
Группа молодых ученых из Московского государственного строительного университета представила отечественную разработку – самовосстанавливающийся асфальтобетон. Особый компонент умного материала позволяет ликвидировать часть образовывающихся в процессе эксплуатации трещин, тем самым увеличивая сроки нормативного состояния отдельных участков дорог. Подробнее о самовосстанавливающихся асфальтобетонах «Строительному еженедельнику» рассказал руководитель исследований Сергей Иноземцев, кандидат технических наук, доцент кафедры строительного материаловедения НИУ МГСУ.
– Сергей Сергеевич, как пришла идея заняться разработкой и созданием этого умного материала?
– Мы наблюдали, как у классического щебеночно-мастичного асфальтобетона ЩМА-15 в некоторых случаях проявляется эффект естественного восстановления, связанный с термопластичными свойствами битума преимущественно за счет легких фракций. Однако самовосстановление показателей происходит при повышенных температурах, что не дает возможности использовать данный потенциал, ведь нельзя позволить «размягчить» дорогу до такой степени, чтобы она восстановилась. И мы приступили к работе над тем, чтобы данный эффект кратно усилить и научиться им управлять, получили поддержку от Российского научного фонда и сформировали команду ученых, которая занялась исследованием этой проблемы.
– Какую технологию самовосстановления удалось разработать вашей команде?
– Ключевым компонентом нашей технологии являются специальные капсулы-контейнеры с полимером внутри, которые добавляются в асфальтобетонную смесь. Они предназначены для того, чтобы запасать вещество внутри себя, и, как только в процессе эксплуатации асфальтобетон начнет разрушаться и будут формироваться дефекты и трещины, из капсул высвободится полимер, который, полимеризуясь, склеит берега трещин и вернет асфальтобетону способность сопротивляться нагрузкам. Таким образом достигается эффект самовосстановления.
Мы апробировали капсулу на щебеночно-мастичных смесях ЩМА-15 и определили, что оптимальная концентрация капсул на уровне 3% от количества битума позволяет достичь максимального восстановительного эффекта.
– Какой полимер заложен в основу технологии? И самое главное – это российский продукт?
– С самого начала наших исследований на данную тему мы применяли только те компоненты, которые производят в России. В качестве активного компонента мы рассматривали несколько веществ и в конечном итоге выбрали тот, что дает лучший эффект самовосстановления. Производят этот AR-полимер в Казани, и я не уверен, что за рубежом есть аналоги.
– На данный момент в МГСУ есть опытные образцы?
– Да, конечно. Исследовательская работа еще не завершена, поэтому мы преимущественно работаем на опытных образцах, созданных в лаборатории.
На конкретных дорожных участках пока не работаем, но если представители отрасли будут заинтересованы в том, чтобы на текущем этапе осуществить работы по апробации, то мы готовы в этом направлении двигаться, чтобы достаточно быстро подготовить и необходимые материалы, и документы.
– В целом на каком этапе сейчас находится научная работа?
– Проект поддержан Российским научным фондом и рассчитан на несколько лет. Суть заключается в том, чтобы разработать общую концепцию того, как создавать подобного рода материалы. Не просто разработать самовосстанавливающийся материал, а сформулировать общие подходы, для того чтобы у отрасли были инструменты для создания собственного варианта подобного материалов.
На данный момент сама концепция принципиально готова, и у нас достаточно материалов, чтобы перейти к созданию промышленной партии. Вопрос в заинтересованности отрасли.

– Подобный материал существует в российской и зарубежной практике? Это импортозамещение или отечественное открытие?
– Само по себе исследование в области умных материалов, включая и самовосстанавливающиеся, является общемировой тенденцией в строительном материаловедении. За последние десять лет количество работ, посвященных данной теме, выросло в 3–3,5 раза, и в их числе есть ряд зарубежных и отечественных.
Иностранные исследователи предлагают использовать в качестве запасающего вещества внутри капсул различного рода масляные отходы, тогда как наше решение предлагает в качестве активного компонента применять полимер. В своих исследованиях мы сравнивали два этих подхода и доказали, что капсулы с полимерным активным веществом значительно превосходят масляные и обладают бо́льшим преимуществом.
– В чем заключается различие двух активных веществ и почему выбран именно полимер?
– Прежде всего отличается механизм воздействия на структуру асфальтобетона. Если в качестве восстанавливающего агента в капсулах используются масла, то в момент разрушения происходит следующий процесс: вещество высвобождается, смачивает стенки трещин, частично диффундируя, – по сути, разжижает материал омолаживая битум. В результате этого процесса происходит некоторое восстановление пластичности асфальтобетона.
В случае с применением полимера механизм действия иной. При разрушении капсул высвобождается полимер, который также смачивает берега трещин, частично диффундируя полимеризуется. В результате полимер изнутри склеивает часть дефектов, и за счет этого мы получаем не просто увеличенную пластичность, но и восстановленные связи внутри материала. В этом случае показатели самовосстановления асфальтобетона выше.
– Пластичность асфальтобетона иногда грозит образованием колейности на дороге. Как разрешаются эти риски?
– Как раз одним из главных недостатков применения масляных капсул является неблагоприятная пластичность, которая может привести к образованию колей. И для того, чтобы отойти от данного риска, нами было принято решение найти другой механизм действия. В случае с полимерным наполнителем капсулы склеивание трещин позволяет не допускать разжижения матрицы, давая лучшие показатели упругости и сопротивления.
– По информации МГСУ, подрядчики используют подобные технологии?
– Время от времени в прессе встречаются заголовки, посвященные умным материалам и нанотехнологиям в дорожном строительстве, но в России нет примеров внедрения или апробации асфальтобетонов со свойствами самовосстановления.
Знаю, что китайские коллеги запустили производство промышленного продукта в виде подобных капсул с масляным веществом внутри, однако информации об успешной реализации пока нет.
– Наверняка в вашей работе есть раздел, посвященный технико-экономическому обоснованию и целесообразности использования технологии самовосстанавливающихся асфальтобетонов. Можете поделиться данными расчетов?
– Разумеется, мы сделали экономические расчеты, которые основаны на оценке себестоимости и технического эффекта. Согласно нашим расчетам, использование капсул позволяет получать асфальтобетон, который не просто соответствует всем требованиям стандартов, но и обладает дополнительным набором уникальных свойств. Все это позволяет эксплуатировать участок дороги больший период времени. По сравнению с классическими щебеночно-мастичными смесями, несмотря на незначительное удорожание себестоимости материала, технико-экономическая эффективность достигает не менее 33%.
– В данном случае, что вкладываете в понятие эффективности?
– Мы исследовали стабильность во времени структурно-чувствительных параметров, таких как прочность. Со временем в процессе эксплуатации она уменьшается, то есть под воздействием различных факторов происходит разрушение материала и деструктивные процессы отражаются на показателях. Наблюдая за работой капсул, мы видим, что в период самовосстановления прочность возрастает, а технические показатели стремятся к первоначальным значениям. Этот эффект позволяет продлить время достижения момента, когда показатели достигнут критического значения, то есть дороге потребуется ремонт. По нашим оценкам, технология позволяет увеличить данный период нормативного состояния асфальтобетона более чем в 2–2,5 раза.

– Россия – очень большая страна, территории которой находятся в различных климатических зонах (отличаются погода, грунты, интенсивность движения и другое). В связи с этим вопрос: где и в каких условиях лучше всего проявят себя самовосстанавливающиеся асфальтобетоны?
– Не хочется сейчас необоснованно как-то ограничивать применимость разработки, поскольку предстоящий этап внедрения как раз выявит наилучшие условия. Сами капсулы способны ликвидировать в асфальтобетоне часть дефектов и трещин, и мы считаем, что смеси с такими компонентами целесообразно использовать при устройстве верхних слоев одежды автомобильных дорог в условиях, которые провоцируют трещинообразование. Достаточно широкая формулировка, но это могут быть и северные территории, где при низких температурах асфальтобетон становится хрупким, и южные, где трещины образовываются по другим причинам, например, из-за старения вяжущего.
– Насколько сложен процесс производства самовосстанавливающихся асфальтобетонов, ведь не секрет, что подрядчики сами готовят смеси вблизи объектов строительства, ремонта или реконструкции.
– Мы достаточно давно занимаемся разработкой строительных материалов и понимаем, как важно, чтобы методика производства менялась в минимальной степени или вообще не менялась. Технология создания самовосстанавливающихся асфальтобетонов несложная и вполне может быть осуществлена на существующих асфальтобетонных заводах. Условно говоря, дополнительный компонент можно вводить в смесь как обычную добавку с помощью отдельного бункера с дозатором. Никакого специфического оборудования для этого не требуется.
Что касается самого синтеза капсул, то и он может быть организован с использованием отечественного оборудования. В своих исследованиях мы использовали компоненты российского производства, которые сегодня присутствуют на рынке.
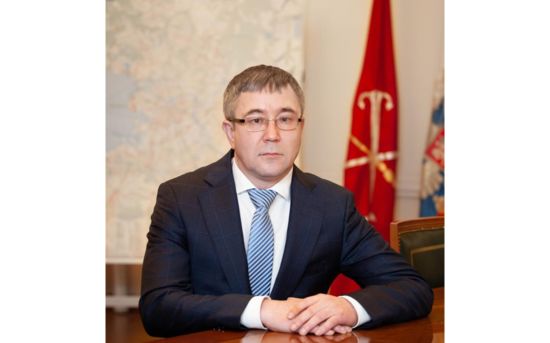
Председатель Комитета по развитию транспортной инфраструктуры (КРТИ) Александр Федотов рассказал «Строительному Еженедельнику» о сегодняшней ситуации в дорожном хозяйстве.
— Александр Михайлович, какие основные направления, связанные с развитием транспортной инфраструктуры города, определены комитетом на сегодня?
— Дороги — локомотив экономики, определяющий скорость и эффективность развития Санкт‑Петербурга и страны в целом. Транспортная инфраструктура является сложной многоуровневой системой, которую связывают процессы строительства, ремонта, содержания с умелым применением новых технологий и строительных материалов. Она определяет качество жизни населения города. Для создания такой системы нужны умелые руки и светлые головы дорожников.
С каждым годом увеличиваются объемы дорожного и мостового строительства, всё больше улиц доводится до нормативного состояния, повышается уровень транспортно-эксплуатационного состояния и безопасности.
Развитие транспортной инфраструктуры должно быть максимально синхронизировано с развитием самого города. Это основная задача, которая стоит перед нами.
В условиях быстрого роста автомобилизации и естественного увеличения нагрузки на улично-дорожную сеть центра Санкт-Петербурга, правительством города прорабатывается комплекс мер по улучшению транспортной ситуации и сохранению исторического центра Северной столицы. Он направлен на создание и развитие магистралей, позволяющих повысить связанность и пропускную способность улично-дорожной сети районов Санкт-Петербурга, а также призванных перенаправить транспортные потоки в обход исторического центра.
Особое внимание уделяется исторической части города, где каждая улочка, переулок требуют индивидуального подхода. Основные трудности при работе здесь связаны с исполнением действующих норм и правил в условиях застройки, не предназначенной для современных транспортных нагрузок.

— Какие объемы финансирования отрасли в этом году, какие источники привлекаются для реализации проектов?
— Для развития транспортной инфраструктуры Санкт-Петербурга в 2023 году выделено почти 105 млрд рублей, в том числе средства федерального бюджета, ИБК и казначейские кредиты.
Из них на дорожное хозяйство предусмотрено 46 млрд. Затратная часть на ремонт дорог в этом году увеличена до 12,3 млрд, включая 1,2 млрд федеральных средств, на капитальный ремонт дорог — до 4 млрд, на ремонт трамвайных путей — почти вдвое по сравнению с прошлым годом: с 1,9 млрд до 4 млрд рублей. Это позволит отремонтировать 22 км трамвайных линий. Все проекты, которые реализуются в этом году, полностью обеспечены финансированием из различных источников: это федеральный и региональный бюджеты, инфраструктурные бюджетные кредиты, концессионные соглашения.
— Получено разрешение на строительство крупного транспортного проекта – Южной широтной магистрали. Расскажите об этом объекте.
— Южная широтная магистраль, строящаяся за счет Адресной инвестиционной программы, - это очень долгожданный объект для Московского, Пушкинского и Колпинского районов. По сути, эта дорога станет дублером КАД и соединит Сарицкую улицу, Петербургское шоссе и шоссе Подбельского. Стратегически важная трасса повлияет на социально-экономическое развитие южной части города.
ЮШМ включает 3 транспортные развязки. Сейчас практически завершены подготовительные работы по расчистке коридора для будущей магистрали. В финальной стадии разработка рабочей документации, регистрация земли для строительства. В ближайшее время планируется дать торжественный старт началу основных работ.

— Какие объекты введены в эксплуатацию в этом году?
— В августе в Приморском районе завершено строительство Шуваловского проспекта от Камышовой до Планерной улицы, связывающего две части района, с возможностью въехать на скоростную магистраль ЗСД.
В мае были введены в эксплуатацию съезды вблизи делового квартала «Лахта Центр», обеспечивающие связь с Приморским шоссе, Приморским проспектом и улицей Савушкина.

— Какие объекты инфраструктуры дорожники сегодня строят в Санкт-Петербурге?
— Прежде всего следует выделить полуторакилометровую транспортную развязку на пересечении Московского шоссе с Дунайским проспектом. Уже через год она обеспечит непрерывную транспортную связь основных городских магистралей в южной части города, выход транспорта на автодорогу федерального значения М-10 «Россия» и далее – на международный транспортный коридор «Европа – Западный Китай». Сегодня генподрядчиком АО «ПО «Возрождение» уже ведутся работы по устройству асфальтобетонного покрытия на первой части путепровода, специалисты завершили переустройство теплосети и линий электропередачи, освобождается пятно застройки для второй части и съездов.
Еще один ключевой проект, реализуемый на юге города, - реконструкция Петрозаводского шоссе со строительством двухуровневой развязки, надземного пешеходного перехода и расширением шоссе до 6 полос движения. Подрядчик ударными темпами завершает работы по установке шумозащитных экранов, переустройству инженерных коммуникаций, завершает комплекс работ по устройству мостового полотна и установке барьерного ограждения. До конца года откроем рабочее движение через железнодорожные пути Октябрьской железной дороги в разных уровнях.
На очереди старт строительства трассы М-32, которая соединит будущую дорогу М–49 с Приморским шоссе. Получим положительное заключение Госэкспертизы в ноябре и сразу же приступим к реализации проекта. Подрядная организация уже осуществляет переброску необходимых сил и средств в зону строительных работ.
Долгожданным подарком для всего города является начало строительства Большого Смоленского моста, который соединит берега Невы в самом широком русле реки - между Володарским мостом и мостом Александра Невского. Длина Большого Смоленского моста - 1,6 километра. Разводной пролет - двукрылый. В сведенном положении высота центральной части моста над водой - 15 метров. Ширина судоходного пролета - 60 метров. Проектом предусмотрено 6 полос движения автотранспорта (по 3 в каждую сторону), в центре - два полотна для движения трамваев. С УДС города его будут связывать три развязки.
Проектная документация загружена в ФАУ «Главгосэкспертиза».
Идеальный случай взаимодействия города и инвесторов. Проект разработан частным инвестором под техническим сопровождением городского заказчика.

— Что можно сказать про выполнение плановых показателей национального проекта «Безопасные качественные дороги» в Санкт-Петербурге в этом году?
— Улично-дорожная сеть, проспекты, набережные, шоссе преображаются. Повышение скорости и комфорта передвижения по ним отмечают сами автомобилисты и жители города. Протяженность трасс, отвечающих всем нормативным требованиям, неуклонно увеличивается.
Санкт-Петербург присоединился к реализации национального проекта «Безопасные качественные дороги» в 2021 году. В этом году запланировано заменить покрытие проезжей части и восстановить благоустройство на 250 км, из них в рамках национального проекта отремонтировать более 150 км на 63 объектах.
Стоит отметить, что в рамках реализации нацпроекта БКД в этом году впервые применили подход маршрутного ремонта. Дорожное полотно обновлено на Арсенальной, Ушаковской, Пироговской, Выборгской набережных и на Приморском проспекте. То есть по правому берегу Невы от въезда в город до ЗСД обеспечен практически сквозной беспрепятственный и безопасный проезд. Также отремонтированы часть Московского проспекта, Литейный, Ленинский, Витебский проспекты, Песочное шоссе. В стадии активных работ находятся Софийская улица, проспекты Ветеранов и Энергетиков, Приморское шоссе.

— Как идет развитие транспортной инфраструктуры Кронштадта?
— Строительство и модернизация уличной дорожной сети Кронштадта связана с созданием туристско-рекреационного кластера на территории города, посвященного истории ВМФ России. Эта точка притяжения уже стала излюбленной среди жителей и гостей Петербурга. Ежемесячно Кронштадт посещает несколько сотен тысяч туристов. Поэтому сегодня на особом контроле одна из основных задач – развитие инфраструктуры острова Котлин. С этой целью бюджетом города в 2023-2025 гг. предусмотрены расходы в объеме 16,95 млрд рублей. КРТИ уже заключил госконтракты на проведение работ по 5 объектам, еще по одному проводятся конкурсные процедуры. Будут выполнены работы по строительству и реконструкции участков Цитадельского и Кронштадтского шоссе, дорог на территории 7-го и 8-го кварталов и уже строится пешеходная набережная, которая объединит парк «Остров фортов» и сквер «Инчхон».
Для улучшения доступности по заказу Минстроя России компания «ДСК» начала реконструкцию развязки КАД и Кронштадтского шоссе. Со своей стороны, Санкт-Петербург, как я уже говорил, начал реконструкцию Кронштадтского шоссе с расширением до четырех полос от Комплекса защитных сооружений до Цитадельской дороги.

— Около 14 млрд рублей пойдет на развитие дорожной инфраструктуры в Шушарах до 2025 года. Что запланировано сделать в этой части города?
— Мы стараемся поменять сложившуюся ситуацию с развитием улично-дорожной сети на территориях новых жилых кварталов. Строительство улично-дорожной сети достаточно отстало от застройки домов. Руководству города удалось сконцентрировать вливания в решение этой задачи совместными усилиями с привлечением средств бизнеса и средств города.
Что касается поселка Шушары, правительством Санкт-Петербурга решен большой объем имущественных и земельных вопросов. В настоящее время ведется реконструкция Пушкинской улицы. В работе у комитета еще 14 объектов модернизации улично-дорожной сети в микрорайоне. Это строительство Новгородского проспекта, Школьной улицы, Шушарской дороги и других улиц.

— Как повлияли на строительство и реконструкцию объектов транспортной инфраструктуры недавно введенные санкции?
— Импортозамещение в дорожной отрасли ведется с 2014 года, поэтому нам удалось минимизировать те риски, с которыми столкнулись представители других отраслей. Бизнес умело переориентировал логистические цепочки на Восток и на внутренний рынок, что дало отечественным поставщикам толчок и стимул к развитию. В итоге было налажено производство АБЗ, на рынке появились укладочные комплексы, специальная, грузовая техника. Отмечен рост производства основных материалов производителями из Санкт-Петербурга и Ленинградской области.
Сохранить уникальность и индивидуальность Санкт-Петербурга, увеличить темпы его развития, при этом создать современные и комфортные условия для перемещения жителей города ― вот задача, которую ставит перед собой дорожная-строительная отрасль.

ГК «Арасар» называют пионером применения новых технологий демонтажа – она одной из первых в России для сноса зданий и сооружений внедрила лазер, алмазную резку и многие другие инновационные решения. О возможностях компании рассказывает ее основатель Александр Штарёв.
– Александр Юрьевич, как Вам удалось внедрить лазерную технологию для демонтажа?
– Мы обратили внимание на лазерную установку, которая использовалась для поджига нефтяных разливов с безопасного расстояния, и увидели возможность ее использования для нашей деятельности. Первый объект, на котором был применен лазер, – Кондопожский комбинат хлебопродуктов. Это произошло в 2022 году. На площадке предприятия мы успешно демонтировали с расстояния 50 метров массивную аварийную металлическую конструкцию бункерного типа высотой 60 метров и общим весом со вспомогательным оборудованием до 50 тонн. Лазер выглядит очень эффектно, как в научно-фантастическом фильме.
ГК «Арасар» одна из первых в России внедрила в демонтаж и алмазную резку, но это было давно, еще в 2000-х годах, когда о таком способе работы на нашем рынке не слышал никто. Мы комплексно подошли к данному вопросу, для продвижения и популяризации этих технологий много работали с проектными институтами, разъясняли потенциальным заказчикам, что так можно. Сейчас выполнение некоторых задач демонтажа немыслимо иным способом. Также мы изучали возможность демонтажа разрядом электрического тока – проводили собственные исследования, ряд решений запатентовали.
Наша команда стремится освоить как можно больше технологий и всегда подобрать наиболее точный способ решения конкретной проблемы. ГК «Арасар» имеет и применяет все возможные технологии в нашей области, разработанные на данный момент, которые позволяют решать любые задачи демонтажа самых сложных конструкций. Я с гордостью могу сказать, что среди российских демонтажных компаний лишь единицы обладают таким набором компетенций.

– Над внедрением каких технологий Вы работаете сейчас?
– Мы постоянно ищем новые пути решения демонтажных задач. Сегодня активно развиваем направление демонтажа гидроразмывом бетона под огромным давлением – 1000 бар. Это, на наш взгляд, перспективная технология на данный момент. Пока она не представлена массово в России, задумывалась как ремонтная. Тем не менее мы видим большой потенциал ее применения для демонтажа.
– У вас много высокотехнологичного оборудования, в том числе импортного, которое требует соответствующего технического обслуживания. Насколько вы зависите от иностранных поставщиков? Как в компании идет процесс импортозамещения?
– К сожалению, не все оборудование можно заместить. Действительно, рынок почувствовал текущие трудности, но они преодолеваются. Знаю, что многие наши поставщики переориентировались с западных рынков на иные и пытаются заменить даже уникальное оборудование. ГК «Арасар» вносит в этот процесс свою лепту. Например, ключевую роль в алмазной резке играет канатная система. Мы запустили производство этого оборудования под собственным брендом на нашей производственной площадке в Санкт-Петербурге, и оно с успехом работает на объектах России. Об этом думали еще до введения санкций и ухода основных поставщиков – нам было интересно освоить такую компетенцию, но когда были введены санкции, мы ускорили вывод на рынок канатных систем собственного производства. Наша компания не только применяет их в своей работе, но и продает другим участникам демонтажного рынка.

– Расскажите о самых крупных и значимых объектах компании.
– За 25 лет своего существования ГК «Арасар» выполнила более 1000 проектов. Прямо сейчас мы реализуем социально значимый проект в Мариуполе. Там мы демонтировали, вывезли и утилизировали около 600 тысяч кубометров строительного объема. Также трудимся на Городецком и Волховском гидроузлах, соответственно, в Нижегородской и Ленинградской областях, на одном стратегическом объекте Росатома и ведем еще с десяток не менее важных федеральных инфраструктурных проектов.
– Какие интересные организационные и технические задачи по демонтажу удалось решить?
– ГК «Арасар» сфокусирована на сложных инженерных задачах демонтажа, это наша специализация, поэтому подавляющее большинство из тысячи наших объектов очень сложные. Следует отметить, что демонтаж всегда разный. К решению каждой задачи требуется индивидуальный подход. Так, например, сейчас на одном из наших объектов выполняется демонтаж под водой на глубине от 10 до 25 метров. При этом полностью отсутствует документация по обследованию демонтируемой конструкции. Решения принимаются по ходу производства работ.
Нам приходилось работать и при температуре –50°С, и круглосуточно в темноте полярной ночи, и под водой, и на высоте более 100 метров, и под землей на глубине 60 метров. Но пока за 25 лет мы не встретили ни одной инженерной задачи, с которой не смогли справиться.
– Известно, что ни один вуз и техникум не выпускает специалистов по демонтажным работам. Как Вы подбираете кадры?
– Да, к сожалению, готовых демонтажников нет, поэтому первый этап поиска подходящего человека очень сложен. Мы находим строителей и переучиваем их на наш профиль. У нас разработано несколько программ обучения и наставничества. Выпущены специальные методички. Есть определенный цикл, который необходимо пройти каждому новому сотруднику. Следует отметить, что в нашей компании всегда благоприятная ситуация для обучения на конкретных практических примерах. Мы обычно ведем не менее 10 проектов в различных точках страны, причем все они разные по виду демонтируемых конструкций, применяемым технологиям и внешним условиям. У нас всегда есть подходящая работа, которую можно демонстрировать человеку, и на ее примере разъяснять специфику нашей деятельности.
– Вы говорили, что компания «Арасар» применяет комплексный подход к демонтажу зданий и сооружений.
– Все зависит от желания заказчика. Принципиально мы сейчас позиционируемся как узконаправленная компания – занимаемся демонтажем, изучаем все, что связано с демонтажем. Становимся с каждым днем лучше и лучше в этой профессии. Разумеется, мы можем выполнить весь комплекс услуг по демонтажу объекта: проектирование, работы на площадке, экологическое сопровождение, а также благоустройство и озеленение.
– Расскажите о возможностях компании: какова производительность, сколько объектов вы способны вести одновременно?
– Наша компания востребована на рынке демонтажных работ, поэтому ведет не менее 10 проектов одновременно. Конкретную производительность мы не определяем, потому что находимся не в плановой экономике, поэтому беремся за решение задач в любом объеме, который предлагает рынок. И за 25 лет работы компании не было ни одного случая, чтобы мы не справились с задачей или отказались от проекта по причине полной загрузки техники или людей.

– В случае нехватки ресурсов под конкретную задачу вы привлекаете рабочую силу или оборудование со стороны?
– Субподряд практически не используем, потому что, во-первых, наша работа очень ответственная, особенно с точки зрения безопасности, во-вторых, мы привыкли к колебаниям рынка в зависимости от различных факторов, в том числе политических. За четверть века работы мы научились гибкости и способности адаптироваться к любым внешним условиям.