Опорные леса в современном строительстве
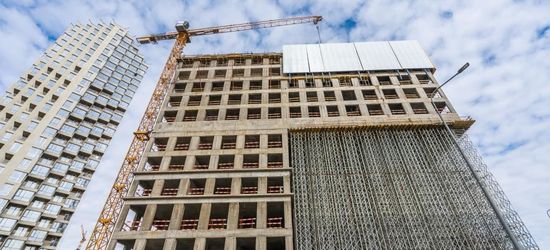
Современное строительство — высококонкурентная среда. Компании-застройщики борются за внимание потенциальных покупателей самыми разными способами. Одним из важных факторов при выборе жилого комплекса является его архитектура. Покупатели высоко оценивают необычные, сложные, функциональные решения. Совместно с застройщиками над созданием жилых комплексов трудится большое количество экспертов: архитектурные бюро, проектные организации, поставщики решений и оборудования.
Одним из примеров таких проектов является жилой квартал Shagal от Группы «Эталон». В сегодняшней статье речь пойдет о 13-м корпусе квартала Shagal, который расположен в непосредственной близости от набережной Марка Шагала и автомобильного моста через затон Новинки. Корпус представляет собой уникальное сооружение с консольным выступом, который находится на высоте 27 метров над уровнем земли и является основанием для вышележащих шести этажей. Консольная плита опирается на смежные блоки здания, а ее центральную часть поддерживают несущие колонны, образующие жесткую пространственную конструкцию.
Архитектурное решение комплекса воплощалось в жизнь технической дирекцией Группы «Эталон» совместно с разработчиком решений — компанией «Дока Рус». О том, как это происходило, нам рассказал технический руководитель проекта от компании «Дока Рус» Федор Крупенин.

— Федор, расскажите, пожалуйста, какие задачи были поставлены перед техническим отделом вашей компании? Как компания, поставляющая опалубку и опорные леса, могла оказать влияние на ход строительства?
— Перед нами стояла задача разработать проект для возведения консольной части здания и реализовать его: выполнить расчеты, подобрать необходимое оборудование, обеспечить логистику, монтаж и демонтаж оборудования на стройплощадке.
— В чем сложности данного проекта с точки зрения поставщика опорных лесов?
— Корпус представляет собой сложное архитектурное сооружение с консольной конструкцией, которая «парит» на высоте 27 метров и несет на себе шесть жилых этажей. Нам предстояло рассчитать нагрузки и выставить опорные леса под консольной плитой так, чтобы они до определенного этапа удерживали не только плиту, но и строящиеся на ней этажи. Только после возведения нескольких этажей поверх плиты конструкция могла начать «работать», принимая на себя нагрузки самостоятельно.
— Чем проект был особенно интересным и сложным для вас лично?
— «Дока Рус» подключилась к проекту на стадии проектирования инженерного решения. Наш технический отдел тесно взаимодействовал с инженерами-конструкторами проектной организации Группы «Эталон».
Для обеспечения безопасности работ по возведению консольной части и выполнения условия жесткости возводимой монолитной конструкции мы создали трехмерную расчетную модель опорных лесов, которая включалась в расчетную модель здания (SCAD). Мы анализировали усилия в стойках опорных лесов, исходя из результатов, полученных в этой модели. Расчет выполнялся в несколько этапов по мере нагружения лесов определенным количеством этажей с внесением соответствующих корректировок в проект.
Данная технология позволила нам получить более точные результаты, а также оптимизировать расстановку оборудования и уменьшить количество используемого материала.

— Какие технические решения были применены для реализации проекта?
— Усилия, возникающие в стойках опорных лесов, были близки к предельным допустимым значениям, поэтому мы приняли решение расставить леса методом «башня в башне» («шаг» рам лесов составлял 0,5 м). Установка башен производилась посредством укрупненной сборки. Особенности конструкции выбранной системы опорных лесов позволяли собирать блоки высотой в несколько ярусов на земле. Собранные блоки перемещались краном на уже установленные конструкции лесов, что позволило ускорить монтаж и повысить безопасность работ.
Еще одно проектное решение заключалось в применении строительного подъема консольной плиты. Стойки опорных лесов на определенном участке выдвигались выше проектной отметки, а после демонтажа лесов плита прогибалась до заданного уровня.

Дополнительная сложность заключалась в проектировании опорных стоек фундаментной плиты. Необходимо было расставить леса в обход монолитных ребер жесткости высотой два метра. Было применено решение по созданию несущего каркаса из стандартных силовых элементов для установки опорных лесов в зоне данных ребер.
— На каком этапе вы завершили участие в проекте?
— В целях безопасности наши опорные леса продолжали находиться под консольным участком здания на протяжении девяти месяцев. После образования единой жесткой консольной конструкции, которая самостоятельно воспринимает нагрузки, опорные леса можно было демонтировать. Строительство корпуса было продолжено с применением дополнительного оборудования, предоставляемого нашей компанией, — ветровых экранов и защитных платформ по контуру здания для обеспечения безопасного проведения монолитных и фасадных работ.

ТЕХНОНИКОЛЬ представила платформу ЭКО.ТН участникам Форума Союза переработчиков пластмасс
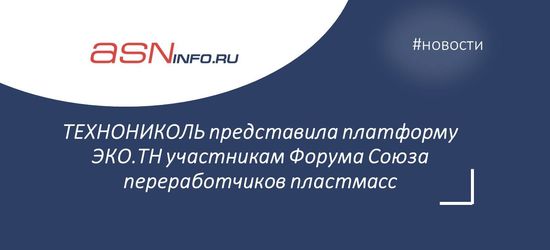
В Москве прошел Форум Союза переработчиков пластмасс, организованный при поддержке Минпромторга России. Дмитрий Михайлиди, директор по развитию направления «Полимерная изоляция» ТЕХНОНИКОЛЬ, представил платформу, объединяющую переработчиков и продавцов вторсырья.
Выступая перед участниками форума, Дмитрий Михайлиди отметил: «Производство базовых полимеров растет каждый год, в 2023 году рост составил 3,1 %. При этом доля вторичных полимеров в России не превышает 7 % от общего объема и в натуральном выражении составляет около 0,8 млн тонн. Тогда как в мировой практике использование вторичных полимеров находится на уровне 8 млн тонн в год (по данным за 2023 год). На сегодняшний день рынок позволяет заменить около 30 % базовых полимеров вторичными. Это поможет не только сохранить ресурсы планеты, но и сократить затраты бизнеса. Ведь дисконт вторичных полимеров колеблется в диапазоне 10–30 %».
Рынок переработки переживает активный рост, о чем свидетельствует увеличение количества линий грануляции: за последние два года прирост составил 49 %.
Компания ТЕХНОНИКОЛЬ на собственных производствах реализует принципы экономики замкнутого цикла: возвращает в производство ПНД, ПП, резину, ПВХ, обработанные масла, полистирол, резиновую крошку.
Больше года назад эту практику решено было расширить за пределы производства ТЕХНОНИКОЛЬ: компания создала маркетплейс по продаже отходов ЭКО.ТН. Он позволяет осуществлять полный цикл управления и отслеживания процесса продажи, переработки и поставки вторичных ресурсов.
На платформе можно реализовать любой вид вторсырья: пленку, картон, полиэтилен и даже кусковой чугун. Для продажи достаточно заполнить информацию о лоте: название отхода, фото, объем и вес, уровень влажности, загрязнения, наличие засоров, прессовки, адрес вывоза и стартовую цену.
Лот будет отображаться на интерактивной карте, что позволит в короткие сроки найти наиболее выгодные каналы сбыта для отходов, которые неизбежно образуются на любом производстве.
Платформа обеспечена сырьем и реальными сделками, а потому интересна переработчикам. В ближайшее время в ЭКО.ТН будет интегрирована система 1С. Это позволит автоматизировать сделки от образования остатка до вывоза и оплаты.
Демонтаж в условиях промзоны
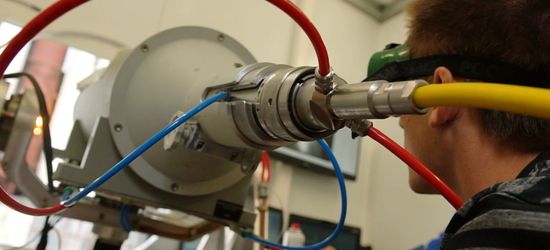
О технологическом процессе демонтажа в условиях действующих промышленных производств рассказывают представители ГК «АРАСАР».
Демонтаж зданий и конструкций в условиях действующих промышленных предприятий имеет свои особенности. Необходимо учитывать производственный процесс в зоне, где будут проходить демонтажные работы, еще более строго соблюдать все требования по безопасности труда и предотвращению аварийных ситуаций.
По словам представителей ГК «АРАСАР», принято выделять два основных этапа проведения демонтажных работ на промпроизводстве. Первый этап — это разработка и согласование проекта производства работ — основного документа, где прописаны все мероприятия в рамках реализации объекта. Второй этап — собственно само производство работ. Из-за действующего производства проблем масса, но уже на стадии разработки ППР компания старается предусмотреть все возможные сложности в работе и отрегулировать их. Также в «АРАСАР» предусмотрен и третий этап — это рециклинг, если он возможен. В частности, демонтированный железобетон дробится в щебень и пускается во вторичное использование.
Самая распространенная задача в таких проектах, отмечают специалисты, — демонтаж фундаментов на действующих производствах при замене оборудования. Так как работы производятся на действующем производстве, то в первую очередь особое внимание уделяется безопасности персонала, далее важна координация работ с другими подрядчиками и персоналом цехов и тщательная предварительная подготовка. Но на первом месте, подчеркивают в «АРАСАР», — в любом случае безопасность и охрана труда.

Немалый опыт компании в демонтажных работах в условиях действующих производств помогает реализовать новые проекты и дает преимущество, отмечают в «АРАСАР». По словам специалистов, основной эффективный способ демонтажа в условиях промышленных предприятий — это технология алмазной резки. Она позволяет быстро разрезать железобетонные конструкции на легко вывозимые части. Организация алмазную резку применяет уже 25 лет. Кроме того, совсем недавно ГК «АРАСАР» первой в мире применила для промышленного демонтажа металлоконструкций технологию лазерной резки. Это абсолютное ноу-хау в демонтаже.
«Интересных проектов работы в промышленном секторе у нас множество, — говорит основатель ГК ”АРАСАР” Александр Штарев. — Расскажу об одном из последних и точно уникальном даже в мировом масштабе проекте — демонтаже железобетонной конструкции на глубине 20 метров под водой на действующей гидроэлектростанции. При реконструкции одного из секторов водосбросной платины наша компания реализовала чрезвычайно сложный проект. Мало того, что работы велись под водой, так еще период их выполнения частично выпал на зиму, а температура в этом регионе достигала минус 35 ℃. А еще мы специально разработали и произвели для этого проекта оборудование, аналога которому в России не производят. В общем, и инженерный персонал компании, и линейный проявили себя на максимальном профессиональном уровне».
Александр Штарев отметил также проект с применением лазера, который был не на действующем производстве, а как опыт в отрасли первым в мире. «На нашем объекте необходимо было произвести демонтаж всех внутренних конструкций здания цеха, оборудования, фундамента, подсобных помещений, а также очистить фасады от металлоконструкций и трубопроводов. Одна из металлических толстостенных труб диаметром почти два метра располагалась в углублении фасада, шла на всю высоту здания и была в аварийном состоянии. Соответственно, альпинистов использовать было нельзя, экскаваторы — тоже, так как был риск повредить фасад. Тогда мы приняли решение воспользоваться мобильной лазерной установкой, разработанной ГК «Росатом». С расстояния 60 метров мы подрезали трубу у основания и контролируемо уронили ее на наружную сторону здания. Все операции заняли два дня. Проект был успешно и быстро реализован», — подчеркивает основатель ГК «АРАСАР».
