Демонтаж в условиях промзоны
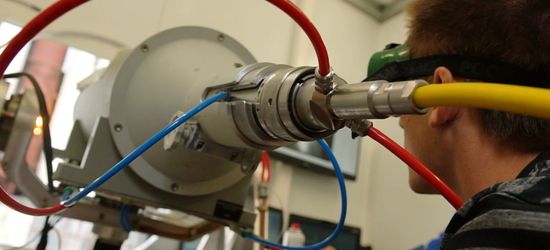
О технологическом процессе демонтажа в условиях действующих промышленных производств рассказывают представители ГК «АРАСАР».
Демонтаж зданий и конструкций в условиях действующих промышленных предприятий имеет свои особенности. Необходимо учитывать производственный процесс в зоне, где будут проходить демонтажные работы, еще более строго соблюдать все требования по безопасности труда и предотвращению аварийных ситуаций.
По словам представителей ГК «АРАСАР», принято выделять два основных этапа проведения демонтажных работ на промпроизводстве. Первый этап — это разработка и согласование проекта производства работ — основного документа, где прописаны все мероприятия в рамках реализации объекта. Второй этап — собственно само производство работ. Из-за действующего производства проблем масса, но уже на стадии разработки ППР компания старается предусмотреть все возможные сложности в работе и отрегулировать их. Также в «АРАСАР» предусмотрен и третий этап — это рециклинг, если он возможен. В частности, демонтированный железобетон дробится в щебень и пускается во вторичное использование.
Самая распространенная задача в таких проектах, отмечают специалисты, — демонтаж фундаментов на действующих производствах при замене оборудования. Так как работы производятся на действующем производстве, то в первую очередь особое внимание уделяется безопасности персонала, далее важна координация работ с другими подрядчиками и персоналом цехов и тщательная предварительная подготовка. Но на первом месте, подчеркивают в «АРАСАР», — в любом случае безопасность и охрана труда.

Немалый опыт компании в демонтажных работах в условиях действующих производств помогает реализовать новые проекты и дает преимущество, отмечают в «АРАСАР». По словам специалистов, основной эффективный способ демонтажа в условиях промышленных предприятий — это технология алмазной резки. Она позволяет быстро разрезать железобетонные конструкции на легко вывозимые части. Организация алмазную резку применяет уже 25 лет. Кроме того, совсем недавно ГК «АРАСАР» первой в мире применила для промышленного демонтажа металлоконструкций технологию лазерной резки. Это абсолютное ноу-хау в демонтаже.
«Интересных проектов работы в промышленном секторе у нас множество, — говорит основатель ГК ”АРАСАР” Александр Штарев. — Расскажу об одном из последних и точно уникальном даже в мировом масштабе проекте — демонтаже железобетонной конструкции на глубине 20 метров под водой на действующей гидроэлектростанции. При реконструкции одного из секторов водосбросной платины наша компания реализовала чрезвычайно сложный проект. Мало того, что работы велись под водой, так еще период их выполнения частично выпал на зиму, а температура в этом регионе достигала минус 35 ℃. А еще мы специально разработали и произвели для этого проекта оборудование, аналога которому в России не производят. В общем, и инженерный персонал компании, и линейный проявили себя на максимальном профессиональном уровне».
Александр Штарев отметил также проект с применением лазера, который был не на действующем производстве, а как опыт в отрасли первым в мире. «На нашем объекте необходимо было произвести демонтаж всех внутренних конструкций здания цеха, оборудования, фундамента, подсобных помещений, а также очистить фасады от металлоконструкций и трубопроводов. Одна из металлических толстостенных труб диаметром почти два метра располагалась в углублении фасада, шла на всю высоту здания и была в аварийном состоянии. Соответственно, альпинистов использовать было нельзя, экскаваторы — тоже, так как был риск повредить фасад. Тогда мы приняли решение воспользоваться мобильной лазерной установкой, разработанной ГК «Росатом». С расстояния 60 метров мы подрезали трубу у основания и контролируемо уронили ее на наружную сторону здания. Все операции заняли два дня. Проект был успешно и быстро реализован», — подчеркивает основатель ГК «АРАСАР».

Сверхгабаритное стекло в архитектуре: вызовы и решения при остеклении
Визуально легкие стеклянные фасады и широкоформатное остекление – многолетний глобальный архитектурный тренд, актуальный и для России. Стекло в формате oversize смотрится очень эффектно: визуально увеличивает пространство и пропускает в помещение много света. И если до недавнего времени крупногабаритное архитектурное стекло приходилось импортировать из Европы, то сегодня активно развиваются не только производственные площадки компаний - производителей архитектурного стекла, но и возможности компаний - переработчиков.
Тем не менее остекление oversize-формата более 6 м пока продолжает считаться сложным процессом: выбрав такое стекло для проекта, можно столкнуться с некоторыми особенностями при транспортировке, переработке и эксплуатации. О том, что необходимо учесть, выбирая сверхгабаритное стекло на проект, рассказывает технический специалист Larta Glass Михаил Голиков.
Вес стеклоизделия. Большой формат означает большой вес, который сильно влияет на остальные составляющие ограждающей светопрозрачной конструкции. Конструкция может не выдержать собственного веса.
Чтобы нивелировать эту проблему, важно подобрать подходящую профильную систему. При выборе профильной системы отталкивайтесь от формулы стеклоизделия или стеклопакета, а не от ограничений профильной системы по возможной толщине заполнения.
Чрезмерный прогиб из-за ветровых нагрузок и недостаточного крепления может привести к потере устойчивости стеклоизделия.
Используйте триплекс и более толстые монолитные стекла, например, толщиной 8, 10 и 12 мм, а также выполняйте специализированный расчет для оценки вероятных значений прогибов и напряжений в стеклоизделии.
Оптические искажения и деформации, влияющие на визуальное восприятие фасада, могут возникнуть после термообработки стекол большого формата и недостаточной толщины.
Чтобы минимизировать эффект деформации, связанный с термообработкой, используйте более толстые наружные стекла. Например, наружное стекло толщиной 12 мм или триплекс из закаленных или термоупрочненных стекол толщиной 10 мм и более.
Энергоэффективность. При остеклении больших проемов важно знать: сопротивление теплопередаче у стены выше, чем у ограждающей светопрозрачной конструкции. Чем больше процент остекления, тем труднее обеспечивать требуемые показатели энергоэффективности.
Применяйте стекла с многофункциональными покрытиями. Они повышают энергоэффективность зданий: пропускают максимум солнечного света и одновременно могут помочь защитить помещение от жары летом и снизить теплопотери зимой. Для достижения оптимального результата можно использовать несколько различных видов стекла.
Переработка. Не все переработчики готовы работать с форматом oversize.
Уточните актуальную информацию по производителям стеклоизделий у регионального менеджера по архитектурным продажам или специалистов технической поддержки клиентов в Larta Glass.
Доступность и ремонтопригодность. Ранее формат oversize был исключительно импортной позицией, что накладывало на заказчика и исполнителей множество вызовов, связанных с доставкой стекла к переработчику или готовых стеклоизделий на объект. Кроме того, разрушение готового изделия на этапе строительства либо в процессе эксплуатации объекта – еще более серьезная проблема. Заказчик может столкнуться с трудностями по доставке аналогичного изделия, а поставщик не всегда может обеспечить своевременную замену. При проектировании остекления в формате oversize важно знать не только переработчиков, но и поставщиков стекол.
Оценивайте риски, выбирая поставщиков, и ориентируйтесь на возможности локальных поставщиков. Например, в линейке продуктов Larta Glass есть стекла с архитектурным покрытием сверхгабаритного формата длиной до 9,5 м. Ширина остается неизменной и равна 3,21 м.
Стекло oversize-формата требует более сложной переработки, но результат того стоит: сочетание сверхгабаритного формата стекла и энергоэффективного покрытия позволит реализовать смелые архитектурные решения и при этом обеспечить соответствие требованиям по энергоэффективности светопрозрачных конструкций.

О компании
Larta Glass — один из крупнейших произво- дителей листового стекла, стекла с покрытием и зеркала в странах СНГ. Три завода компании в Рязани, Раменском и Ростовской области входят в число самых современных предпри- ятий по производству листового стекла.
Стекло, изготовленное на заводах Larta Glass, можно увидеть на объектах в Сочи, спортивных площадках чемпионата мира по футболу, аэропортах Москвы и крупных российских городов и во множестве других проектов.
Испытания подтвердили, что ползучесть при сжатии XPS ТЕХНОНИКОЛЬ CARBON ECO SP не превышает 1,5 %

Специалисты лаборатории строительной физики НИИСФ РААСН провели исследование теплоизоляции XPS ТЕХНОНИКОЛЬ CARBON ECO SP и выяснили, что ползучесть материала при сжатии не превышает 1,5 %.
«В европейских странах производители строительных материалов обязаны указывать значения данного параметра. В России исследование ползучести на сжатие является добровольным, хотя оно имеет ключевое значение для материалов, которые в течение всего срока эксплуатации находятся под воздействием больших нагрузок. Речь прежде всего о теплоизоляции, применяемой в фундаментах, полах и других конструкциях, соприкасающихся с грунтом», — рассказывает Кирилл Парамонов, руководитель технической службы направления «Полимерная изоляция» ТЕХНОНИКОЛЬ.
В ходе испытаний теплоизоляционные плиты в течение определенного времени подвергаются воздействию нагрузки, после чего эксперты оценивают изменения толщины. Максимальный период исследования составляет 608 суток, почти два года, что при проведении интерполяции (пересчета на более долгий срок) соответствует 50 годам эксплуатации. В России подобные испытания практически не проводят, что связано с высокой стоимостью исследования, их долговременностью и риском получить неподходящие результаты.
«Ползучесть при сжатии экструзионного пенополистирола марки CARBON ECO SP не превышает 1,5%, общее уменьшение толщины не превышает 1,5% после 30-кратной экстраполяции на период 50 лет при заданной нагрузке 120 Па, т.е. декларируемый уровень соответствует СС(1,5/1,5/,50)120 согласно ГОСТ 32310-2020», - комментирует Павел Пастушков, руководитель сектора испытаний теплофизических характеристик строительных материалов НИИСФ РААСН, к.т.н.
XPS ТЕХНОНИКОЛЬ CARBON ECO SP применяется в качестве теплоизоляционного слоя в конструкциях плитных фундаментов. В этой сфере надежность, прочность и минимальное водопоглощение являются ключевыми показателями для теплоизоляции.
С учетом того, что заменить теплоизоляцию под фундаментной плитой практически невозможно, важно сохранить ее толщину в течение всего срока эксплуатации.
Испытание на ползучесть при сжатии показало, что в условиях нагрузки от здания надежность и долговечность марки XPS ТЕХНОНИКОЛЬ CARBON ECO SP составляет не менее 50 лет.