Изготовление стекла

Стекло — это неорганический хрупкий материал, используемый в различных сферах повседневной жизни. Изготавливается из разных материалов, от которых зависят его свойства. Разберем подробнее, как именно устроено производство.
Состав стекла
Стекло выполняется чаще всего из сырья, которое проходит плавление при высоких температурах. Основным компонентом выступает песок, хотя в техническом плане это все-таки кварц или диоксид кремния. К нему добавляют прочие составляющие, например:
- кальцинированная сода;
- доломит;
- известняк;
- стеклобой;
- прочие химикаты.
Для производства стекла осуществляется охлаждение компонентов, которые вначале были расплавлены при температуре от +300 до +2500 градусов. Скорость такая, что не допускается формирования заметных кристаллов. Интересно, что для работы бывает достаточно исключительно и песка, но тогда приходится повышать температуру. Именно по этой причине для модификации используется сода. Например, известняк повышает прочность. Оптимальный состав такой: 75% кремнезема, 10% извести и 15% соды.
Какими могут быть изделия из стекла
Изделия из стекла бывают разными. Условно они делятся на такие группы:
- прозрачные и непрозрачные;
- цветные и бесцветные;
- люминесцированные;
- поглощающие или отталкивающие ультрафиолет.
Неорганическое стекло отличается высокими механическими, химическими и тепловыми характеристиками. Стоит отметить, что, хоть материал и очень чувствителен к повреждениям, сопротивление сжатия у него аналогично таковому у чугуна. Повысить прочность можно при помощи закалки, химической или термической обработок. Благодаря этому устраняются микротрещины, которые возникают под воздействием окружающей среды.
В России производство стекла основывается на следующих процессах:
- подготовка сырья;
- формирование шихты;
- варка;
- охлаждение;
- отжиг и обработка.
Все процессы тщательно отработаны, за счет чего готовые изделия получаются высокого качества.
Этапы производства
Чаще всего стекло изготавливается из таких веществ, как кремнезем, SiO2 и Na2CO3. При производственной необходимости составы могут обогащать дополнительными модификаторами. Для осветления, например, берут сульфаты, хлорид натрия, нитрат аммония и так далее. Перед началом изготовления все компоненты просеивают и сушат. Затем их смешивают, пока масса не станет однородной. При необходимости осуществляется дополнительное измельчение.
Далее шихта отправляется в печь, которая применяется специально для варки стекла. Нагревание позволяет испарить остаточные частички воды. В это время происходит разложение абсолютно всех компонентов. По мере увеличения температуры наступает плавление силикатов. В процессе они формируют непрозрачную массу. Заканчивается этот этап сразу после того, как температура доходит до 1200 градусов. В этот момент стекло приобретает прозрачность.
Далее идет стеклообразование. В ходе этого процесса зерна кварца растворяются в силикатном расплаве, в результате чего возникает однородная масса. Идет это несколько медленно, занимает до 90% времени провара шихты. Когда масса достигает температуры 1500-1600 градусов, происходит удаление газов.
Еще один этап производственного процесса — осветление. Для этого добавляются специальные компоненты, которые способствуют уменьшению поверхностного натяжения стекломассы. Расплав хорошо перемешивают специализированным оборудованием. Вместе с этим процессом проводится гомогенезация.
Завершающий этап — охлаждение. Необходимо соблюдать вязкость массы, которая позволит в дальнейшем сформировать требуемую продукцию. Температура в процессе держится на уровне 700-1000 градусов. Тут очень важно медленно и аккуратно ее уменьшать. Создание различных изделий из стекломассы осуществляется механическим способом на специальном оборудовании.
Что такое шихта
Производство стекла стартует уже в карьере. Кварцевый песок необходимо тщательно очистить, чтобы готовое изделие получилось качественным и надежным. Для очистки сырья от посторонних примесей осуществляется промывка с использованием специализированного оборудования. По завершении этого процесса песок сушат и перемещают в вибрационное сито для просеивания. Отбираются те крупинки, диаметр которых не превышает миллиметра.
Полученное сырье направляют уже на производство — в специальное хранилище. Это главный компонент шихты, но, конечно, не единственный. Сейчас при изготовлении стекла нельзя обойтись без добавок, которые укрепят его и придадут некоторые дополнительные свойства. В состав шихты обычно входят следующие компоненты:
- кремнеземное сырье;
- сода;
- доломит;
- кокс, сульфат соды;
- силикат натрия, лития или калия;
- известняк;
- полевой шпат и так далее.
Естественно, перед использованием компоненты тщательно подготавливают и смешивают при определенных условиях. Еще в шихту могут добавлять иногда измельченное битое стекло. Такое сырье не требует никаких дополнительных обработок, что делает производство лишенным отходов.
О стекломассе
Как только смесь будет готова, ее отправляют в печь для варки стекла. Там температура поддерживается на уровне 1600 градусов. По достижении шихтой жидкого состояния, она перемещается в другую часть печи, а на ее место устанавливают новую партию. Интересно, что данный процесс не останавливается. Каждую минуту может подаваться до полутора тонн материала.
На следующем участке температура снижается до 1000 градусов. Материал становится более однородным, из него удаляют газы. По готовности стекломассу оставляют остывать, за счет чего она становится вязкой. Далее можно переходить к формированию.
Силикатное стекло
Силикатное стекло встречается нам каждый день. Из него изготавливают самые разные вещи: посуду, предметы декора, очки, лампы накаливания, окна и многое другое. Производится оно путем плавки двуокиси кремния при температуре 1700 градусов. В итоге получается материал, который характеризуется прекрасной светопропускаемостью, стойкостью к низким температурам и отсутствием взаимодействия с химикатами. Надо отметить, что он еще и хорошо сверлится, полируется или шлифуется.
Силикатное стекло, помимо уже упомянутых сфер, используется в авиации и судостроении. С его использованием изготавливают кабины, делают фонари и устройства, отвечающие за визуальный контроль. Указанный материал прекрасно подходит для изоляции.
Листовое стекло
Для изготовления листового стекла берут два основных компонента — карбонат натрия и кварцевый песок. Масса размещается в специализированной ванне, в которой также находится расплавленное олово. При этом сам материал может быть нескольких типов:
- термостойкий;
- огнестойкий;
- защищенный от воздействия тепла;
- закаленный;
- стойкий к механическим воздействиям;
- ламирированный.
Из этого следует, что листовое стекло можно использовать в разных сферах, но чаще всего — в строительстве или для обустройства автомобилей. В последней отрасли без него обойтись вообще невозможно.
Лобовые стекла
Лобовое стекло необходимо для качественной защиты салона автомобиля от внешних воздействий, проникновения внутрь осадков и пыли. Оно обеспечивает находящимся внутри людям достаточный уровень безопасности. Каждый день технология производство совершенствуется. Чаще всего стекло изготавливают из материала «Триплекс». В таком случае оно будет иметь трехслойную структуру, благодаря которой не разлетится от удара. Осколки будут удержаны армирующей пленкой.
Еще один вариант — «Сталинит». Тут в основе лежит специализированная процедура закаливания, за счет которой прочность стекла значительно повышается. При ударе оно разлетается на мелкие осколки, которые тоже не вредят людям. Но к такому материалу прибегают довольно редко.
Сама технология производства начинается с разметки по конфигурации и геометрическим размерам. Но проводится только надрез, по которому затем продвигается специализированная горелка, согревающая стекло до необходимой температуры. Это приводит к тому, что оно лопается вдоль линии. Затем кромки обрабатываются специализированными абразивными лентами, а материал промывают мыльным раствором для избавления от остатков грязи и пыли. После покрывают раствором, защищающим от слипания.
Как только эти этапы будут пройдены, специалисты проверяют, насколько качественный и крепкий получился материал. Потом два стекла соединяют друг с другом, и им придается необходимая форма, специфическая для конкретной марки автомобиля. Конструкцию кладут в печь, прогреваемую до температуры 760 градусов, что придает стеклу пластичность. Охлаждение проводится аккуратно и медленно, а после затвердевания между заготовками вставляют прозрачную пленку. Все эти процессы, естественно, автоматизированы, так что можно получить несколько идентичных изделий.
Способы производства стекла
Стекло — это твердое вещество, которое активно используется в различных строительных работах. Оно способно пропускать солнечный свет, не давая при этом теплу выйти изнутри. Чаще всего из него изготавливают окна, витрины, перегородки и зеркала. Листовые стекла обрабатывают в специализированных печах, что закаляет его, то есть придает ему увеличенную прочность. Укрепленные варианты нередко применяются для остекления лоджий и балконов. Если вдруг они повредятся, то от них не будет опасных острых осколков.
Современное производство стекла предлагает потребителям различные модели. Существуют даже энергосберегающие, солнцезащитные и армированные. В первом случае применяется тонкое прозрачное покрытие с высокой проводимостью тепла. Свет оно пропускает очень хорошо, что идеально для отопительного сезона.
Солнцезащитные стекла многократно тонируются для достижения идеального результата. Их применяют для фасадов, включают в состав стеклопакетов. Они способствуют повышению комфортности проживания в доме. Иногда встречаются при производстве аквариумов и витражей.
Армированные стекла хороши для обустройства окон или перегородок. Они отличаются высокой стойкостью к огню благодаря наличию специальной сетки из металла.
Изготовление цветного стекла
Цветное стекло может быть изготовлено различными способами, от которых зависит окончательный оттенок. Первая технология предполагает окрашивание в массе. Она довольно проста и практически ничем не отличается от производства обычного материала. В сырье добавляют разные красители, а также обязательно устанавливается строго заданная температура. Минус — высокий расход средств для придания желаемого оттенка.
Вторая технология уже сложнее, зато краситель уходит более экономно. Стекло изготавливается из двух слоев: первый — простой прозрачный лист, второй — либо тонкий крашеный, либо цветная оксидная пленка. Очень важно следить за линейным коэффициентом, он должен быть абсолютно одинаковым.
Особые виды стекла
Существуют особые виды стекла, которые могут использоваться в разных сферах и для разных целей. Разберемся подробнее в этом вопросе:
- Плоское стекло. Чаще всего его используют в окнах, дверях, автомобильных стеклах и так далее. Для изготовления жидкий материл доводится до желаемой толщины, а потом охлаждается и сгибается при необходимости. Стеклопакеты соединяют сразу несколько панелей в одну систему.
- Стеновые стеклоблоки. Для изготовления берут две разных половинки, которые спрессовывают и отжигают вместе. Их используют в архитектурной сфере для обустройства стен, люков и так далее. Стоит отметить, что такие изделия отличаются эстетичностью.
- Бронированное стекло. Оно является пуленепробиваемым и применяется в различных сферах промышленности. Выполняется из многослойного стекла, для изготовления которого прибегают к реализации специальных технологий. Подобный материал идеален для повышения безопасности: например, в ювелирных магазинах, банках.
- Кварцевое стекло. Считается одним из самых ценных. Выполняется из природного кристалла, который измельчают до гранулята и расплавляют. Чаще всего используется для изготовления деталей точной механики — например, кварцевых часов, контейнеров химических реагентов, лабораторного оборудования и так далее.
- Стеклокерамика. Сначала применялась для создания зеркал и креплений телескопов. Сейчас же из нее также изготавливают варочные панели и посуду. Производится путем «контролируемой кристаллизации».
- Светочувствительные стекла. Они позволяют получить картинку через образование микроскопических частиц из металла после воздействия электромагнитного излучения. Считается перспективным для выполнения всевозможных сложных микросхем.
- Стекловолокно. Расправленный материал пропускают через очень тонкие отверстия, в результате чего формируются нити, которые потом сплетаются друг с другом или остаются в пухлом веществе, применяемом для изоляции тепла или звука. Из стекловолокна делают различное спортивное оборудование, корпуса лодок и прочее.
- Жидкое стекло. Используется для заполнения пор и различных недостатков. Оберегает поверхности от воздействия влаги и солнца, а также прочих потенциально опасных факторов.
- Хрусталь. Из этого вида стекла выполняются элементы декора, имеющие красивый блеск.
- Богемское стекло. Производство ведется в Чехии и Силезии. Резка и гравировка производятся вручную.
- Оптическое стекло. Встречается в разных сферах: медицине, астрономии, фотоаппаратуре и так далее. Производство считается довольно сложным процессом, поскольку важна скрупулезная точность и чистота. Обработка осуществляется с помощью алмазных пил. Стандарты должны строго соблюдаться, в противном случае будет брак.
- Гнутое стекло. Зачастую применяется для витрин, необычных полок и мебели. Материал получают посредством медленного нагрева полотна до 650 градусов. Он смягчается и под собственным весом сгибается. Сам процесс занимает от двух до двадцати часов.
Технология производства стекла не стоит на месте и регулярно совершенствуется. Благодаря этому готовые изделия приобретают все более высокое качество. Знание особенностей создания стекла поможет выбрать самый качественный и подходящий для конкретной ситуации вариант.
Спецтехника в дорожном строительстве
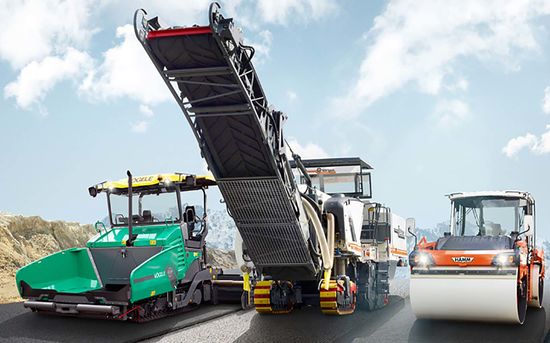
Спецтехника в дорожном строительстве — это механизмы и машины, использующиеся для ремонта и укладки дорожного полотна. Существует несколько основных видов, которые отличаются рядом особенностей по применению.
Наиболее популярная спецтехника
Качество и скорость строительства дорожного полотна зависят не только от используемых материалов, но и от спецтехники. Существует множество машин, которые помогают снижать трудозатраты. К наиболее популярным относят:
- асфальтоукладчики;
- грейдеры;
- катки;
- экскаваторы;
- фрезы;
- кусторезы;
- виброплиты.
Всю специальную техники классифицируют в соответствии с типом выполняемых работ.
Для подготовительных работ
Разравнивать поверхности помогают экскаваторы, грейдеры и кусторезы. Техника делает природный ландшафт ровнее и сглаживает неровности.
Если требуется избавить почву от пней, то применяют корчеватели и рыхлители. Они могут быть в виде самостоятельной техники или использоваться на базе бульдозера. Универсальные машины с разным навесным оборудованием пользуются повышенным спросом.
Автокраны
В дорожных работах часто используют автокраны, так как машины мобильны и работают в ограниченном пространстве. Передвигаются на колесном шасси. Используют их для выгрузки и погрузки:
- монолитных блоков;
- фасованных строительных материалов;
- бревен;
- строительных вагончиков;
- кирпича.
Вид техники для работ выбирают в зависимости от производительности.

Телескопический погрузчик
Телескопический погрузчик — это техника, оснащенная колесным шасси и телескопической стрелой. Машины предназначены для перемещения в ограниченном пространстве. Чтобы повысить устойчивость, используют гидроуправляемые аутригеры, а также электронные системы, которые стабилизируют шасси на неровной поверхности.
Технику применяют для различных задач:
- поднятия людей;
- выравнивания основания;
- планирования территории под строительство объекта;
- перевалки грузов.
Основной рабочий орган машины — телескопическая стрела, которая приводится в движение при помощи гидравлической жидкости. Груз захватывается вилами или аналогичными устройствами. Особенность техники — высокая грузоподъемность и возможность доставать далеко расположенный объект.
Телескопический погрузчик — это отлично защищенная машина, которая оборудована кабиной, выдерживающей падение грузов и опрокидывание. Когда возникает максимально допустимая нагрузка, срабатывает сигнализация. Рабочее место оператора надежно защищено от:
- вибрации;
- ударной нагрузки;
- попадания влаги и пыли;
- шума.
В кабине оператора предусмотрена система отопления и кондиционер.

Грейдер
Грейдер предназначен для выполнения транспортировочных, строительных и земляных работ. Чаще всего используют при укладке асфальта. Особенно незаменима техника в непроходимых местностях:
- посадках;
- заболоченных участках;
- заброшенных локациях.
Машины активно применяют:
- при строительстве аэродромов и автомобильных дорог;
- в мелиорации земель;
- для очистки дорог и улиц от снега;
- при ремонте грунтовой и гравийной дороги.
При помощи грейдера планируют площади и откосы, послойно выравнивают грунт и прочие основания. Транспорт используют при создании:
- насыпей;
- обочин;
- водоотливных каналов;
- откосов.
Также технику используют для очистки территории от снега и мусора.
Грейдеры разделяют по видам. Бывают:
- Полуприцепные и прицепные. Их фиксируют на раме строительной техники или трактора. Отличаются компактными размерами.
- Самоходные. Выпускают на колесном шасси, которое дает возможность машине самостоятельно перемещаться.
Основной рабочий орган техники — отвал. Это стальной лист, который согнут по криволинейному профилю. В нижней части болтами закреплен нож, который режет грунт. По краям находятся боковые ножи. При дополнительной установке кирковщика оператор быстро разрушает старое дорожное полотно и рыхлит почву. На основную раму можно устанавливать снегоочиститель и рабочее оборудование бульдозера.

Экскаватор
Технику используют для:
- выравнивания поверхностей;
- копания котлованов;
- прокладывания коммуникаций;
- строительных работ;
- всех видов дорожных работ;
- погрузки и выгрузки материалов;
- планирования грунта;
- корчевания пней.
Экскаваторы выпускают на гусеничном ходу и колесной части. Каждый тип обладает своими преимуществами.
Машина на гусеничном ходу перемещается и сохраняет работоспособность даже на полном бездорожье. Она не боится грязи, камней и крутых косогоров. Технику используют в местах, где колесные модели не могут полноценно работать. Недостаток — машину требуется доставлять на объект при помощи специального транспорта.
Техника на колесной части может работать в болотистой местности. На объект доставляется самостоятельно.
Основные элементы машины — это экскаваторный и погрузочный ковш. Есть возможность использования дополнительного оборудования:
- гидромолота;
- специфических захватов;
- вилки для поддонов;
- нестандартного оборудования, изготавливающегося на заказ.
По типу управления бывают джойстиковые и рычажные модели. В первом варианте управление более легкое и точное.

Кусторез
Кусторезы используют во время подготовительных работ для расчистки строительной площадки от мелколесья и кустарников. Применяют их при:
- освоении новых земель;
- прокладке трассы;
- устройстве просеки в лесном массиве;
- мелиоративных работах.
Технику для выполнения работ используют в зимнее и летнее время.

Землеройные
Экскаваторы и бульдозеры выравнивают основание и снимают лишний грунт. Производительность машин и мощность техники бывает различной, так как работы проводятся на разных рельефах и типах почвы. Землеройные машины выносливы, долговечны и износоустойчивы. Бывают на гусеничном и колесном ходу.
Землеройная техника не может перемещаться на большой скорости, так как относится к тихоходным машинам. Для доставки их на удаленный объект применяют дополнительный автотранспорт, которые перевозит негабаритные грузы. Его также относят к машинам, которые используют в дорожном строительстве.
Скреперы
Скреперы — техника, которая срезает грунт послойно. Машины бывают самоходными и прицепными. Основной рабочий орган — ковш. Скрепер используют для:
- устройства насыпей и выемок;
- возведения плотин;
- обустройства дамб;
- отрывки котлована;
- уплотнения грунта.
По типу разгрузки техника бывает свободной, полупринудительной и принудительной.

Бульдозеры
Бульдозер — это самоходная техника с ножевым рабочим органом. Машину используют для земельно-транспортных работ. В дорожном строительстве применяют различные типы бульдозеров, которые подходят для всех этапов строительства:
- подготовки грунтового основания;
- устройства песчаного и щебеночного слоя;
- подготовки дорожного покрытия к асфальтированию.
Типовой бульдозер — это базовая машина, в которой спереди расположен навесной металлический отвал. Основная функция машины — послойное срезание грунта и перемещение его на расстояние до 150 м. Также техника:
- разрабатывает грунт;
- возводит насыпи, плотины и дамбы;
- засыпает траншеи после проведения коммуникаций;
- планирует строительные площадки;
- расчищает территорию от кустарников и растительного слоя;
- выкорчевывает пни;
- расчищает завалы на дорогах.
Гусеничный бульдозер создается на базе гусеничного трактора. Основное преимущество — большая проходимость и производительность. Недостаток — низкая скорость и необходимость использования специальной техники для транспортировки к месту работ.
Гусеничные модели чаще всего применяют при проведении землеройных работ. Для устройства слоев дорожного основания используют пневмоколесные бульдозеры, которые создают на базе колесного трактора или тягача. Они более маневренные, но по производительности уступают гусеничным моделям.

Укладывающая и обслуживающая техника
Когда подушка подготовлена, для стабильности основание утрамбовывают. Для этого используют разные технологии: от вибротрамбования до монолитной подушки. Поэтому в дорожном строительстве часто применяют бетоносмеситель.
После того, как основание полностью готово, используют катки и асфальтоукладчики. Они создают финишное покрытие. Для замены дорожного полотна применяют специальные фрезы. Они удаляют верхний слой, который пришел в негодность, выравнивают основание и создают условия для укладки асфальта.
Каток
Каток — это крупная строительная техника, которая утрамбовывает и уплотняет основание из земли, асфальта, гравийно-песчаных смесей.
По типу рабочего органа выделяют:
- комбинированные;
- вальцовые;
- пневмоколесные.
Катки, содержащие внутри вибратор, усиливают степень уплотнения дорожного покрытия без увеличения массы техники. Существуют прицепные модели, использующиеся совместно с трактором.

Заливщик швов
Заливщик швов осуществляет санацию трещин и швов. Используют при мелком ремонте асфальтобетонного покрытия.
Заливщик швов — это одноосный прицеп, на котором установлена термоизолированная емкость, заполненная расплавленным битумом. Внутри постоянно поддерживается температура в пределах 130°-140°С.
Машина для ямочного ремонта
При помощи техники осуществляют ремонт асфальтобетонного полотна, заполняя ямы из смеси битумной эмульсии и щебня. Предварительную подготовку полотна проводить не надо. Отремонтированную дорогу разрешается эксплуатировать сразу после завершения работ.
Асфальтоукладчики
Технику используют для укладки асфальтовой и бетонной смеси на дорожное полотно. Машины выпускают на гусеничном и колесном ходу. Оснащают компьютеризованными устройствами, которые автоматизируют рабочий процесс.
Гусеничные модели массивные и применяются на автомагистралях. Колесная техника более легкая и мобильная. Поэтому используют ее чаще всего в городских стесненных условиях.
Электроника, при минимальном участии оператора, контролирует:
- скорость движения;
- температурный режим и ход подачи асфальтобетонного раствора;
- направление перемещения.
Также у асфальтоукладчика есть выглаживающая доска и трамбующий брус.

Гудронатор
Гудронатор — это автораспределитель битума, который техника в горячем или холодном состоянии равномерно распределяет по дорожному полотну. Устройство, независимо от скорости движения, автоматически поддерживает заданный оператором объем вяжущего вещества на метре квадратном дорожного полотна.

Виброплита
Часто спецтехнику для уплотнения грунта применяют при возведении тротуара. Работу проводят при помощи укатывания и вибрирования. В некоторых трамбующих машинах применяют два варианта.
Виброплита — это легкое устройство, которое используют в дорожном строительстве и ямочном ремонте дорожного покрытия. Механизм помогает трамбовать:
- песок;
- грунт;
- гравий;
- изношенное асфальтовое покрытие;
- гравий.
Модели отличаются по типу приводного двигателя. Бывают:
- Бензиновая виброплита — это наиболее востребованный, доступный по стоимости вариант. Подходит для средних по тяжести работ.
- Виброплита с электромотором. Удобный в использовании инструмент. Недостаток — привязанность к электросети.
- Дизельная виброплита — это мощная и дорогая техника, которую используют профильные предприятия.
Вид и вес виброплиты выбирают, ориентируясь на тип выполняемой работы.

Техника для очистки дорожного покрытия от снега
Технику для очистки дорог оснащают щетками и отвалами. Машины бывают:
- тротуароуборочные;
- снегоуборочные.
Техника очищает дорожное полотно от слежавшегося и свежевыпавшего снега. Используют машины для удаления снежных насыпей на взлетно-посадочных полосах аэродромов и шоссе.
Чаще всего применяют комбинированную технику на базе тракторов или грузовиков. Благодаря возможности смены навесного оборудования машины решают различные задачи. Тем самым заменяют несколько видов узкопрофильной техники.
В таблице указаны типы навесных агрегатов, предназначенных для очистки дорог:
Тип навесных агрегатов |
Описание |
Плужный |
Снежный отвал устанавливают на любую дорожную технику. В летнее время используют для очистки аэродромов и дорог от опавшей листвы, мусора. |
Щеточный |
Предотвращают накапливание снега и увеличение его слоя. В теплое время года щетки применяют для очищения дорожного полотна от грязи и пыли. |
Шнекороторный |
Устройство измельчает снег и подает его к вращающемуся ротору. Обладает большой дальностью отбрасывания. Показывает высокую производительность при уборке сильно слежавшегося и глубокого снега. |
Ветродуйный |
Данный тип используется крайне редко на дорогах и тротуарах, но незаменим для аэродромов. Из техники на высокой скорости выходит холодный поток воздуха, сдувающий весь снег. В теплое время года при помощи устройства очищают территорию от грязи, пыли и опавшей листвы. |
Тепловой |
Тепловое навесное устройство применяют на аэродромах. Благодаря мощному потоку раскаленных газов поверхность полотна быстро высушивается. Остатки снега и льда испаряются. |
Поливальный |
Обрабатывают дорожное полотно жидкими реагентами, которые растворяют лед. |

Техника для производства и транспортировки растворов
Смеси для дорожного полотна изготавливают на заводе. Транспортировку асфальтобетона на объект осуществляют грузовые автомобили, оснащенные специальными кузовами. Чаще всего используют самосвалы.
Бетонные смеси доставляют миксеры. Во время движения в бетономешалке раствор постоянно перемешивается, что дает возможность перевозить его на дальнее расстояние, не теряя качество.
Техника для нанесения дорожной разметки
Техника для нанесения дорожной разметки бывает:
- Универсальной. Отличается большими габаритами. Одновременно наносит несколько линий практически любыми материалами.
- Компактной. Используют для нанесения разметки на небольшой площади.
Машины оснащены приборами, которые автоматически контролируют ширину и толщину наносимой линии. Обладают высокой маневренностью, простотой управления, высоким качеством осуществляемых работ.
Спецтехника существенно упрощает работы и помогает обеспечивать максимальное качество дорожного полотна. В результате частичный или полный ремонт дороги приходится проводить гораздо реже.

Монолитные работы в дорожном строительстве

Монолитное полотно гораздо надежнее асфальтового, но применяют его ограниченно. Связано это с невысоким финансированием, особенностями рельефа и ограниченным объемом необходимых марок цемента. Прежде чем сделать выбор в пользу бетона, изучите его преимущества, правила укладки и эксплуатации.
Преимущества и недостатки монолитных дорог
Достоинства монолитного покрытия:
- Высокая прочность. Не надо проводить ремонтные работы длительное время. Срок эксплуатации дороги — не меньше 40 лет. Асфальтовое покрытие служит 10 лет, при условии ежегодного ремонта. Минимальный износ монолитного покрытия 0,1-0,2 мм в год.
- При строительстве дороги техника расходует меньше топлива, так как в момент движения автомобилей бетон не деформируется.
- Монолитное покрытие устойчиво к резкому изменению климатических условий. Дорожное полотно не портится из-за проливных дождей и резких перепадов температур.
- Монолитная дорога защищает окружающую среду от вредных выбросов, так как горючего при езде по бетонной дороге расходуется меньше. В результате уменьшается выброс в атмосферу выхлопных газов.
- Высокий коэффициент сцепления дорожного основания, который не изменяется при увлажнении.
- Можно вести строительную работу при неблагоприятных условиях.
- Легкость приготовления бетонного раствора и высокая скорость заливки.
- Монолитная дорога обладает хорошей отражающей способностью, поэтому при движении по бетонному полотну у водителя лучше видимость по сравнению с асфальтом, особенно в ночное время.
Основной недостаток покрытия — дороговизна, так как бетон стоит дороже асфальтового варианта. Если повредится монолитное основание, то придется заменять целую плиту. Во время дождя и снегопада дорога становится скользкой.
Материалы
Основной материал для монолитного дорожного строительства — бетон марки М400. Он устойчив к большим нагрузкам, возникающим под действием легковых и грузовых автомобилей.
В таблице указаны основные характеристики и требования к их выполнению:
Характеристики |
Описание |
Прочность на сжатие |
Это способность бетона выдерживать сжимающую нагрузку. Для основы используют марку бетона М300 и выше, для верхнего слоя — от М400. |
Прочность на расширение при изгибе |
Дорожное покрытие — это горизонтальная поверхность, которая подвергается постоянному давлению. Поэтому используют классификацию марок от М5 до М50. |
Морозоустойчивость |
Марку бетона определяют по морозостойкости, которая зависит от климатических условий региона. Для этого берут самый холодный месяц года и рассчитывают среднемесячную температуру. Если климат суровый и температурный режим ниже -15°С, то верхний слой бетона составляет F200, от -5°С до -15°С — F150, от 0° до -5°С — F100. |
Прочность щебня для финишного покрытия |
Не менее 1200 кг/см2. |
Плотность щебня для подушки |
От 800 до 1000 кг/см2. |
Степень подвижности |
При конусном исследовании параметр должен соответствовать уровню 2 см. Для предотвращения отклонения от указанного значения добавляют в состав бетонной смеси минеральные включения. |
Строительство
Монолитную дорогу строят в несколько этапов. Чтобы покрытие получилось качественным, соблюдают все требования, установленные проектной документацией.
Подготовка грунта
В первую очередь проводят подготовительные работы, которые связаны с обработкой грунта. Их начинают после составления проектной документации и геологических исследований региона. Бетонирование осуществляют по горизонтали с изъятием холмов небольшого размера.
Обустраивая крупную автомагистраль, плодородную почву снимают в полном объеме. Если организуют подъезд ко двору, то изымают не более 20 см земли. Созданную подушку уплотняют катком и массивными виброуплотнителями.
На этом этапе делают дренажную систему, которая будет отводить дождевую и грунтовую воду. Для этого создают незначительный уклон 2°-4°. В боковой части дороги фиксируют бетонный желоб и делают откосы.
Подстилочный слой
Песчаную подушку делают толщиной 20-40 см. Подстилка помогает улучшать дренаж и предотвращать размытие грунта при отрицательной температуре. Обязательно делают подушку для дороги на торфяных и глиняных почвах. Чаще всего ее засыпают гравием или крупными камнями, затем выравнивают при помощи катка.
В процессе работ делают запроектированный уклон. Каменную засыпку дополнительно укрепляют цементным раствором. Чем толще получится основание, тем долговечнее будет дорога.

Монтаж опалубки
Для монтажа опалубки используют деревянные доски, высота которых равна уровню заливки смеси. По краю бетона устанавливают ребра жесткости. Все части опалубки обрабатывают специальными растворами, которые помогают быстро отсоединять доски от застывшего материала.
К древесным щитам предъявляются определенные требования по крепости. Если во время строительства задействуют специальную технику, то делают стальную опалубку, обладающую повышенной прочностью и долговечностью. В основе каждого элемента находится подошва с увеличенной устойчивостью к большой нагрузке.
Все секции опалубки должны быть выставлены в одну линию и надежно закреплены. Это условие является обязательным для дорог любых размеров.
Для предотвращения расширения и деформации полотна во время эксплуатации используют армирование металлической сеткой с размером ячеек 150 мм. Работу проводят в процессе заливки. Металлические элементы фиксируют от нижнего уровня на высоте 4 см, предварительно выровняв материал.
Укладка бетона
Укладку бетонного покрытия выполняют в один или несколько этапов. Раствор заливают по периметру. В несколько этапов выполняют процесс, когда проводят армирование.
Бетон быстро затвердевает, поэтому его наносят максимально быстро, при этом сохраняя высокое качество работ. Иначе его эксплуатационные качества ухудшатся. Для заливки автомобильной магистрали используют только заводской бетон, который доставляют на строительную площадку тяжелой спецтехникой.
Основные правила укладки:
- бетон выгружают по 1 м3, затем выравнивают, чтобы получить одинаковую плотность;
- полотно выкладывают в 2 или 3 слоя;
- для уплотнения применяют вибрационное оборудование и специальные механизмы;
- к следующей площадке переходят только после того, как первая обработана.
Если выполняют армирование, то виброприбор размещают на 7 см выше верхнего края. Бетонный раствор используют подвижный и пластичный, но не жидкий. Иначе смесь начнет вытекать через опалубку и потеряет качество.
На готовое монолитное покрытие наносят текстуру, которая напоминает алмазную насечку. Процесс помогает делать поверхность шероховатой.
Нарезка и герметизация температурного шва
Важный этап обустройства дороги — нарезка деформационных швов. Их можно устанавливать после достижения плотности, равной 60%. При меньших показателях полотно не сможет выдержать вес специальной техники и оборудования.
Швы защищают дорогу от повреждений из-за температурного расширения, которое возникает во время сильных морозов. Для распиловки плиты применяют специальные инструменты. Дистанцию между зонами делают согласно проекту. Чаще всего толщину монолита умножают на 30.

Уход
Чтобы защитить монолитное полотно от преждевременного разрушения:
- дорогу для общего пользования открывают не ранее, чем через 28 суток после заливки, так как раствор должен набрать заводскую прочность;
- полотно обрабатывают полимерами, которые создают водонепроницаемую пленку и предотвращают деформацию;
- при возникновении трещин небольшое разрушение заделывают шпатлевкой, крупное — бетонным раствором;
- при появлении разломов снимают весь участок (проблема чаще всего возникает, когда не хватает уплотнения).
При обработке дороги полимерами сцепление колес автомобилей с полотном ухудшается, так как снижается шероховатость. Поэтому на скоростных автомагистралях их используют редко.
Еще один способ профилактики разрушения монолитного полотна — укладка слоя износа. Это значит, что на готовую поверхность наносят асфальт. Он помогает обеспечивать сцепление колес с покрытием и увеличивает срок эксплуатации дороги в несколько раз. Кроме того, стоимость ремонта асфальтобетонного покрытия обходится гораздо дешевле.
Требования к качеству
Качество монолитной дороги регламентирует стандарт СНиП 3.06.03-85 «Автомобильные дороги». Согласно документу, строительная компания должна соблюдать требования:
- Обеспечивать устойчивость к значительным и постоянным механическим нагрузкам. Точное значение определяют в каждом случае индивидуально, учитывая свойства полотна.
- Исключать возможность появления трещин в результате интенсивного использования дороги и сразу после заливки материала. Для этого строго соблюдают технологию монтажа и правильно подбирают соотношение компонентов в бетонной смеси.
- Обеспечивать неуязвимость к действию химических сред и водостойкость. Строительство автомобильной магистрали происходит на разном по качеству грунте и рельефе. Поэтому дорогу защищают от разрушительного действия воды и делают хорошую дренажную систему. Иначе полотно деформируется и станет непригодным для эксплуатации.
Обязательно соблюдают пропорции приготовления раствора для обеспечения максимального качества возводимого покрытия. Монолитная дорога, изготовленная в соответствии со стандартами, выдерживает повышенные нагрузки и не деформируется при увеличенном транспортном потоке.

Транспортировка бетонного раствора
К месту укладки раствор доставляют разные спецсредства. Бетонную смесь подают:
- вагонеткой по колейным путям;
- ленточным транспортером;
- бункером;
- автосамосвалом;
- бадьей по канатной дороге, если строительство проходит в горной местности;
- бетононасосом.
Чаще всего при строительстве монолитного основания для дороги и аэродромного покрытия используют автосамосвалы. Доставляют раствор к месту работ быстро, так как необходимо успеть произвести укладку, уплотнение и отделку до момента схватывания. Требуемые работы выполняют чаще всего в течение двух часов.
Скорость схватывания раствора зависит от температуры воздуха. После приготовления смесь необходимо доставить к месту строительства при:
- 20°-30°С — в течение 30 мин;
- 10°-20°С — не позже, чем через 60 мин;
- 5°-10°С — в течение 120 минут.
У каждого транспортного средства, которое доставляет бетонную смесь, должен быть сопроводительный паспорт (карточка). В документе работник, несущий ответственность за выпуск раствора, указывает:
- время приготовления;
- осадку конуса (подвижности смеси);
- марку цементобетона;
- место укладки.
По паспорту осуществляют контроль продолжительности транспортировки и соответствия марки доставленного цементобетонного раствора, предъявляемым требованиям. Если транспортное средство слишком долго было в пути, и видно, что за оставшееся время специалисты не успеют выполнить комплекс работ, то бетон для укладки полотна не используют. Его отправляют на второстепенные объекты.
Наиболее трудные и энергоемкие процессы при монолитных работах механизированы. Если объект значительно удален от основной базы, то их выполняют вручную. Ориентируясь на принятую технологию и вид сооружения, применяют бетоноукладчик или бетонораздатчик.
Процесс изготовления монолитных плит
Процесс изготовления монолитных плит включает:
- подготовку форм необходимых размеров или выставление опалубочных щитов;
- монтаж арматурного каркаса для улучшения прочности плит;
- заливку бетонной смеси, которую сразу же трамбуют для удаления пузырей воздуха;
- снятие опалубки после застывания раствора.
Готовые плиты оставляют на несколько дней, для набора требуемой прочности.
Где применяют бетонное покрытие
Монолитное покрытие используют для строительства:
- дорог различного типа;
- автомагистралей;
- взлетно-посадочных полос аэродромов;
- разгрузочных площадок в портах;
- причалов;
- прибрежных дорог и набережных;
- тротуаров;
- железнодорожных платформ;
- автобусных остановок.
Используемый в процессе строительства раствор содержит современные добавки, которые повышают плотность, водостойкость, прочность и морозоустойчивость покрытия.

Пластификатор
При строительстве монолитной дороги в раствор добавляют пластификаторы, которые помогают ускорять набор прочности материала. Их применение:
- Повышает подвижность, растекаемость и удобоукладываемость смеси, что приводит к снижению трудозатрат при укладке. В результате получается плотный бетон, в котором образуется меньшее количество пор.
- Обеспечивает удобство при работе с густоармированной конструкцией.
- Увеличивает долговечность бетона и ускоряет набор прочности.
- Предотвращает расслаивание смеси, так как пластификаторы обладают водоредуцирующими свойствами.
- Помогает экономить 10% цемента, что в процессе дорожного строительства составляет огромные суммы.
Пластификаторы продаются в удобной для дозирования форме. Их добавляют в бетон в жидком виде.
Успех проводимых работ
Чтобы строительство монолитной дороги прошло успешно, необходимо:
- Перед началом проведения основных работ произвести пробную укладку. Процесс помогает проверить производительность механизмов и работ, подобрать состав отряда катков, оценить качество и однородность полученной бетонной поверхности.
- Убедиться, что бетонную смесь выпускают на высокопроизводительном бетонном узле. Это позволит обеспечить непрерывную работу специальной техники при равномерной скорости и без остановок, что исключает появление неровностей.
- Рассчитать необходимое количество самосвалов, учитывая производительность растворно-бетонного узла, объема кузова автотранспорта, климатических условий, расстояние транспортировки материала и времени суток. Нельзя, чтобы техника простаивала, ожидая разгрузки.
- Исключить расслоение бетонной смеси при загрузке и выгрузке самосвалов. Поэтому кузов заполняют равномерно, а для укладки используют перегружатели.
- Предохранять раствор от высыхания, укрывая и доставляя материал по графику.
Процесс уплотнения смеси начинают сразу после укладки и завершают в течение часа после того, как бетонная смесь приготовлена. Нарезку швов сжатия производят, когда бетон достигает необходимой прочности, чтобы исключить выкрашивание кромок.
Монолитное покрытие дорог — это прочное и долговечное основание, которое требует минимальных затрат на ремонт и содержание. Появившиеся трещины необходимо сразу же заделывать, иначе они увеличатся в размерах, и придется снимать весь участок монолитного полотна.