Изготовление стекла

Стекло — это неорганический хрупкий материал, используемый в различных сферах повседневной жизни. Изготавливается из разных материалов, от которых зависят его свойства. Разберем подробнее, как именно устроено производство.
Состав стекла
Стекло выполняется чаще всего из сырья, которое проходит плавление при высоких температурах. Основным компонентом выступает песок, хотя в техническом плане это все-таки кварц или диоксид кремния. К нему добавляют прочие составляющие, например:
- кальцинированная сода;
- доломит;
- известняк;
- стеклобой;
- прочие химикаты.
Для производства стекла осуществляется охлаждение компонентов, которые вначале были расплавлены при температуре от +300 до +2500 градусов. Скорость такая, что не допускается формирования заметных кристаллов. Интересно, что для работы бывает достаточно исключительно и песка, но тогда приходится повышать температуру. Именно по этой причине для модификации используется сода. Например, известняк повышает прочность. Оптимальный состав такой: 75% кремнезема, 10% извести и 15% соды.
Какими могут быть изделия из стекла
Изделия из стекла бывают разными. Условно они делятся на такие группы:
- прозрачные и непрозрачные;
- цветные и бесцветные;
- люминесцированные;
- поглощающие или отталкивающие ультрафиолет.
Неорганическое стекло отличается высокими механическими, химическими и тепловыми характеристиками. Стоит отметить, что, хоть материал и очень чувствителен к повреждениям, сопротивление сжатия у него аналогично таковому у чугуна. Повысить прочность можно при помощи закалки, химической или термической обработок. Благодаря этому устраняются микротрещины, которые возникают под воздействием окружающей среды.
В России производство стекла основывается на следующих процессах:
- подготовка сырья;
- формирование шихты;
- варка;
- охлаждение;
- отжиг и обработка.
Все процессы тщательно отработаны, за счет чего готовые изделия получаются высокого качества.
Этапы производства
Чаще всего стекло изготавливается из таких веществ, как кремнезем, SiO2 и Na2CO3. При производственной необходимости составы могут обогащать дополнительными модификаторами. Для осветления, например, берут сульфаты, хлорид натрия, нитрат аммония и так далее. Перед началом изготовления все компоненты просеивают и сушат. Затем их смешивают, пока масса не станет однородной. При необходимости осуществляется дополнительное измельчение.
Далее шихта отправляется в печь, которая применяется специально для варки стекла. Нагревание позволяет испарить остаточные частички воды. В это время происходит разложение абсолютно всех компонентов. По мере увеличения температуры наступает плавление силикатов. В процессе они формируют непрозрачную массу. Заканчивается этот этап сразу после того, как температура доходит до 1200 градусов. В этот момент стекло приобретает прозрачность.
Далее идет стеклообразование. В ходе этого процесса зерна кварца растворяются в силикатном расплаве, в результате чего возникает однородная масса. Идет это несколько медленно, занимает до 90% времени провара шихты. Когда масса достигает температуры 1500-1600 градусов, происходит удаление газов.
Еще один этап производственного процесса — осветление. Для этого добавляются специальные компоненты, которые способствуют уменьшению поверхностного натяжения стекломассы. Расплав хорошо перемешивают специализированным оборудованием. Вместе с этим процессом проводится гомогенезация.
Завершающий этап — охлаждение. Необходимо соблюдать вязкость массы, которая позволит в дальнейшем сформировать требуемую продукцию. Температура в процессе держится на уровне 700-1000 градусов. Тут очень важно медленно и аккуратно ее уменьшать. Создание различных изделий из стекломассы осуществляется механическим способом на специальном оборудовании.
Что такое шихта
Производство стекла стартует уже в карьере. Кварцевый песок необходимо тщательно очистить, чтобы готовое изделие получилось качественным и надежным. Для очистки сырья от посторонних примесей осуществляется промывка с использованием специализированного оборудования. По завершении этого процесса песок сушат и перемещают в вибрационное сито для просеивания. Отбираются те крупинки, диаметр которых не превышает миллиметра.
Полученное сырье направляют уже на производство — в специальное хранилище. Это главный компонент шихты, но, конечно, не единственный. Сейчас при изготовлении стекла нельзя обойтись без добавок, которые укрепят его и придадут некоторые дополнительные свойства. В состав шихты обычно входят следующие компоненты:
- кремнеземное сырье;
- сода;
- доломит;
- кокс, сульфат соды;
- силикат натрия, лития или калия;
- известняк;
- полевой шпат и так далее.
Естественно, перед использованием компоненты тщательно подготавливают и смешивают при определенных условиях. Еще в шихту могут добавлять иногда измельченное битое стекло. Такое сырье не требует никаких дополнительных обработок, что делает производство лишенным отходов.
О стекломассе
Как только смесь будет готова, ее отправляют в печь для варки стекла. Там температура поддерживается на уровне 1600 градусов. По достижении шихтой жидкого состояния, она перемещается в другую часть печи, а на ее место устанавливают новую партию. Интересно, что данный процесс не останавливается. Каждую минуту может подаваться до полутора тонн материала.
На следующем участке температура снижается до 1000 градусов. Материал становится более однородным, из него удаляют газы. По готовности стекломассу оставляют остывать, за счет чего она становится вязкой. Далее можно переходить к формированию.
Силикатное стекло
Силикатное стекло встречается нам каждый день. Из него изготавливают самые разные вещи: посуду, предметы декора, очки, лампы накаливания, окна и многое другое. Производится оно путем плавки двуокиси кремния при температуре 1700 градусов. В итоге получается материал, который характеризуется прекрасной светопропускаемостью, стойкостью к низким температурам и отсутствием взаимодействия с химикатами. Надо отметить, что он еще и хорошо сверлится, полируется или шлифуется.
Силикатное стекло, помимо уже упомянутых сфер, используется в авиации и судостроении. С его использованием изготавливают кабины, делают фонари и устройства, отвечающие за визуальный контроль. Указанный материал прекрасно подходит для изоляции.
Листовое стекло
Для изготовления листового стекла берут два основных компонента — карбонат натрия и кварцевый песок. Масса размещается в специализированной ванне, в которой также находится расплавленное олово. При этом сам материал может быть нескольких типов:
- термостойкий;
- огнестойкий;
- защищенный от воздействия тепла;
- закаленный;
- стойкий к механическим воздействиям;
- ламирированный.
Из этого следует, что листовое стекло можно использовать в разных сферах, но чаще всего — в строительстве или для обустройства автомобилей. В последней отрасли без него обойтись вообще невозможно.
Лобовые стекла
Лобовое стекло необходимо для качественной защиты салона автомобиля от внешних воздействий, проникновения внутрь осадков и пыли. Оно обеспечивает находящимся внутри людям достаточный уровень безопасности. Каждый день технология производство совершенствуется. Чаще всего стекло изготавливают из материала «Триплекс». В таком случае оно будет иметь трехслойную структуру, благодаря которой не разлетится от удара. Осколки будут удержаны армирующей пленкой.
Еще один вариант — «Сталинит». Тут в основе лежит специализированная процедура закаливания, за счет которой прочность стекла значительно повышается. При ударе оно разлетается на мелкие осколки, которые тоже не вредят людям. Но к такому материалу прибегают довольно редко.
Сама технология производства начинается с разметки по конфигурации и геометрическим размерам. Но проводится только надрез, по которому затем продвигается специализированная горелка, согревающая стекло до необходимой температуры. Это приводит к тому, что оно лопается вдоль линии. Затем кромки обрабатываются специализированными абразивными лентами, а материал промывают мыльным раствором для избавления от остатков грязи и пыли. После покрывают раствором, защищающим от слипания.
Как только эти этапы будут пройдены, специалисты проверяют, насколько качественный и крепкий получился материал. Потом два стекла соединяют друг с другом, и им придается необходимая форма, специфическая для конкретной марки автомобиля. Конструкцию кладут в печь, прогреваемую до температуры 760 градусов, что придает стеклу пластичность. Охлаждение проводится аккуратно и медленно, а после затвердевания между заготовками вставляют прозрачную пленку. Все эти процессы, естественно, автоматизированы, так что можно получить несколько идентичных изделий.
Способы производства стекла
Стекло — это твердое вещество, которое активно используется в различных строительных работах. Оно способно пропускать солнечный свет, не давая при этом теплу выйти изнутри. Чаще всего из него изготавливают окна, витрины, перегородки и зеркала. Листовые стекла обрабатывают в специализированных печах, что закаляет его, то есть придает ему увеличенную прочность. Укрепленные варианты нередко применяются для остекления лоджий и балконов. Если вдруг они повредятся, то от них не будет опасных острых осколков.
Современное производство стекла предлагает потребителям различные модели. Существуют даже энергосберегающие, солнцезащитные и армированные. В первом случае применяется тонкое прозрачное покрытие с высокой проводимостью тепла. Свет оно пропускает очень хорошо, что идеально для отопительного сезона.
Солнцезащитные стекла многократно тонируются для достижения идеального результата. Их применяют для фасадов, включают в состав стеклопакетов. Они способствуют повышению комфортности проживания в доме. Иногда встречаются при производстве аквариумов и витражей.
Армированные стекла хороши для обустройства окон или перегородок. Они отличаются высокой стойкостью к огню благодаря наличию специальной сетки из металла.
Изготовление цветного стекла
Цветное стекло может быть изготовлено различными способами, от которых зависит окончательный оттенок. Первая технология предполагает окрашивание в массе. Она довольно проста и практически ничем не отличается от производства обычного материала. В сырье добавляют разные красители, а также обязательно устанавливается строго заданная температура. Минус — высокий расход средств для придания желаемого оттенка.
Вторая технология уже сложнее, зато краситель уходит более экономно. Стекло изготавливается из двух слоев: первый — простой прозрачный лист, второй — либо тонкий крашеный, либо цветная оксидная пленка. Очень важно следить за линейным коэффициентом, он должен быть абсолютно одинаковым.
Особые виды стекла
Существуют особые виды стекла, которые могут использоваться в разных сферах и для разных целей. Разберемся подробнее в этом вопросе:
- Плоское стекло. Чаще всего его используют в окнах, дверях, автомобильных стеклах и так далее. Для изготовления жидкий материл доводится до желаемой толщины, а потом охлаждается и сгибается при необходимости. Стеклопакеты соединяют сразу несколько панелей в одну систему.
- Стеновые стеклоблоки. Для изготовления берут две разных половинки, которые спрессовывают и отжигают вместе. Их используют в архитектурной сфере для обустройства стен, люков и так далее. Стоит отметить, что такие изделия отличаются эстетичностью.
- Бронированное стекло. Оно является пуленепробиваемым и применяется в различных сферах промышленности. Выполняется из многослойного стекла, для изготовления которого прибегают к реализации специальных технологий. Подобный материал идеален для повышения безопасности: например, в ювелирных магазинах, банках.
- Кварцевое стекло. Считается одним из самых ценных. Выполняется из природного кристалла, который измельчают до гранулята и расплавляют. Чаще всего используется для изготовления деталей точной механики — например, кварцевых часов, контейнеров химических реагентов, лабораторного оборудования и так далее.
- Стеклокерамика. Сначала применялась для создания зеркал и креплений телескопов. Сейчас же из нее также изготавливают варочные панели и посуду. Производится путем «контролируемой кристаллизации».
- Светочувствительные стекла. Они позволяют получить картинку через образование микроскопических частиц из металла после воздействия электромагнитного излучения. Считается перспективным для выполнения всевозможных сложных микросхем.
- Стекловолокно. Расправленный материал пропускают через очень тонкие отверстия, в результате чего формируются нити, которые потом сплетаются друг с другом или остаются в пухлом веществе, применяемом для изоляции тепла или звука. Из стекловолокна делают различное спортивное оборудование, корпуса лодок и прочее.
- Жидкое стекло. Используется для заполнения пор и различных недостатков. Оберегает поверхности от воздействия влаги и солнца, а также прочих потенциально опасных факторов.
- Хрусталь. Из этого вида стекла выполняются элементы декора, имеющие красивый блеск.
- Богемское стекло. Производство ведется в Чехии и Силезии. Резка и гравировка производятся вручную.
- Оптическое стекло. Встречается в разных сферах: медицине, астрономии, фотоаппаратуре и так далее. Производство считается довольно сложным процессом, поскольку важна скрупулезная точность и чистота. Обработка осуществляется с помощью алмазных пил. Стандарты должны строго соблюдаться, в противном случае будет брак.
- Гнутое стекло. Зачастую применяется для витрин, необычных полок и мебели. Материал получают посредством медленного нагрева полотна до 650 градусов. Он смягчается и под собственным весом сгибается. Сам процесс занимает от двух до двадцати часов.
Технология производства стекла не стоит на месте и регулярно совершенствуется. Благодаря этому готовые изделия приобретают все более высокое качество. Знание особенностей создания стекла поможет выбрать самый качественный и подходящий для конкретной ситуации вариант.
На чем не стоит экономить во время ремонта?
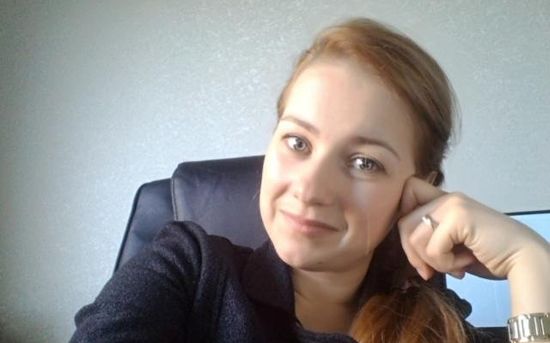
Юлия Курова, руководитель продуктового направления компании «Теплолюкс» поделилась советами, на чем лучше не экономить во время ремонта и рассказала, как продукты Теплолюкс позволят избежать незапланированных трат.
Комплексный ремонт обычно всегда подразумевает большие финансовые и временные затраты, поэтому многих интересует вопрос, на чём же можно сэкономить, сохранив при этом достойное качество.
В первую очередь важно понимать, что экономить не стоит на тех вещах, которые, во-первых, влияют на безопасность, во-вторых, при поломке могут повлечь за собой гораздо более высокие траты. К такой категории можно отнести систему защиты от протечки воды. Зачастую, покупая квартиру с готовой сантехникой или проводя ремонт в старом доме, не известно, насколько качественно выполнены сантехнические работы, более того, даже если вы проводили эти работы самостоятельно или вместе с вашей строительной бригадой, риск протечек всегда есть.
Система защиты от протечки позволит предотвратить гораздо бОльший ущерб в случае затопления – как минимум поможет быстро устранить протечку и не испортить интерьер вашей ванной комнаты, как максимум сохранить ремонт близлежащих комнат и не затопить соседей снизу.
Как работает система? В местах, куда вода может попасть в первую очередь (под раковиной, унитазом, ванной), устанавливаются датчики протечки. На трубы монтируются шаровые краны. При попадании воды на датчик сигнал поступает на модуль, после происходит автоматическое перекрытие подачи водоснабжения за несколько секунд. Также оповещение поступит и на смартфон, после чего Вы максимально быстро сможете отреагировать на сложившуюся ситуацию.
Чем может обернуться подобная экономия? Если у вас или ваших соседей сверху хоть раз протекали трубы, вы знаете, сколько проблем это может доставить. Чтобы устранить последствия протечки, придётся потратить не только время и деньги, но и нервы. А в нынешних реалиях стоимость Вашего ремонта и соседей снизу несоизмеримо выше стоимости оборудования и монтажа системы защиты от протечки. Её можно купить от 16 тысяч рублей, и, если она сработает даже один раз – экономия на вынужденном ремонте и беспокойствах очевидна. Особенно, если вы живете на высоком этаже в многоквартирном доме.
Также с системой защиты от протечки можно хорошо сэкономить, если в квартире два стояка в разных санузлах (сейчас в большинстве новых квартир это именно так), то установить краны системы защиты от протечек можно в холле в водяном распределительном пункте – понадобится всего два крана, а не четыре. Это сохранит более 10 тысяч рублей.
Ещё одним продуктом, на котором всё-таки не стоит экономить, если вы хотите его установить, являются тёплые полы. В сравнении со стоимостью полноценного ремонта, система тёплых полов обойдётся недорого, а удовольствия и комфорта от неё во много раз больше. Если купить самую дешёвую систему тёплого пола, то через пару лет она может выйти из строя или работать с перебоями, а менять всю систему уже слишком дорого, так как для этого придётся снова разбирать весь пол и менять электрику. В случае с тёплым полом можно сэкономить на терморегуляторе, купив программируемый вместо дешевого механического – при нынешней цене на электричество, он окупится меньше, чем через год, а это 2-3 тысячи рублей.
В дополнение можно сказать, что все инженерные системы, которые могут потребовать ремонта или замены: электрика, отопление, вентиляция и др., должны быть установлены так, чтобы к ним был свободный доступ инструментами. Лучше всего рассмотреть несколько вариантов, выбрать среди них оптимальный, адаптировать его к персональным условиям. Поиск наилучшего решения требует времени, но зато в дальнейшем окупится удобством эксплуатации и надёжностью безопасности жильцов.
Как снизить ущерб от коррозии металла и сократить затраты на обслуживание трубопроводов на 10%?

Каждая шестая домна в России сегодня работает «впустую» по одной причине: коррозия съедает около 10% всего производимого металла[1]. Проблема коррозии под изоляцией обостряется с каждым годом, так как эксплуатируемые металлические изделия стареют, а количество разрушающих факторов увеличивается. В результате коррозия становится причиной колоссального экологического и экономического ущерба. Совсем избежать самопроизвольного разрушения металлов невозможно, но есть способы замедлить процесс. О том, как это сделать, рассказали в компании ROCKWOOL Россия. Эксперты компании с 2015 года прицельно исследуют проблематику возникновения коррозии под изоляцией.
Чем опасна коррозия металла?
Негативные последствия коррозии связаны с существенным увеличением затрат на эксплуатацию промышленного оборудования и устранение последствий разрушения металлов, а также с серьезными рисками для экологии и безопасности людей.
Так, если говорить об экономической стороне проблемы, то ущерб от коррозии и затраты на борьбу с ней составляют 3-4% ВВП в США и Германии, а в России — более 5%. Из-за коррозии трубопроводов и оборудования под изоляцией сокращается потенциальный срок службы промышленных объектов, а вынужденные приостановки на ремонт снижают эффективность и увеличивают потери бизнеса. Так, час простоя может стоить до 20 тысяч долларов.
Эксперты ROCKWOOL добавляют, что 60% аварийных ситуаций с трубопроводами происходят вследствие коррозии металла. При этом стоимость ремонта может составлять до 300 тысяч рублей на один метр трубы. В среднем на ремонт повреждений от коррозии под изоляцией уходит около 10% от общего бюджета на обслуживание трубопроводов.
С точки зрения экологической безопасности и рисков для населения серьезные опасения вызывают возможные последствия из-за производственных аварий по причине коррозии. По данным Росприроднадзора, основная причина утечек из резервуаров и трубопроводов — это коррозионные повреждения. Так, в 2020 году из-за коррозии на трубопроводе Оха-Комсомольск-на-Амуре произошел разлив нефтесодержащей жидкости на площади 0,4 га.
К сожалению, коррозия металла приводит не только к экологическим катастрофам, но и к гибели людей. Один из самых резонансных случаев произошел в 2020 году в Перми: в результате прорыва теплотрассы погибли пять человек. Как сообщили в Ростехнадзоре, причиной аварии стал локальный коррозионный износ участка трубопровода вследствие старения антикоррозионного изоляционного покрытия.
Почему возникает коррозия?
В появлении коррозии всегда так или иначе виновата влага, однако ее влияние может быть разным, например:
- общая и точечная коррозия углеродистой стали возникает при контакте влажной среды и углеродистой стали;
- коррозионное растрескивание под действием внешних напряжений нержавеющей стали происходит из-за воздействия водорастворимых хлоридов из воды.
По оценкам ученых, в последние годы появились дополнительные факторы, которые провоцируют новые ЧП из-за самопроизвольного разрушения металлов. В частности, это интенсивное развитие трубопроводной сферы, нефтяной, химической и нефтехимической промышленности, а также устаревание существующего оборудования и несвоевременный ремонт. Кроме того, по словам академика РАН Евгения Каблова, к таким факторам можно отнести и появление новых видов бактерий.
«Воздействие отдельных бактерий привело к тому, что интенсивность коррозии увеличилась на 20–30%. Даже нержавеющие материалы, которые никогда не корродировали, эти бактерии прожигают, как лазер. Они передвигаются по металлической поверхности, и продукты их жизнедеятельности разрушают нержавейку», — рассказывает Евгений Каблов.
Не последнюю роль в возникновении коррозии играет и промышленная изоляция. Сегодня абсолютное большинство трубопроводов изолируются, чтобы снизить теплопотери. И именно под слоем изоляции зачастую и начинается разрушение металла.
Как снизить риски коррозии под изоляцией
Коррозия под изоляцией — это наружная коррозия трубопроводов или оборудования, которая появляется под внешней обшивкой изделия из-за проникновения влаги. Это одна из самых опасных и коварных разновидностей разрушения металла. Дело в том, что очаги коррозии в таких ситуациях скрыты изоляцией и их нелегко вовремя обнаружить. В лучшем случае проблема вскрывается при снятии изоляции во время очередной проверки, в худшем — уже при аварии. Наиболее высокий риск возникновения коррозии возникает на трубопроводах, работающих в циклическом режиме (нагрев-остывание).
О предотвращении коррозии нужно задумываться еще на этапе проектирования. Есть четыре ключевых правила:
- Трубопроводы и оборудование должны проектироваться так, чтобы положение опор, фитингов и прочего максимально способствовало отведению воды.
- На трубопроводы и оборудование необходимо наносить подходящее антикоррозионное покрытие и регулярно проверять его состояние в рамках плана техобслуживания.
- Необходимо выбрать подходящий изоляционный слой, который будет соответствовать назначению и не станет источником дополнительной коррозии.
- Следует подобрать оптимальную систему защиты от атмосферных воздействий. Она должна соответствовать назначению, сочетаться с установленной под ней изоляцией и регулярно проверяться.
Как выбрать подходящую изоляцию?
Обычно при выборе изоляции для трубопроводов и другого оборудования подрядчики уделяют внимание ее теплопроводности и максимальной температуре эксплуатации. Однако для снижения рисков коррозии под изоляцией этого недостаточно, важно учесть причины ее появления. Их всего три: материал впитывает влагу, плохо выводит влагу или же не соответствует по химическому составу. Таким образом, правильная изоляция не должна влиять на стальную конструкцию, поглощать воду и задерживать пар.
«Есть три параметра, которые непосредственно влияют на саморазрушение металла под изоляцией. Во-первых, это химическая инертность: коррозия стали ускоряется, если из изоляционного материала можно выделить кислотные соединения. Поэтому водная вытяжка из изоляционного материала должна быть слегка щелочной. Во-вторых, это содержание хлоридов. Они могут выщелачиваться и приводить к растрескиванию под внешним напряжением. Уровень содержания подверженных водному выщелачиванию хлоридов в изоляционном материале должен быть выше 10 мг/кг. В-третьих, это водоотталкивающее свойство: водопоглощение должно быть не более 1 кг/м2», — рассказывает Роман Бочков, менеджер по развитию направления Техническая изоляция и Огнезащита компании ROCKWOOL Россия.
Национальная ассоциация инженеров-коррозионистов (NACE) провела ряд испытаний, чтобы проверить, какие именно изоляционные материалы соответствуют перечисленным свойствам. Оказалось, что самый оптимальный вариант для промышленного применения — это каменная вата. Во время испытаний этот материал показал самую низкую площадь повреждения поверхности: всего 32%, в то время как у изоляции из стекловаты этот показатель составил 42%, у пеностекла — 70%, а у ПИР — все 100%. Максимальная глубина повреждения металла при изоляции каменной ватой тоже оказалась самой низкой (всего 40 мкм), а максимальная скорость коррозии — самой медленной из всех (0,5 мм в год)[2].
Аналогичные испытания провела и лаборатория МГУ: каменную вату с содержанием водорастворимых хлоридов менее 10 мг/кг сравнили с каменной ватой с высоким содержанием хлоридов, а также со стеклянной ватой, синтетическим каучуком, пеностеклом и пенополиуретаном. Среди всех перечисленных материалов для промышленной изоляции лучшие результаты продемонстрировал первый образец: скорость коррозии при использовании каменной ваты с низким содержанием водорастворимых хлоридов составила всего 0,23 мм в год. Для сравнения: под изоляцией из каучука коррозия развивается со скоростью 0,52 мм в год, а под пенополиуретаном — 0,75 мм в год.
«Мы регулярно проводим собственные исследования проблематики возникновения коррозии под изоляцией, ориентируясь, в том числе и на рекомендации NACE. Результатом этой работы стала специализированная линейка прошивных матов и навивных цилиндров из каменной ваты ProRox с низким содержанием водорастворимых хлоридов (меньше 10 мг/кг). Испытания показали, что применение такой изоляции увеличивает ресурс трубопроводов от 11 до 17 % по сравнению с изоляцией из каменной ваты с высоким содержанием водорастворимых хлоридов», — добавляет Роман Бочков.
Прошивные маты и цилиндры ProRox гидрофобизированы, что обеспечивает эффективную защиту от проникновения влаги по всей толщине её слоя. Кроме того, она не препятствует проходу пара, что снижает риск образования конденсата. Такая изоляция доказывает свою эффективность даже на предприятии в условиях Крайнего Севера.
Коррозия металла — неизбежный процесс, однако это не повод оставить попытки и прекратить бороться с ней. Современные разработки предлагают эффективные методы защиты технических сооружений от подобных повреждений и позволяют существенно снизить скорость саморазрушения металлов. А значит — избежать колоссального ущерба.
[1] По данным Института физической химии РАН, https://tribune-scientists.ru/articles/357
[2] ASTM – G189-07 Standard Guide for Laboratory Simulation of Corrosion Under Insulation. Испытания NACE