Монтаж опалубки монолитных составляющих здания
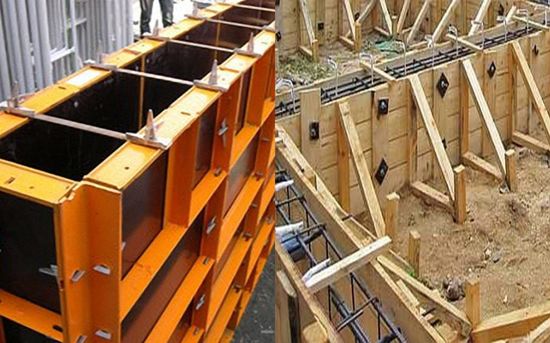
Установка опалубки необходима для качественной заливки бетонного раствора. Такая конструкция устанавливается при формировании фундамента или возведения бетонных стен здания. От качества проведенной работы зависит прочность основания будущей постройки и внешний вид помещения. Работа по созданию опалубки не отличается сложностью, но требует ответственного подхода.
Правила установки опалубки
Любая опалубка состоит из щитов и блоков, укрепленных специальными опорами. С учетом используемого материала и типа изделия сборка каждой конструкция имеет свои нюансы. При этом существуют общие правила, которых необходимо придерживаться во время монтажа. Они выражаются в следующем:
- Перед началом сборки строительная площадка должна быть полностью очищена от мусора.
- Если поверхность грунта имеет неровную плоскость, то необходимо срезать слой почвы. Подсыпание щебня недопустимо.
- Работу по установке маяков следует начинать с углов. При этом тщательно проверить их на вертикальность и горизонтальность.
- Заливка раствора должна проводиться только после того, когда конструкция будет проверена на герметичность.
При формировании деревянных опалубок необходимо тщательно подгонять доски. Кроме стыков следует устранять все отверстия в древесине, которые могут возникнуть в результате выпадение сучков. Выявленные щели требуется забивать паклей.
Конструкция для фундамента
Поскольку любой фундамент служит основанием для здания, качеству его изготовления уделяется повышенное внимание. Правильно сделанная опалубка позволяет существенно снизить расход бетона и сформировать ровное основание.
На предварительном этапе следует хорошо ознакомиться с проектом. Также нужно обратить внимание на время проведения работ и не начинать закладку фундамента в морозный период.
Составляющие конструкции
В качестве материала для опалубки могут быть использованы доски, щиты или фанера. Главное, чтобы стенки были способны воспринимать и удерживать нагрузку от давления раствора. При этом должны соблюдаться следующие условия:
- Используемые щиты могут быть квадратной или прямоугольной формы, а их размеры произвольными.
- Стенки опалубки должны быть укреплены с помощью горизонтальных распорок.
- Внутри конструкции обязательно прокладывается гидроизоляция, препятствующая вытеканию цементного раствора.
Если в качестве исходного материала применяется фанера, то ее толщина должна быть порядка 15 мм. Когда для работы используются доски, они берутся толщиной 40 мм. Иногда опалубка изготавливается из пластика. Этот материал прочен и долговечен, но имеет высокую стоимость. Приобретать такие изделия можно только в том случае, когда расчет ведется на их многоразовое использование.

Процедура установки
Монтаж опалубки состоит из следующих шагов:
- На выделенном участке расчищается площадка, и на ней откладываются расчетные величины.
- Выкапывается нужных размеров траншея.
- Сбивается необходимых параметров опалубка.
- Сначала в вырытую траншею укладывается внешний ряд сбитых досок.
- Затем устанавливается второй ряд, и между ними вставляются заранее приготовленные распорки.
- Над вырытой траншеей устанавливается второй ряд опалубки на заданную высоту фундамента.
- После проверки вертикальности все расположенные сверху щиты скрепляются поперечинами.
- На последней стадии опалубка укрепляется наклонными распорками.
Вся внутренняя часть собранной опалубки устилается пленкой, которая предотвращает вытекание из различных щелей залитого внутрь бетона. Такая необходимость возникает потому, что даже надежные распорки не в состоянии противостоять давлению раствора.
Опалубка для стен
В отличие от фундамента, бетонные стены здания имеют значительные параметры, поэтому установленная опалубка должна обладать большой прочностью. Для ее изготовления могут быть использованы листы OSB, металл, пенополистирол, доски или фанера.
Устанавливаемая опалубка бывает следующих видов:
- Съемная. Обычно изготавливается из обработанных досок или металла. Затем она убирается после схватывания раствора.
- Несъемная. Изготавливается из теплоизоляционных материалов, поскольку она не убирается после окончания работы. В результате здание утепляется, а также у него увеличивается звукоизоляция.
Перед изготовлением опалубки проводятся расчеты, где за основу берутся следующие исходные данные:
- объем заливаемого пространства;
- размер толщины стен.
При расчете конструкций опалубки принимаются во внимание следующее параметры:
- ее несущая способность;
- количество необходимого материала на изготовление;
- технология возведения для конкретного случая;
- стоимость опалубки.
На основании полученных данных определяется количество необходимых опор, которые будут противостоять деформационным изменениям конструкции.

Съемный вариант из древесины
Деревянная опалубка состоит из щитов, в свою очередь состоящих из сбитых досок. В отличие от фундаментной конструкции, данные изделия имеют увеличенные параметры. Если используется ОSВ, то такие изделия должны обладать высокой влагостойкостью.
В качестве фиксации установленных щитов применяется брус, который также выступает как ребро жесткости. Все части опалубки между собой скрепляются проволочными скрутками или стяжками. Наружная часть опалубки фиксируется в неподвижном положении с помощью хомутов, колышков, подкосов или прижимных досок.
Основным условием при формировании опалубки является отсутствие промежутков между досками. Их допустимая величина не должна составляет больше 3 мм. При выходе за эти пределы во время трамбовки бетонной смеси раствор начнет выдавливаться через большие щели. В некоторых случаях выходит только вода, но это тоже является негативным явлением, поскольку понижается качество цементного материала. Для устранения такого явления большого размера зазоры заделываются паклей или прибитыми снаружи деревянными рейками.

Съемная конструкция из металла
Опалубкой для бетонной стены может служить листовой прокат, который имеет толщину до 1,5 мм. Здесь жестким основанием служит каркас, изготовленный из трубы с приваренными уголками. Крепление листа к нему осуществляется с помощью сварки или саморезов. Данная конструкция является съемной.
Также существует и несъемный вариант металлической опалубки, который предполагает формирование обрешетки. В этом случае размер ячеек имеет форму квадрата со стороной 0,2-0,4 м. Их размер зависит от толщины используемого металлического листа.
Для усиления жесткости в верхней части опалубки устанавливаются перемычки, которые устраняют риск расхождения щитов. Во внутренней части пространства прокладываются трубы, служащие каналами для будущих коммуникационных систем.
После заливки раствора требуется зафиксировать положение щитов в неподвижном состоянии. Для этого с обеих сторон под углом устанавливаются распорки, в качестве которых могут служить деревянные балки или металлические трубы.

Процедура демонтажа
Любая съемная конструкция после застывания раствора убирается. Обычно период ожидания составляет от несколько дней до недели. Здесь все зависит от климатических условий местности. Процедура демонтажа опалубки состоит из нескольких этапов:
- Идет снятие крепежа, который соединяет между собой параллельно расположенные щиты.
- Убираются установленные с двух сторон откосные стойки.
- Все элементы конструкции осторожно снимаются.
Демонтаж опалубки должен проводиться с предельной аккуратностью. Снятие щитов начинается с отклонения их от верхней точки. Такую работу следует начинать только в том случае, когда существует полная уверенность в окончательном застывании раствора.
Несъемная опалубка
С помощью несъемной опалубки можно построить дом с одновременным его утеплением. Основными элементами системы являются блоки с замками для фиксации. Изготавливаются они из следующих видов материала:
- Пенополистирола. Такая опалубка характеризуется прочностью и хорошей теплоизоляцией. Небольшой вес конструкции обеспечивает минимальное давление на бетон. Основным преимуществом материала является его способность хорошо пропускать воздух.
- Арболитобетона. Это деревянные щиты, в которых присутствуют пузырьки воздуха, что является характерной особенностью материала. Такие изделия обладают хорошей влагостойкостью, пожаробезопасностью и не подвержены гниению.
- Фибролита. Основу изделий составляет древесная стружка и каустический магнезит. К характерным свойствам материала относится его морозостойкость, огнестойкость и экологическая чистота.
Из всех видов материала чаще всего применяется пенополистирол. Причиной является его легкость, что обеспечивает удобство монтажа. Плиты соединяются между собой с помощью сложных замков и перемычек. Это придает цельность конструкции без использования подпорок. На внутренней стороне опалубки присутствуют пазы, обеспечивающие надежность сцепления материала с застывшим бетоном. Внешняя поверхность гладкая, что позволяет вести качественную финишную отделку.

Скользящая опалубка
Для возведения бетонных стен новаторским вариантом является скользящая опалубка. В ее состав входят следующее элементы:
- Щиты. Они могут иметь разную геометрию в зависимости от конфигурации бетонной стены. Изготавливаются такие составляющие из металла или фанеры.
- Домкратная рама. Она выдерживает основной вес конструкции.
- Домкратные стержни. Это специальные толкатели, которые двигают щиты в нужном направлении с помощью электрического двигателя или ручным способом.
- Направляющие.
Если опалубка изготовлена из металла, то с внутренней стороны смазывается специальным составом. Это устраняет риск прилипания бетона к материалу. По мере выполнения определенного этапа работы опалубка перемещается вертикально вверх. Металлические направляющие, по которым совершается движение щитов, располагаются строго вертикально. Их наращивание осуществляется с помощью болтовых соединений.

Существующие виды
Используемая скользящая опалубка для бетонных стен бывает двух видов:
- Крупнощитовая. В данном случае изделие имеет большой вес, поэтому для монтажных работ используется техника. При этом оборудование необходимо не только для поднятия опалубки на определенную высоту, но и для трамбовки залитого бетона.
- Мелкощитовая. Такие элементы конструкции используются для работы без применения спецтехники ввиду их небольшого веса. Небольшого размера опалубку удобно использовать при возведении любого масштаба зданий.
Конфигурация обоих видов щитов предполагает формирование стен разной геометрии. Они бывают прямыми или вогнутыми. Примером может служить строительство прямоугольных домов или круглых башен.
Монтажные работы
Монтаж скользящей опалубки осуществляется в несколько этапов:
- Если опалубка уже была в употреблении, то она хорошо очищается от бетона, и на ней устраняются все видимые внешние дефекты.
- Затем внутренняя поверхность щитов смазывается специальной эмульсией.
- В фундамент здания вмуровываются направляющие стержни с домкратами.
- Из щитов формируется короб.
- На основании домкратной рамы устанавливаются короб, состоящий из внутренних и внешних щитов с формированным дном.
- Внутри короба вяжется арматура в соответствии с чертежами проекта.
- Для соблюдения толщины стены здания устанавливаются специальные шаблоны. Их количество — как минимум две единицы.
- На кронштейнах подвешиваются с наружной и внутренней стороны короба подмостки. На них будут присутствовать рабочие и проводить корректировку заливки бетона.
- Внутреннее пространство заполняется бетоном и после его затвердевания домкраты поднимают всю конструкцию на заданную высоту.
Таким способом можно вести строительство сооружения до 4 м в сутки.
Преимущества и недостатки
Использование скользящей опалубки имеет следующие преимущества:
- Обеспечивается высокая скорость проведения работы.
- Отсутствует необходимость в привлечении большого количества рабочей силы.
- Наблюдается значительная экономия средств при возведении здания.
Однако в такой работе наблюдаются и некоторые недостатки, которые выражаются в следующем:
- Скользящая опалубка имеет сложную конструкцию.
- Выполнять такую работу могут только работники с высокой квалификацией.
- Должна быть обеспечена бесперебойная доставка бетонной смеси.
Однако все присутствующие недостатки полностью перекрываются существенными преимуществами.
Опалубка для перекрытий
Если в здании планируется установка бетонного перекрытия, то для него требуется формирование специальной опалубки. Такое устройство должно обладать высокой прочностью и надежностью, потому что ему требуется выдерживать большой вес бетона. Для изготовления заранее подготавливаются балки, доски и водостойкая фанера. Монтаж опалубки ведется на высоте, поэтому в качестве опор обычно используются телескопические стойки.
Монтаж перекрытия состоит из шагов:
- Устанавливаются стойки с шагом до 1 м по всей протяженности стен.
- Их высота должно быть одинаковой для обеспечения горизонтальности перекрытия.
- На опоры укладываются продольные брусья.
- Сверху располагаются поперечные брусья с шагом 20-60 см.
- На поперечные брусья прибивается фанера. Листы должны располагаться так, чтобы их стыки приходились на деревянный брус. В качестве крепежа используются саморезы.
- После формирования основания устанавливаются вертикальные ограждения. Для этой цели используются доски, толщина которых должна составлять 30-40 мм. В некоторых случаях ограждением служит присутствующая кирпичная кладка.
- Внутри пространства прокладываются трубы для инженерной коммуникации.
Достоинством такой опалубки является то, что после застывания бетонной смеси ее можно снимать и использовать повторно.
Опалубки для возведения бетонных сооружений с течением времени постоянно модернизируются. Только при создании фундамента для небольшого дома они имеют элементарный вид. Во время масштабного строительства применяются сложные конструкции, позволяющие вести работы в быстром темпе с наименьшими затратами.

«Теплая керамика»: надежно, экономично, долговечно
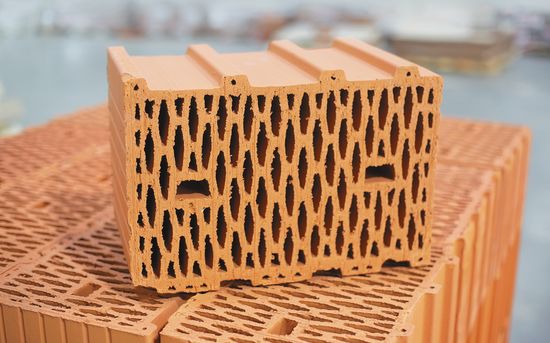
Крупноформатная керамика последние несколько лет уверенно держит позиции на рынке. Это современный и наиболее востребованный материал, который эффективно используется как в многоэтажном, так и в коттеджном строительстве.
Признание он получил и среди покупателей продукции компании «ЛСР. Стеновые» (предприятие, входящее в холдинг крупнейшего застройщика России, «Группу ЛСР»), став одним из самых популярных товаров в ассортименте наравне с лицевым и рядовым кирпичом, а также клинкером – фасадным и тротуарным (о нем подробнее читайте статью «Российский клинкер: эпоха возрождения», «Строительный Еженедельник» от 25 марта 2019 года) и газобетоном («Правильный дом – это каменный дом», «Строительный Еженедельник» от 22 апреля 2019 года).
Планируя создание индивидуального «дома своей мечты», граждане обычно начинают с выбора локации, оценивая перспективность той или иной местности для проживания. А вот уже на следующем этапе проектирования возникает вопрос, будет ли дом предназначен для сезонного или постоянного проживания, а также – из каких материалов его возводить.
К дачному домику требования, конечно, попроще, хотя и в этом случае основательный хозяин подойдет к вопросу со всей серьезностью. А вот если речь идет о коттедже для постоянного проживания, об обустройстве с комфортом всего участка, то в любом случае здание должно соответствовать самым высоким требованиям, таким как прочность, долговечность, экологичность. Очень важным становится вопрос теплоизоляции, поскольку от него напрямую зависит уровень расходов на теплоснабжение. Немаловажны и такие факторы, как пожаробезопасность, стойкость к вредным воздействиям окружающей среды, звукоизоляция и пр. Как раз всем этим требования полностью отвечает крупноформатная керамика.
Керамоблок как он есть
Крупноформатную керамику с порами внутри нередко называют также крупноформатным камнем, керамическими блоками либо поризованной или теплой керамикой. Она производится по нормам ГОСТ 530-2012, в соответствии с которым правильное название – «камень керамический».
Современные поризованные керамоблоки появились в 1980-х годах в Германии. «Предком» этого материала можно назвать пустотелый красный кирпич. По исходному сырью и некоторым эксплуатационным параметрам они схожи. Но по размеру керамический блок обычно превосходит кирпичи как минимум в 2,1 раза, что дает ему множество преимуществ. Крупноформатные продукты превышают его по габаритам более чем в 10 раз. Так, компания «ЛСР. Стеновые» производит рядовой поризованный крупноформатный камень следующих размеров: 14,3 НФ, 12,35 НФ, 11,2 НФ, 10,7 НФ. НФ в данном случае – это число стандартных кирпичей, которые по объему могут быть заменены одним керамоблоком.
Форма у этого стройматериала сложная, с системой «паз – гребень» с двух длинных сторон. Она позволяет минимизировать количество сквозных швов в кладке, что снижает общий коэффициент теплопроводности стены. В сравнении с возведенными из обычного кирпича строениями дома из керамических блоков получаются более теплыми.
Поризованным же керамический камень делают для того, чтобы уменьшить его вес при увеличении размера и обеспечить дополнительные теплоизоляционные характеристики. В качестве поризаторов, добавляемых на этапе формования глиняной массы, могут выступать солома, опилки древесины, шелуха семечек или риса, торф и т. д. Все это сгораемые материалы натурального происхождения. Главная их задача – выгореть дотла при обжиге керамического камня в печи. После них внутри остаются многочисленные микропустоты, которые и придают керамоблокам повышенные теплотехнические характеристики.
Производство керамики – высокотехнологичный процесс, требующий современного оборудования. Компания «ЛСР. Стеновые» выпускает такую продукцию на Никольском кирпичном заводе в Отрадном (Колпинском кирпичном заводе в Колпино), а в случае их большой загруженности – также и на Рябовском кирпичном заводе (Тосненский район). «Никольский завод построен в 2012 году, на нем установлены немецкие производственные линии последнего поколения. На других заводах в рамках программ модернизации также было установлено современное оборудование», – рассказывает ведущий менеджер компании «ЛСР. Стеновые» по работе с проектными организациями Дамир Бахтигараев.
Современные мощности предприятий, а также тщательный контроль на всех этапах производственного цикла гарантируют высокое качество выходящего на рынок керамического камня компании «ЛСР. Стеновые».
Плюсы, плюсы…
Если взглянуть на международный опыт, причем брать не джунгли Юго-Восточной Азии или пустыни далекой Аризоны, а климатически и географически близкую России Германию, то при малоэтажном строительстве самым популярным материалом там остается керамика. Из нее делаются несущие стены, которые покрываются либо облицовочным кирпичом, либо клинкером. Придомовые дорожки также делают из тротуарного клинкера.
Причины этого очевидны: хозяева заинтересованы в прочном, экономичном, экологичном и долговечном здании. Таком, в котором будет комфортно и безопасно жить не только им самим, но и их наследникам. Совершенно очевидно, что и российские домовладельцы заинтересованы в том же. И теперь компания «ЛСР. Стеновые», выпуская современные стройматериалы (и керамику, и клинкер, и газобетон) обеспечила для них такую возможность.
Именно поэтому крупноформатные керамические блоки получают все большее распространение как в коттеджном, так и в многоэтажном строительстве (стеновые заполнения в монолитном каркасе). Это не удивительно, поскольку они обладают поистине уникальным сочетанием прекрасных характеристик.
Высочайшие теплоизоляционные качества
Благодаря особенностям конструкции крупноформатные керамические блоки являются на данный момент единственным стеновым керамическим материалом, позволяющим осуществлять строительство домов с толщиной стен 38–64 см без дополнительного утепления. Показатели теплопроводности (0,08–0,18 Вт/м•°С) у стены толщиной 51 см, выполненной с использованием керамоблоков, сопоставимы с кладкой из обычного кирпича толщиной 120–200 см.
Сравнительная легкость
Благодаря пористости и наличию пустот крупноформатные стеновые блоки имеют меньший объемный вес (600–800 кг/куб. м), чем обычный кирпич (у пустотелого красного кирпича пустоты занимают 25–40% объема, а у блока этот показатель достигает 44–56%). Это обеспечивает удобство работы по укладке керамического камня. Кроме того, низкий вес материала позволяет обеспечить экономию при устройстве фундамента.
Высокая скорость работ
Крупноформатность блока позволяет ускорить темпы строительства в 3–5 раз. Если из обычного кирпича каменщик в среднем выкладывает 1–1,5 куб. м кладки за смену, то из керамоблоков – до 8 куб. м.
Экономичность
Быстрые темпы работы позволяют снизить себестоимость кладки. Система «паз – гребень», не требующая заполнения раствором при кладке, дополнительно позволяет уменьшить как расход кладочного раствора (как минимум в 3 раза), так и площадь «мостиков холода».
Высокая прочность
Уникальная технология производства и совершенство структуры внутренних полостей позволяют изготавливать блоки со сбалансированным сочетанием высокой прочности и низкой теплопроводности. Так, при теплопроводности 0,21 Вт/м•°С прочность на сжатие блока составляет 150 кг/кв. см (М-150), а при 0,16 Вт/м•°С – 100 кг/кв. см (М-100).
Долговечность
Отсутствие необходимости использования эффективных утеплителей позволяет возводить гомогенные стеновые конструкции, которые более всего устойчивы к негативному воздействию окружающей среды: температурным перепадам в сочетании с попеременным увлажнением и высушиванием, воздействию кислотных дождей и выхлопных газов, ветровым нагрузкам. Все это определяет их высокую (более 100 лет) долговечность, а также экономичность, если учитывать не только расходы на строительство, но и эксплутационные и ремонтные расходы.
Звуконепроницаемость
Крупноформатный керамоблок, наряду с высокими теплоизоляционными характеристиками, обладает и высоким уровнем звукоизоляции. Так, к примеру, керамические перегородки толщиной всего 12 см имеют звукоизоляцию минимум 45 дБ, а стены толщиной 38 см – около 53 дБ. Поэтому стены, возведенные из крупноформатных керамических блоков, не требуют дополнительных затрат на шумоизоляцию.
Экологичность
Керамический камень изготавливается исключительно из натуральных экологически чистых компонентов. В своем составе не содержит вредных примесей, красителей и абсолютно безопасен для человека.
Высокая биологическая инертность
Керамоблоки устойчивы к биопоражениям, на керамике вообще крайне неохотно живут и размножаются грибки, плесень и различные микробы.
Пожаробезопасность
Крупноформатные керамоблоки относятся к негорючим строительным материалам (класс НГ). Они не поддерживают горение, под воздействием высоких температур не деформируются, а также не выделяют вредных для человека веществ.
Высокая стойкость
Керамический камень устойчив к атмосферным воздействиям, влиянию ультрафиолетовых лучей, кислот и щелочей, отличается химической инертностью.
…и еще плюсы
Помимо этого, к достоинствам керамического камня можно отнести и широкий ассортимент блоков, позволяющий найти оптимальный вариант для каждого конкретного случая: богатство форм открывает новые возможности для дизайнеров и архитекторов.
Технология производства керамического камня позволяет выпускать блоки точных размеров и с идеальной геометрической формой, облегчающей их сочетание с иными материалами. «Крупноформатные керамические блоки идеально «работают» в сочетании с облицовочным клинкером (получается очень эффектно), с облицовочным кирпичом (это более экономичный вариант), которые также производятся компанией «ЛСР. Стеновые» в широком ассортименте», – подчеркивает Дамир Бахтигараев.
Рифленая поверхность керамоблоков позволяет при необходимости быстро, легко и экономно проводить штукатурные и облицовочные работы. Расход штукатурки уменьшается в среднем в 1,5–1,7 раза по сравнению с работой на стенах из обычного кирпича.
Сочетание этих факторов (относительная легкость материала, простота технологии кладки, уменьшенное количество кладочного раствора, быстрота выполнения штукатурных работ и пр.) дает возможность серьезно экономить на всей совокупности работ. Сроки их выполнения снижаются как минимум в 3 раза по сравнению с использованием обычного кирпича.
Bonus: микроклимат
Все ранее описанные преимущества крупноформатных керамоблоков касаются технических характеристик материала, а также удобства и экономичности при ведении строительных работ. То есть это достоинства, которые имеют большое значение прежде всего с точки зрения строителя: возможность соблюдать действующие нормативные требования к объекту при сравнительно невысокой стоимости его возведения.
Необходимо, однако, отметить и еще одно немаловажное обстоятельство, играющее важнейшую роль для жильцов зданий из керамического камня и объясняющее большую популярность его при индивидуальном жилищном строительстве. Благодаря базовым свойствам керамики и оптимальному расположению в ней пустот крупноформатные блоки обладают уникальным тепло- и влагообменом, позволяют стенам «дышать» и поддерживать внутри помещения оптимальный микроклимат.
«Сама глина из-за специфики ее структуры обладает свойством прекрасно впитывать влагу. Причем переносит ее из жилого помещения наружу, обеспечивая оптимальную влажность внутри здания. А крупноформатная поризованная керамика, благодаря особенностям производства, гарантирует прекрасную термоизоляцию. В совокупности же это создает великолепный микроклимат внутри помещений, обеспечивающий тепло зимой и прохладу летом, причем как без избыточной влажности воздуха, так и без чрезмерной сухости. Фактически формируются условия, оптимально комфортные для самоощущения человека. Ни один другой материал на такое не способен», – подчеркивает Дамир Бахтигараев.
Таким образом, если частный дом строится в регионе с повышенной влажностью и низкими зимними температурами (что особенно характерно для Северо-Запада России), то, по утверждению экспертов, у керамических блоков практически нет конкурентов. Древесина и пористый бетон в таких условиях прослужат значительно меньше. А на кирпичные стены придется монтировать недешевый утеплитель, который будет деградировать из-за постоянного воздействия влаги. Таким образом, пористая керамика в данном случае выигрывает по всем статьям.
Неудивительно поэтому, что крупноформатные керамические блоки наряду с газобетоном, классическим кирпичом и клинкером являются одним из лидеров продаж в Центрах строительных материалов «Группы ЛСР», расположенных по адресам:
пр. Кима, 19
ул. Репищева, 10
пр. Народного Ополчения, 10
+7 (812) 334-87-87
Ежедневно: 09:00–20:00.
Интернет-магазин строительных материалов «Группы ЛСР»: sm.lsr.ru
Doka – в опалубке дока
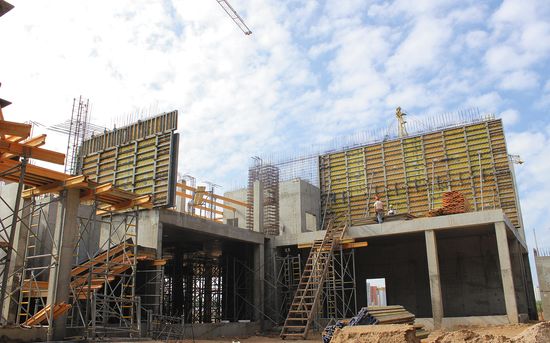
Современное строительство объектов любого назначения невозможно представить себе без монолитных технологий; их – без современных опалубочных систем, ну а их – без продукции, известной всему миру под брендом Doka.
Конкурентоспособность в современном бизнесе немыслима без постоянного движения вперед. И это прекрасно понимают в австрийском концерне Umdasch GmbH, которому принадлежит эта торговая марка и который постоянно предлагает рынку что-то новое – более выгодное, более надежное, более эффективное.
На базе опыта
В прошлом году концерн отпраздновал свое 150-летие, бренд опалубочных систем Doka – 60-летие, а филиал в России «Дока Рус» – 20-летие. И говорит это прежде всего о том, что за каждой новой разработкой компании стоят десятки лет опыта: исследований, открытий, новых технологий, модернизации и совершенствования продукции. Результатом их становится появление уникального оборудования, учитывающего пожелания и практические нужды строителей.
Желание соответствовать требованиям рынка, стремление улучшать существующие и создавать новые технологичные продукты привели к созданию в 1990 году на базе головного предприятия Doka в Амштеттене научно-исследовательского центра, который насчитывает более 100 сотрудников. Инновационные опалубочные решения и передовые инженерные разработки вывели австрийский концерн в 2004 году на новую высоту – самое высокое здание в мире, «Башня Халифа» в Дубае, было построено с опалубкой Doka.
Следствием такого подхода к бизнесу стали создание 160 филиалов по всему миру и массовый экспорт продукции. Ежегодные объемы производства головного предприятия Doka в Австрии составляют 4 млн кв. м фанеры, 1 млн стоек перекрытия, 10 млн пог. м балок, 180 тыс. панелей рамной опалубки, 250 тыс. рам опорных лесов.
Стеновые системы Doka представлены рамной и балочной опалубкой, круговой и фасадной, опалубкой для колонн и контрфорсами. Компания производит опалубку для перекрытий, подъемно-переставные системы, в том числе самодвижущиеся, опорные леса, а также защитные экраны, подмости и прочие системы безопасности.
К окрашенной или оцинкованной стальной раме прикреплена фанера, которая формирует поверхность бетона. Элементы опалубки, разные по высоте и ширине, легко соединяются между собой при помощи специальных замков, создавая простейшие геометрические формы по длине и высоте. Любая система рамной опалубки имеет элементы пассивной безопасности: консоли для приемки бетона, лестницы доступа, перила.
Для создания сложных по геометрии или архитектурным формам поверхностей стен используется балочно-ригельная стеновая опалубка, которая требует предварительной сборки. Применение этой системы имеет свои преимущества и недостатки, о чем долго могут спорить специалисты. Важно помнить, что специалист способен предложить клиенту ту систему, которая наиболее соответствует правильно сформулированному запросу.
Современные автоматизированные устройства производства и хранения до недавнего времени удовлетворяли потребности в опалубке на пяти обитаемых континентах, в 75 странах мира. Ответом Doka на новые вызовы современности стал проект по запуску нового производства – в России, а также вывод на рынок новой опалубки ReForma Standard plus.
Новый завод
Стремление соответствовать требованиям рынка привело к тому, что впервые за 150-летнюю историю руководство концерна Doka приняло решение об открытии производственного предприятия полного цикла за пределами Австрии. Выбор был не случайным: именно российский рынок сегодня динамично развивается и является одним из самых требовательных к качеству, долговечности и технологичности опалубки.
Новое предприятие откроется летом этого года в особой экономической зоне (ОЭЗ) «Липецк». Завод, который разместится на территории в 6 га, будет оснащен оборудованием, аналогичным оборудованию на производстве Doka в Австрии. На предприятии будут созданы мощности для серийного производства до 70 тыс. кв. м стальной рамной опалубки в год.
Первая серийная партия ReForma Standard plus сойдет с полностью автоматизированного конвейера в середине лета, а официальные продажи стартуют в сентябре 2019 года.
«Общий объем инвестиций в завод опалубки Doka в Липецке уже составил около 9 млн евро, – говорит генеральный директор ООО «Дока Липецк» Андрей Гусев. – На настоящий момент штат сотрудников составляет 28 человек, в будущем планируется расширение до 90 человек. Наша команда проходит обучение в Австрии, у нас организованы тренинги специалистами Doka на местах. Таким образом, за новой опалубкой ReForma Standard plus, которая будет производиться на нашем заводе, стоит многолетний инженерный опыт мирового лидера рынка».
Новая система
После многолетнего всестороннего анализа предложения на рынке, изучения недостатков опалубочных систем других производителей из России и ближнего зарубежья специалисты Doka разработали, практически «с нуля», новую систему рамной опалубки ReForma Standart специально для российского рынка. Более того, они постарались учесть многочисленные пожелания клиентов и использовать при производстве самые лучшие образцы отечественных материалов и импортных комплектующих.
Производство будет организовано полностью по австрийским технологиям и стандартам качества. «ReForma Standard plus – это новый продукт, созданный по оригинальным австрийским технологиям и доработанный с учетом эксплуатации в российских условиях, – рассказывает генеральный директор ООО «Дока Рус» Борис Ухов. – Опалубка имеет ряд преимуществ в методах фиксации, показателях оборачиваемости, особенностях стеновых и угловых элементов. Это позволит нам более активно конкурировать с российскими и международными производителями на локальном рынке и в будущем также расширить экспортные продажи».
Новая стальная рамная опалубка ReForma Standard plus предназначена для возведения железобетонных вертикальных монолитных конструкций – стен, колонн и шахт. В первую очередь, новая опалубка российского производства от Doka ориентирована на сектор жилищного и коммерческого строительства, где важны быстрота и простота сборки, надежность, долговечность и высокая экономическая эффективность.
Мировая «премьера» опалубки ReForma Standard plus состоялась на выставке bauma 2019 в Мюнхене, где Doka представила 32 новинки: новую рамную и балочную опалубку, компоненты, системы безопасности, уникальные цифровые решения для строительных площадок и др.
ReForma Standard plus – это:
Экономическая эффективность:
- Высокая несущая способность до 90 кН/м2 в соответствии с ГОСТ 34329-2017
- Распалубочный угол Doka ReForma SP позволяет легко и безопасно переставлять опалубку шахт
- Быстрое проектирование благодаря программному обеспечению Tipos
- Порошковая окраска защищает от коррозии и обеспечивает легкую очистку рамы
- Совместимость с другими опалубочными системами на российском рынке
Быстрая и простая сборка:
- Быстрый демонтаж благодаря углублению для распалубливания
- Универсальность соединения компонентов – подпорный раскос надежно крепится благодаря универсальной головке, а торцевые отверстия в раме позволяют формировать внешние углы, торцы и колонны
- Сварные эллиптические втулки Doka обеспечивают быструю сборку и необходимый уровень гибкости
- Использование клинового замка позволяет значительно ускорить работу на строительной площадке
Надежность и долговечность:
- Прочная стальная рама обладает повышенной устойчивостью к деформации
- Австрийские стандарты качества в России обеспечены технологиями и знаниями специалистов Doka
Российская презентация опалубки ReForma Standard plus пройдет с 4 по 7 июня на выставке Bauma CTT в Москве, в «Крокус-Экспо» (павильон 14, стенд № 14-640). Для получения бесплатного билета используйте промокод Z130GT5. Зарегистрируйте его на сайте www.bauma-ctt.ru/register.