Особенности проекта определяют выбор шпунтовых изделий
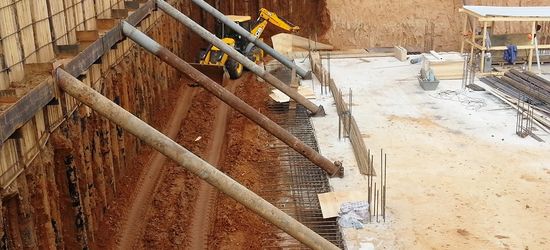
На строительном рынке представлен широкий ассортимент шпунтов – специальных сборных металлических конструкций, которые применяются при создании фундаментов зданий и сооружений, в области гидротехники, мостостроения, дорожного и подземного строительства.
Развитие шпунтовых технологий за последние годы складывается под влиянием растущей доли отечественной продукции на внутреннем рынке, а также замещения импортных поставок. Так, с целью производства качественных шпунтовых изделий в ООО «ТрубМет» разработан и выпускается с 2017 года сварной шпунт корытного типа СШК, который создавался как аналог горячекатаных шпунтов, в том числе шпунтов Ларсена Л4, Л5, Л5-УМ, VL-606-A и других, но по ряду характеристик значительно превзошел их.
Номеклатура шпунтов во многом определяется не столько предпочтениями строителей, сколько возможностями российских поставщиков. Ведущим из них является ЕВРАЗ Нижнетагильский металлургический комбинат (ЕВРАЗ НТМК), где производятся горячекатаные шпунтовые сваи с замком типа Ларсена марки Л5-УМ.
«Шпунты, представленные на российском рынке, можно разделить на несколько основных видов: шпунты Ларсена, трубошпунты сварные, панели шпунтовые сварные (ПШС), сварные шпунты корытные (СШК) и другие», – говорит Данил Маслей, руководитель коммерческого отдела компании «Вектор шпунт», которая специализируется на комплексных свайных работах, включая проектирование, поставку всех видов шпунтов, установку и выемку шпунтовых конструкций.
Шпунтовые изделия отличаются друг от друга техническими характеристиками, включая металлоемкость и форму изделия. Выбор шпунтовых свай при проектировании зависит от объекта, поставленных задач и условий, в которых будет проходить установка и эксплуатация шпунтовой стенки. Для подбора шпунта важно учитывать характер и модуль внешней нагрузки, а также срок эксплуатации.
«Тип шпунта определяется на стадии разработки проекта: инженеры-конструкторы вычисляют требуемую устойчивость шпунтовой стенки, глубину погружения, необходимость установки распорных конструкций и так далее, – поясняет генеральный директор ООО «УМ Геоизол» (входит в группу компаний «ГЕОИЗОЛ») Станислав Тарасенко. – Наибольшее распространение получил металлический шпунт, как прочный и долговечный: это шпунт типа Ларсена, шпунт корытного профиля и Z-образный, а также различные виды трубошпунта».
По данным «Вектор шпунт», наиболее популярными у заказчиков являются шпунты типа Ларсена и трубошпунты. Последние наряду со шпунтовыми панелями в ряде случаев могут быть незаменимы, так как обладают наиболее высоким (а по отдельным спецификациям – многократным) сопротивлением к нагрузкам, по сравнению со шпунтами Ларсена. С другой стороны, применение шпунтов типа Ларсена может достичь необходимого экономического эффекта за счет неоднократной оборачиваемости – при правильном соблюдении технологического процесса извлечения шпунт Л5-УМ можно использовать до 5-7 раз, что повышает до 20-30% выгоду арендной ставки.
Если трубошпунт имеет большой диаметр и будет глубоко залегать, довольно сложно найти подрядчиков с подходящим оборудованием, полагает Данил Маслей. Зачастую на объектах можно встретить применение комбинированных шпунтовых ограждений, когда при проектировании подземной части нужно решить одновременно несколько разных задач или оптимизировать использование шпунтов.
Например, шпунтовые сваи с замковым элементом типа Ларсена особенно эффективны в слабых обводненных грунтах, поэтому они успешно применяются повсюду, где необходимо избежать притока воды в зону строительства.
ГК «ГЕОИЗОЛ» имеет большой опыт выполнения всего комплекса строительно-монтажных работ по устройству свайных фундаментов, «стены в грунте», буровым работам, инженерной защите территорий, подземному и дорожному строительству, усилению грунтов основания с применением собственного парка строительной техники и специализированного оборудования. Шпунты Ларсена компания использовала на самых разных объектах.
«Жёсткость этих шпунтов обеспечивается благодаря ряду параметров, – делится своим опытом работы Станислав Тарасенко. – Во-первых, за счёт толщины стенки шпунта, которая у Л5-УМ достигает 20 мм, что гарантирует высокую коррозийную устойчивость. Для сравнения, у шпунта AZ толщина стенки составляет 6-13 мм.
Во-вторых, расстояние между замковыми соединениями у них равно 500 мм в то время, как у того же шпунта AZ – от 700 до 1400 мм, то есть AZ более гибкий, а потому более подвержен деформации. Строители между собой называют его «лопух».
В силу высокой прочности шпунт наиболее устойчив к деформации при сооружении ограждающих конструкций различных котлованов и надежно защищает от грунтовых вод, потому широко применяется при строительстве подземных сооружений, причалов, набережных, мостов, а также для усиления траншей, береговых линий, склонов и насыпей».
Группа компаний «ГЕОИЗОЛ» применяла шпунт Л5-УМ при реконструкции судоспусковых устройств Средне-Невского судостроительного завода, при строительстве променада в городе Светлогорске Калининградской области, при проведении работ на Тележной ул. 17/19, реконструкции Синопской набережной.
Благодаря быстрому и простому монтажу шпунт Л5-УМ практически незаменим при устройстве прочных и надёжных временных сооружений. Например, при строительстве подземного двухъярусного паркинга в рамках второй очереди (первый этап) бизнес-центра «Невская Ратуша» специалисты «УМ Геоизол» погрузили более 900 тонн такого шпунта в качестве временной жёсткой перегородки между первой и второй очередями строительства. Ещё один пример временного массивного сооружения – трибуна на Южной оградительной стенке Средней гавани Кронштадтского порта к параду в День ВМФ в 2018 году.
Качественный подход
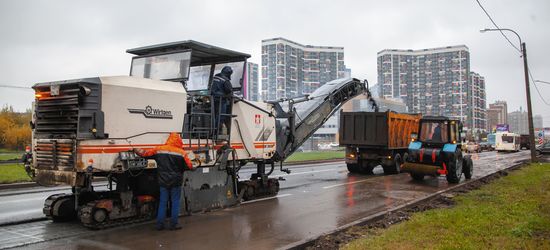
Инновационные технологии позволяют ускорить дорожное строительство и повысить сроки службы асфальтобетонного покрытия. Однако их масштабному внедрению мешают устаревшие нормативы.
Премьер-министр РФ Дмитрий Медведев порекомендовал регионам активнее внедрять в дорожное строительство новые технологии. С этим предложением он выступил на прошлой неделе в Екатеринбурге на совещании по вопросам реализации национального проекта «Безопасные и качественные автомобильные дороги». По его словам, в этом году на эту программу из федерального бюджета было выделено 110 млрд рублей. Однако ряд регионов страны (Приморье, Чукотка, Крым) освоили менее трети предоставленных средств.
Глава российского правительства также предложил наращивать в дорожной отрасли долю контрактов на принципах полного жизненного цикла. «Это мировая практика, она позволяет существенно улучшить качество работ и обеспечить последующий мониторинг. Она, конечно, дисциплинирует подрядчиков, которые не заинтересованы в том, чтобы свой брак постоянно переделывать. К концу 2019 года на принципах жизненного цикла в России должен заключаться каждый 10-й контракт на дорожные работы, то есть 10%. Пока удалось достичь показателя приблизительно 7%, поэтому нужно с подготовкой этих документов в целом ряде регионов поторопиться», – подчеркнул Дмитрий Медведев.
Экспериментальный образец
Стоит отметить, что Петербург и Москва в нацпроекте «Безопасные и качественные автомобильные дороги» не участвуют. В соседней Ленобласти на данный момент по годовому плану данная программа реализована приблизительно на 70%. Параллельно идет подготовка проектов, которые должны стартовать в 2020-м. В целом же в Петербурге и Ленобласти власти стараются активно заниматься ремонтом и строительством дорог и вне федеральных программ. Особое внимание чиновники сейчас уделяют качеству проводимых работ. Многие крупные подрядные организации обоих регионов на своих объектах стараются задействовать инновационные технологии, в том числе и собственные. Правда, чаще всего пока в качестве эксперимента или теста.
В частности, компания «ВАД» совместно с «Газпромнефть – Битумные материалы» летом этого года на тестовом участке в Ленобласти задействовала в работе технологию нанесения защитно-восстанавливающего состава «Брит» (ЗВС-Р) на дорожное покрытие. Этот продукт изготавливается на основе раствора битумно-полимерного вяжущего вещества в органических растворителях и восстанавливает поверхностную структуру асфальтобетона, эффективно защищая его покрытие. Предполагается, что использование ЗВС-Р на автомобильных дорогах поможет продлить срок службы асфальтобетонного покрытия на два-три года и снизит затраты на обеспечение межремонтного периода.
Также этим летом компания «ДСК АБЗ-Дорстрой» уложила километровый экспериментальный участок асфальта на трассе Огоньки – Стрельцово – Толоконниково в Ленобласти, по методу объемного проектирования. В данной технологии был использован ЩМА-19 (щебеночно-мастичный асфальт), а не ЩМА-20, требуемый по ГОСТу. Новая смесь призвана помочь снизить колееобразование, возникающее из-за высокой интенсивности движения на дорогах. Отмечается, что срок эксплуатации дорожных одежд с использованием данного материала в полтора-два раза выше, чем у традиционных смесей.
Необходима актуализация
По мнению первого заместителя директора компании «Стройтех» Сергея Ивашова, качественное строительство дорог невозможно без актуализации действующих государственных стандартов. В настоящее время они меняются, но недостаточно быстро, не успевая за появлением все новых технологий, начиная от проектирования, заканчивая повседневной эксплуатацией дорог. Также необходимо своевременно обновлять различные подзаконные акты.
«Другая боль дорожников – это конкурсы. Сейчас заказчику требуется выбрать подрядчика с наибольшим снижением начальной максимальной цены. При этом демпингующая организация – не обязательно «Рога и копыта». Минимизирование цены приводит к тому, что работы выполняются некачественно, а иногда и вовсе не могут быть завершены. Соответственно, проект остается нереализованным, а проведение дополнительного конкурса требует дополнительных средств и времени. Необходимо отходить от проведения аукционов к прямым договорам, но для этого необходимо существенно менять все законодательство», – полагает Сергей Ивашов.
Мнение
Максим Хрипунов, директор Департамента «3D-системы автоматического управления TOPCON» ООО «Геостройизыскания»:
– В настоящее время при проектировании и строительстве активно применяются различные сканирующие системы, предназначенные для оперативного сбора данных, на основе которых создаются проекты. Получение реальных данных о поверхности дороги входит в часть задач системного рабочего процесса, включающего работу системы 3D на асфальтоукладчиках и дорожных фрезах. Преимущества такой технологии: быстрый сбор большого количества данных; четко спрогнозированное использование времени, оборудования и материалов; проектирование с учетом всех требований и критериев; выполнение работ по фрезерованию и укладке; работа с переменным слоем; интеллектуальное уплотнение.
Сергей Луценко, генеральный директор компании «Дорианс»:
– Сейчас все говорят о необходимости применения BIM-технологий при проектировании дорог. Эту позицию мы поддерживаем и в своих проектах задействуем информационное моделирование. Но в целом, чтобы эти технологии действительно показали свою эффективность, важно их задействовать всем, а не только проектировщикам. Сейчас, к сожалению, они почти не используются при согласовании с заказчиками, представителями ресурсоснабжающих организаций и др. В частности, специалист может с помощью BIM быстро подготовить проект, но далее экспертиза все равно от него попросит чертежи в PDF-файле. С одной стороны, мы внедряем прогрессивную программу, с другой – барьеры для ее эффективного использования сохраняются.
Михаил Смирнов, продакт-менеджер направления «Ремонт бетона» подразделения строительной химии Master Builders Solutions концерна BASF:
– Пока, на наш взгляд, распространение инновационных технологий в дорожной отрасли идет достаточно медленно. Несмотря на их очевидные плюсы, производителям все еще приходится убеждать дорожников, что подобные подходы оправдывают свою стоимость. В целом же решений, способных обеспечить быстрый и качественный ремонт мостов и дорог, на рынке достаточно много. Но хотелось бы отметить, что ставка должна делаться на комплексное использование существующих решений. В частности, составы для ремонта бетона, его вторичной защиты и гидроизоляции необходимо подбирать с учетом индивидуальных особенностей объекта.
Купол как уникальная конструкция

Лаборатория деревянных конструкций ЦНИИСК им. В. А. Кучеренко АО «НИЦ «Строительство» совместно с ООО «ЦНИПС ЛДК» разрабатывает проекты большепролетных каркасов покрытия из клееных деревянных конструкций (КДК). По их проектам построено более 10 аквапарков по всей России. Крупнейший из них – аквапарк «Питерлэнд» в парке 300-летия Санкт-Петербурга. Об особенностях проекта «Строительному Еженедельнику» рассказал заведующий лабораторией деревянных конструкций ЦНИИСК им. В. А. Кучеренко Александр Погорельцев:
– В бассейнах и аквапарках КДК имеют преимущества перед конструкциями из металла или железобетона. Для них хлорирование или озонирование воды создает агрессивную среду, нейтральную для древесины.
В ТРК «Питерлэнд» смонтирован ребристый купол диаметром 90 м и высотой 45 м. Особенности конструкций связаны в основном с его габаритами. В плане меридиональные ребра купола опираются с шагом 14,5 м на нижнее железобетонное кольцо и на стальное верхнее кольцо диаметром 5 м. Основные ребра длиной около 60 м выполнены в виде серповидных сборных ферм и сами по себе являются уникальными в части принятых конструктивных решений, изготовления, сборки и монтажа. На эти ребра с шагом 6 м опираются девять криволинейных кольцевых элементов, из которых два – верхний и нижний – являются опорами для 60 промежуточных меридиональных ребер. Нижний кольцевой элемент выполнен в виде горизонтальной фермы, воспринимающей реакции опор от промежуточных ребер и нагрузки от кольцевой технологической площадки. Остальные кольца являются распорками между меридиональными ребрами для обеспечения их устойчивости.
В конструкции купола реализованы основные принципы «системы ЦНИИСК», все основные узлы и стыки поясов серповидных ребер выполнены на наклонно вклеенных стержнях и V-образных анкерах. Это уникальная система узловых соединений, основанная на вклеивании в древесину арматурных стержней периодического профиля. Россия обладает приоритетом в области подобных узловых соединений деревянных конструкций.
Все жесткие стыки ребер и соединения закладных деталей со стержнями, вклеенными на заводе и на монтаже, выполнены ручной сваркой. Экспериментальные исследования, проведенные в ЦНИИСК с целью оценки влияния сварки на соединения, показали, что существующий «психологический» барьер при сварке деревянных конструкций успешно преодолевается. При соблюдении нескольких рекомендаций сварка практически не сказывается на несущей способности соединений.
Меридиональные ребра состоят из четырех отправочных блоков полной заводской готовности, соединяемых на монтаже жесткими стыками на сварке. Все блоки по торцам снабжены выпусками V-образных анкеров и закладными деталями.
Проблемы допусков по длине для меридиональных ребер решены с помощью зазоров около 40 мм между торцами поясов, заполняемых полимербетоном после сварки V-образных анкеров и стальных полос. Этим достигается плотный контакт по площадкам сжатия.
Треугольная решетка меридиональных ребер включает горизонтальные и вертикальные элементы. Горизонтальные соединены с поясами на цилиндрических нагелях и шпильках, а вертикальные – с усилием растяжения до 40 т – путем сварки выпусков вклеенных стержней и закладных деталей на раскосах.
Сборка и монтаж меридиональных ребер производились в три этапа: сначала на жестком горизонтальном стенде производилась предварительная сборка блоков в проектных габаритах, затем окончательная сборка в вертикальном стальном стенде с последующей установкой блоков в проектное положение.
Из-за кризиса 2008 года после монтажа каркаса купола строительство было приостановлено – и возобновлено только в 2011 году. В результате влажность древесины, не защищенной от атмосферных осадков, значительно превысила величину равновесной влажности, соответствующей условиям эксплуатации. Быстрое завершение строительства и ввод в эксплуатацию могли привести к неравномерной усушке древесины и, как следствие, к появлению значительных трещин и расслоений. Разработанные в ЦНИИСК рекомендации по обеспечению температурно-влажностного режима при завершении строительства позволили избежать этих проблем.