Вторая жизнь. Холодный ресайклинг в дорожном строительстве
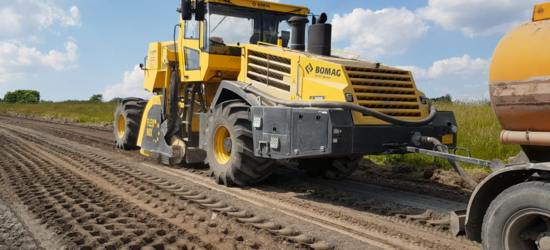
Повторное использование в дорожном ремонте изношенного асфальтового покрытия, перемешанного непосредственно на дороге с верхним слоем дорожного основания, с добавлением вяжущих и специальных добавок позволяет повысить скорость и экономичность проведения работ, при этом получая монолитную плиту основания с очень высокими и долговечными эксплуатационными характеристиками. Данная технология, называемая холодным ресайклингом (холодной регенерацией), активно используется в зарубежных странах, но в России пока только начинает распространяться.
По словам заместителя генерального директора по связям компании «Статус-Грунт» Максима Лебедева, в условиях изношенности дорожного фонда и бюджета, недостаточного для проведения капитального ремонта, местные власти вынуждены ограничиваться текущим ремонтом, который заключается в замене только защитного слоя (асфальтобетона). Большая часть региональных и межмунициапальных дорог в нашей стране устроены много десятилетий назад и рассчитаны были еще тогда на значительно меньшие нагрузки (6–8 т/ось). Их основания практически полностью разрушены, они не несут прочностных характеристик (материалы деградированы, переувлажненные участки, карсты, коррозия дорожного основания и т. д.). Большинство сегодняшних ремонтных работ можно сравнить с укладкой асфальта на «манную кашу»: деньги потрачены, а эффекта нет. Все дефекты дороги в короткие сроки вновь выходят на поверхность.
«В отличие от традиционного фрезерования и замены только верхнего слоя покрытия, технология холодного ресайклинга позволяет получить усиленную конструкцию дорожной одежды, создавая из материалов старого покрытия и дорожного основания новый гомогенный слой с более высокими прочностными характеристиками. Данный метод позволяет использовать 100% материалов старой дороги, сокращая сроки строительства в три раза и получая экономию бюджета до 20–30%, при этом оставаясь мерой текущего, а не капитального ремонта», — подчеркивает Максим Лебедев.
Выбирая технику
В работе по технологии холодного рециклинга используется специализированная техника — ресайклеры, в большинстве своем они импортного производства.
Директор по развитию бизнеса ООО «МС-партс» Александр Басионок отмечает, что конкуренция среди производителей ресайклеров существует, но она в разы ниже по сравнению с другой строительной техникой. «Далеко не каждый завод-изготовитель имеет возможность производить и держать по наличию в России технику для регенерации. Известная китайская компания XCMG это делает, имея постоянный склад ресайклеров на Дальнем Востоке и в Москве. Кроме того, XCMG отличается своей доступностью по стоимости и широким ассортиментом. Что касается новинок, то завод ежегодно дорабатывает существующие модели, опираясь на отзывы своих дилеров и заказчиков, а также регулярно выпускает новые модели.
Ресайклеры — это большие сложные и дорогие машины, продолжает тему региональный менеджер по продажам компании «ФАЙАТ БОМАГ РУС» Дмитрий Абрамов, поэтому рынок машин для регенерации и стабилизации невелик и составляет порядка трех десятков машин в год. «Основными игроками на этом рынке являются три производителя специализированной техники, в число которых входит компания BOMAG, выпускающая подобные машины с 1973 года. При выборе машины для стабилизации и рециклинга важно понимать, с какими вяжущими и в каких комбинациях придется работать на будущих проектах. Машины по запросу клиента комплектуются различными системами введения и дозирования воды и вяжущих материалов в асфальтогранулят», — добавил он.
Требуются стандарты
Несмотря на технологичность и эффектность метода холодного ресайклинга для ремонта и строительства дорог, по мнению экспертов, она пока в нашей стране активно не применяется. К сдерживающим факторам, отмечает Максим Лебедев, можно отнести неосведомленность о ее положительных аспектах и нежелании разбираться в них, а порой и просто лоббирование интересов местных АБЗ и карьеров лицами, принимающими решение на местах, отсутствие их прямой и реальной ответственности за полученный результат и экономическую эффективность решений.
«В связи с вышеизложенным огромные деньги расходуются нецелесообразно или с низкой эффективностью. Необходим более жесткий контроль за этим, особенно при реализации национального проекта "Безопасные и качественные дороги" (БКД). Правда, отдельные регионы используют эту технологию при ремонте дорог. В 2020 году мы отремонтировали по технологии холодной регенерации более 300 тыс. кв. м межмуниципальных дорог в Нижегородской области, сэкономив немалые деньги региону. Данная технология, на мой взгляд, — огромное подспорье в оптимальной реализации программ развития дорожной сети в РФ и, в частности, БКД», — сообщил Максим Лебедев.
В компании «Цитадель технология», занимающейся производством продуктов для стабилизации грунтов, также считают основным сдерживающим фактором серьезного внедрения в дорожную отрасль холодного ресайклинга отсутствие должной нормативно-правовой базы. В данном случае имеется в виду отсутствие национального стандарта по данной технологи. Хотя подвижки, отмечают специалисты, уже есть, в прошлом году приняли предварительный национальный стандарт по укреплению грунтов. Проектировщики неохотно идут на эту технологию. Им проще работать по старинке. Технология требует высококачественного инжинирингового сопровождения. Это и будет в дальнейшем точкой роста. Как только появятся инжиниринговые компании, обладающие компетенцией в проектировании и строительстве по указанной технологии, то и государственным заказчикам будет проще ее применять. Сегодня складывается парадоксальная ситуация: государственные заказчики проводят конкурсы на холодную регенерацию, подрядчики выполняют работу, а технические заказчики порой не знают, по каким нормативам принимать работы, подчеркивают эксперты.
Мнение: Александр Басионок, директор по развитию бизнеса ООО «МС-партс»:
— В линейке ресайклеров XCMG достаточно моделей, чтобы подобрать именно тот, который будет отвечать конкретным требованиям заказчика. К примеру, если дорожная организация работает исключительно в рамках стабилизации грунтов, то приобретение полноценного ресайклера нецелесообразно ,и ему будет вполне достаточно использовать более легкую модель в виде стабилизатора XCMG XL2103 или XL2503. Если же в планах работы с асфальтом или клиент рассматривает приобретение на перспективу с целью участия на объектах с разными требованиями, то, безусловно, стоит рассмотреть полноценный ресайклер типа XLZ2103 или XLZ2303. Весь модельный ряд XCMG представляет собой восемь машин, две из которых — стабилизаторы, шесть — ресайклеры.
Матвей Пироженко: «Продукция Peikko востребована «от Москвы до самых до окраин»
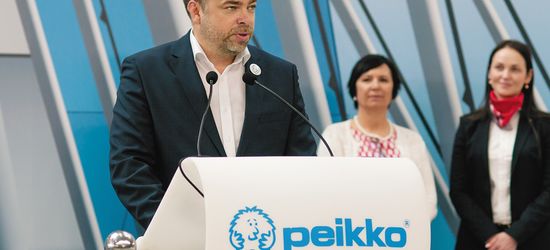
Финская семейная компания Peikko, основанная в 1965 году в Лахти, работает в России уже 12 лет. И, несмотря на непростую рыночную ситуацию, ей удается не только сохранить свои позиции, но и активно развиваться. О новом заводе компании в Санкт-Петербурге и его продукции «Строительному Еженедельнику» рассказал генеральный директор ООО «Пейкко» Матвей Пироженко.
– Матвей Евгеньевич, расскажите, пожалуйста, о новом российском производстве компании.
– Peikko – известный в Финляндии и Скандинавии, а теперь и в России, производитель металлоконструкций для железобетонного строительства (это панели, колонны, элементы фундаментов, дорожные ограждающие конструкции и пр.).
В прошлом году был запущен новый современный завод в Северной столице России. Нами было приобретено промышленное здание площадью более 7,5 тыс. кв. м, а также закуплено высокопроизводительное европейское оборудование. Общий объем инвестиций в проект превысил 420 млн рублей.
На нашем российском предприятии выпускается полный спектр продукции, который холдинг Peikko имеет в своем продуктовом портфолио. Используемое оборудование, стандарты качества как производства, так и самих изготавливаемых изделий полностью отвечают европейским стандартам и требованиям. Это совершенно необходимо, поскольку значительная часть продукции нами экспортируется.
Трудовой коллектив компании в прошлом году увеличился с 40 человек до 100, а в будущем году должен дорасти до 150.
– Вы планируете расширять производство, ставить новые линии?
– В настоящее время установленное оборудование работает в две смены, то есть загружено примерно на 70%. Мы рассчитываем в 2020 году перейти на трехсменную работу, с полным задействованием имеющейся техники.
Впрочем, поскольку объемы поставок у нас неуклонно растут, не исключено, что через несколько лет существующих мощностей нам будет не хватать. И тогда, видимо, встанет вопрос и о запуске нового производства. Скорее всего, в целях оптимизации логистических схем оно будет расположено в Московской области.
– Продукция компании настолько востребована?
– Несмотря на непростые общеэкономические условия и определенную стагнацию, наблюдающуюся на рынке железобетонных изделий, «Пейкко» удается ежегодно увеличивать объемы поставок продукции, в том числе и в последнее время, когда, в общем, мало кто может похвастать заметным ростом.
У нас более 250 российских клиентов, географически расположенных, как поется в известной песне, «от Москвы до самых до окраин»: от Калининграда до Владивостока. Кроме того, сегодня наша продукция экспортируется в пять стран: Финляндию, Швецию, Норвегию, Белоруссию и Казахстан.
Полная локализация производства в России – а мы работаем с качественным сырьем отечественного производства (сталь европейских марок) – в сочетании с жесткими международными требованиями к качеству позволяют нам предложить покупателям в других странах весьма привлекательные условия как по характеристикам выпускаемых изделий, так и по цене. А близость производственной базы к Финляндии и Скандинавии обеспечивает сравнительно невысокие затраты на логистику.
– Какая продукция российского завода идет на экспорт?
– Мы поставляем за рубеж практически всю производимую предприятием номенклатуру. Из наиболее востребованных в Финляндии и Скандинавии продуктов могу выделить комплекты для устройства фундаментов ветрогенераторов электроэнергии. Тема «зеленой энергии» сейчас очень актуальна в Европе, и наша продукция в этой области пользуется повышенным спросом. Это связано с тем, что Peikko предлагает полный комплекс проектирования, производства и затем шеф-монтажа элементов фундаментов «ветряков».
Отмечу, что в последнее время это направление начинает развиваться и в России. Существует уже несколько ветропарков, и заявлено еще около десятка проектов в этой сфере. Соответственно, мы можем быть уверены в перспективности работы в этом сегменте, и в ООО «Пейкко» есть специальное подразделение, работающее в этой сфере.
Алексей Емельянов: «Небольшие затраты могут дать серьезную экономию»

Российская компания «Полипласт» вышла на рынок в 1999 году. Сегодня холдинг объединяет три больших завода (на Урале, в Подмосковье и в Ленобласти), а также ряд локальных производственных площадок, а выпускаемые им химические добавки для различных отраслей промышленности хорошо известны не только в РФ и СНГ, но и во многих странах дальнего зарубежья. О том, почему экономить на добавках в бетон экономически невыгодно, «Строительному Еженедельнику» рассказал генеральный директор ООО «Полипласт Северо-Запад» Алексей Емельянов.
– Алексей Валерьевич, не только от частников, возводящих малоэтажные дома для себя, но даже от строителей порой можно услышать такое мнение, что «бетон – он и есть бетон, какие добавки в него не сыпь». Каково Ваше мнение об этом?
– С моей точки зрения, это подход совершенно ошибочный. И если при стройке «для собственных нужд» он еще допустим (редко когда малоэтажный дом требует каких-то специфических строительных характеристик), то при промышленном строительстве такое отношение ведет не только к снижению качества здания, но и, по сути, к финансовым потерям девелопера.
Дело в том, что добавки позволяют получить бетон с заданными свойствами, оптимально соответствующими назначению объекта, а также конкретным условиям работы. Это пластификаторы и гиперпластификаторы, позволяющие снизить количество воды в смеси, что повышает прочность бетона, делает его тягучим, значительно облегчая работу. Это добавки, которые предотвращают преждевременное застывание бетона при низких температурах, что позволяет работать в зимних условиях. Это различные специализированные добавки, предназначенные для решения конкретных задач, таких, например, как особая прочность, предотвращение появления трещин, пониженная истираемость, повышенная водонепроницаемость и пр. Их целесообразно применять на объектах специального назначения, требующих особых качеств строительных материалов. Это такие области применения, как высотное строительство, гидротехнические сооружения, медицинские учреждения и др.
– И у всех строительных компаний есть специалисты, знающие, какие именно добавки в каких случаях целесообразнее использовать?
– У крупных профессиональных игроков рынка обычно уже есть понимание необходимости использования добавок для эффективной работы, некоторые пока еще слабо знают об имеющихся возможностях. Поэтому «Полипласт» выполняет, в частности, и консалтинговую функцию в этой сфере. Наша задача сегодня – довести до девелоперов и крупных подрядчиков информацию о новых возможностях добавок, бетонов и инновационных технологий в строительстве.
Наши специалисты готовы помочь строителям определить, какие именно добавки наиболее эффективно использовать для решения стоящих перед ними задач в каждом отдельном случае. Все объекты разные, поэтому рецептуру лучше подбирать исходя из конкретной ситуации. Свое влияние оказывают и условия строительства, и специфика сооружения, и даже регион, в котором идет стройка. Ведь, например, на Северо-Западе инертные материалы, входящие в бетон, имеют одни свойства, а в Центральный России – уже несколько иные. Поэтому наши научно-исследовательские центры, действующие при каждом большом заводе, работают не только над созданием новых добавок, но и над оптимизацией их использования.
– Вы упомянули также экономический фактор.
– И этот фактор для строителей наиболее важен. По сути, небольшие затраты на добавки могут не только обеспечить высокое качество строительства, но и дать серьезную экономию по результатам работы.
Дело в том, что стоимость бетона не превышает 8–10% от общих расходов на возведение объекта. И много сэкономить на нем в любом случае не получится. А использование более качественного бетона с современными добавками и инновационными технологиями при небольшом повышении цены материала (ориентировочно на 10–15%) позволяет существенно – на несколько месяцев – ускорить возведение объекта. А это – экономия на обслуживании кредитов, на оборачиваемости опалубки, на оплате рабочей силы, арендованного оборудования и пр. Это работа без неустоек и конфликтов с властями и заказчиками, а в случае госзаказа или при возведении жилья – это соблюдение сроков ввода, отсутствие необходимости переделок и прочих «радостей» (достаточно вспомнить «аммиачные квартиры»).
Таким образом, «перерасход» средств на качественный бетон полностью компенсируется и даже обеспечивает снижение общих затрат на возведение объектов.