Опыт одновременного строительства подземной и надземной частей здания методом up-doun
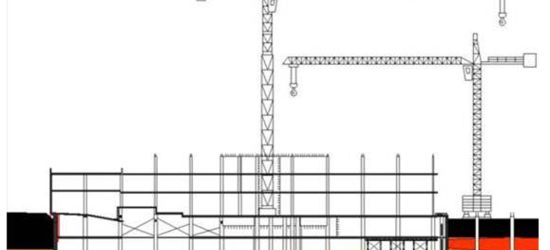
В условиях плотной городской застройки, а также дефицита свободных участков подземное строительство приобретает особую актуальность, однако местная специфика и гидрогеологические условия делают задачу возведения подземных объектов очень непростой. Это стимулирует инженеров использовать новые методы, которые обеспечивают безопасную эксплуатацию окружающей застройки, позволяют проводить подземные работы практически на любой глубине даже в самых сложных инженерных и геологических условиях. Одним из таких является метод up-down, или «вверх-вниз». Такой способ позволяет на нулевой отметке выполнить перекрытие и продолжить строительство одновременно как вверх, так и вниз. Данная технология является актуальной в современных условиях строительства, так как позволяет возводить здания с меньшим задействованием близлежащих территорий. В статье описан принцип технологии up-down, представлен порядок производства работ, рассмотрены основные преимущества и недостатки данного метода, приведены результаты геотехнического мониторинга окружающей застройки.
Основной областью применения метода up-down является устройство глубоких котлованов в пределах плотной городской застройки. Обычно этот метод используется при невозможности выполнения грунтовых анкеров вследствие стесненных условий и существующей развитой подземной части на соседних участках [1–7]. Кроме того, этот метод используется при малых допустимых деформациях окружающих зданий и сооружений. Явным преимуществом метода up-down является высокий темп строительства при устройстве высотной части (рис. 1).
Рис. 1. Схема производства работ по методу up-down
При многих преимуществах этого метода строительства он в большинстве случаев ведет к удорожанию строительного производства по сравнению со строительством в открытом котловане. Особую сложность представляет собой организация снабжения и логистики при подобном виде работ [8]. Следует отметить, что устройство подземной части по методу «вверх-вниз» требует высокой квалификации подрядчика и детальной проектной проработки [9].
Для производства работ по устройству подземной части при данном методе строительства используется технологии «стена в грунте» и струйная цементация грунта (Jet-grouting). Проектирование конфигурации стены выполняется с учетом особенностей технологического оборудования (гидрофрезы). В ходе подготовительных работ по контуру будущей ограждающей конструкции выполняется форшахта шириной 60…80 см и глубиной до 3,0 м. Стенки форшахты раскрепляются железобетонными монолитными конструкциями.
Разработка грунта в траншее и бетонирование выполняются под защитой глиняного тиксотропного раствора, приготовляемого из бентонитовой глины, что обеспечивает устойчивость стенок траншеи от обрушения. Параметры раствора корректируются при производстве работ на опытном участке.
Укладка бетонной смеси панелей ограждающей конструкции производится методом вертикального подъема трубы. Бетонирование стен под защитой глиняного раствора должно выполняться не позднее чем через 8 часов после образования траншеи в захватке. Бетонирование одной захватки проводится непрерывно на всю высоту. Между захватками выполняется холодный рабочий шов, а армирование захватки — сборными пространственными арматурными каркасами. Глубина ограждающей конструкции по данной технологии может достигать 25…30 м.
По грунтовым условиям «стена в грунте» может применяться в любых дисперсных грунтах.
При устройстве больших котлованов, внутри которых возводится здание или сооружение, ограждающие конструкции, выполненные методом «стена в грунте», используют как внешние стены подземной части. В этом случае нагрузка от здания передается на фундаменты, не связанные с ограждающими стенами.
При необходимости ограждающие конструкции, устраиваемые методом «стена в грунте», могут выполнять двойную функцию: являются и ограждением котлована, и конструктивным элементом.
Современные технологии позволяют устраивать конструкции подземных сооружений разных форм, но традиционные и наиболее часто встречающиеся — конструкции из прямолинейных стенок.
При наличии грунтов, содержащих твердые включения природного или техногенного происхождения (крупные валуны, обломки бетонных конструкций, каменной кладки и др.), при проходке траншеи используется техника, оснащенная фрезерным оборудованием, например, фирм «Бауэр», «Касагранде».
Использование грейферного оборудования, которым крупные включения извлекаются, может привести к деформированию стенки траншеи, падению уровня тиксотропного раствора и деформациям окружающего массива и близ расположенных зданий.
Для надежного уплотнения проблемных стыков между панелями траншейных стен, как показал опыт строительства, успешно может быть применена технология струйной цементации jet-grouting. Она заключается в разрушении и перемешивании грунта мощнонапорной струей цементного раствора, исходящего под высоким давлением из монитора, расположенного на нижнем конце буровой колонны. В результате в грунтовом массиве формируются сваи диаметром 0,6–1,5 м из нового материала — грунтобетона с достаточно высокими несущими и противофильтрационными характеристиками. При этом цементационные работы могут выполняться как снаружи ограждающих котлован стен, так и изнутри котлована до его разработки. С этой целью в зависимости от прогнозируемой величины раскрытия стыков с глубиной могут быть применены неармируемые или армируемые металлическими трубами грунтоцементные колонны диаметром 60 или 80 см.
Для разработки грунтового ядра внутри подземного сооружения, возводимого способом «стена в грунте», рекомендуется применять технологию, которая предусматривает разработку вначале центральной части грунтового массива на глубину одного яруса с сохранением по периферии нетронутых участков. Такой прием облегчает работу ограждающей конструкции. Затем монтируются распорные конструкции, и разрабатывается оставшаяся часть грунта. Одним из существенных преимуществ данных технологий является возможность устройства как отдельных, так и протяженных подземных конструкций с поверхности земли без экскавации котлована [10].
Производство работ по методу up-down считается одним из самых сложных видов строительного производства с геотехнической точки зрения и предусматривает комплексную программу мониторинга в период строительства здания [11].
- Характеристика объекта строительства
Рассматриваемая площадка строительства обладает практически всеми перечисленными осложняющими факторами:
Инженерно-геологические и гидрогеологические условия.
В геологическом строении площадки принимают участие следующие элементы (рис. 2): ИГЭ-1. Современные техногенные отложения, песчано-суглинистые грунты со щебнем кирпича. ИГЭ-2. Глина мягкопластичной консистенции. ИГЭ-3. Суглинки мягкопластичной и тугопластичной консистенции. ИГЭ-4. Супеси пластичные. ИГЭ-5. Пески пылеватые, средней плотности, водонасыщенные. ИГЭ-6. Пески мелкие, средней плотности, водонасыщенные. ИГЭ-7. Пески средней крупности, средней плотности, водонасыщенные. ИГЭ-8.1. Глина полутвердая. ИГЭ-8. Мергель малопрочный. ИГЭ-9.1. Известняк, разрушенный до щебня и дресвы. ИГЭ-9. Известняк малопрочный. ИГЭ-10. Глина полутвердая.
Подземная вода встречена на глубине 3,7…4,0 м от поверхности.
В представленных инженерно-геологических условиях, при наличии в основании значительной толщи слабых грунтов и высоком уровне грунтовых вод, основным требованием к ограждающей конструкции котлована является обеспечение минимального поступления воды в котлован и ограничение дополнительных вертикальных перемещений окружающей застройки. Для определения зданий и сооружений, на которые возможно влияние от строительства проектируемого, предварительно назначается 30-метровая зона, которая впоследствии уточняется расчетами. Выполняется обследование зданий, определяется история их строительства, техническое состояние основных конструктивных элементов. Величина допустимого влияния определяется исходя из условия обеспечения надежности здания и зависит от его технического состояния и конструктивной схемы.
Рис. 2. Инженерно-геологический разрез площадки строительства
Градостроительная и геотехническая ситуация.
Строящееся здание возводится в существующем квартале исторической застройки на месте демонтированного здания. При этом по градостроительным условиям было необходимо сохранить исторический фасад здания, выходящий на улицу. В зону влияния строительства попадают 15 зданий, техническое состояние зданий по результатам обследования оценено как удовлетворительное, предельные дополнительные осадки этих зданий ограничены диапазоном 10…30 мм. Для обеспечения сохранности и механической безопасности зданий при производстве работ по строительству здания и в ходе его эксплуатации необходимо было выполнить комплекс работ по улучшению механических свойств грунтовых оснований (метод компенсационного нагнетания цементного раствора) и усилению конструкции фундаментов. На всех этапах производства работ был организован мониторинг за развитием вертикальных перемещений и техническим состоянием основных конструкций зданий. Схема расположения наблюдательных марок приведена на рис. 3.
Рис. 3. Схема размещения наблюдательных марок (вертикальные перемещения)
Характеристика строящегося здания.
Здание монолитное, железобетонное, с максимальной отметкой верха 34,10 м, прямоугольной формы в плане, состоящее из 6-этажной надземной части и 3-этажной подземной части (гаража). Несущие конструкции — продольные и поперечные монолитные железобетонные стены и колонны. Максимальная глубина котлована 12,60 м. Способ разработки котлована up-down: заглубление под защитой дисков плит перекрытий с возможностью одновременного строительства вверх. Конструкция ограждения котлована: траншейная стена толщиной 640 мм, выполняемая гидрофрезерным оборудованием (базовая машина BAUER BG-28 с гидрофрезой BC-32). Фундамент — свайное поле со сваями-бареттами, опирающимися на однородный скальный грунт (известняки). Вся эксплуатационная нагрузка передается на сваи, железобетонная плита подстилающего слоя толщиной 250 мм не связывается со сваями.
2. Последовательность выполнения работ
Производство работ по устройству подземной части здания выполнялось в следующей последовательности:
Этап 1. Выполнение компенсационного нагнетания цементного раствора в грунтовое основание фундаментов зданий окружающей застройки. Усиление конструкции фундаментов зданий окружающей застройки. Устройство буроинъекционых свай в основании фундаментов сохраняемой части фасада (рис. 4).
Рис. 4. Схема выполнения работ по усилению грунтового основания фундаментов существующих зданий
Усиленный таким образом грунтовый массив является новым техногенным образованием, обладающим высокой степенью жесткости. Методика уплотнения позволяет уплотнять не только дисперсные связанные грунты (глины, суглинки, супеси), но и несвязанные дисперсные грунты (пески, насыпные техногенные грунты). Расширение возможностей применения технологии на широком спектре грунтов происходит за счет подбора качественной характеристики раствора, обеспечивающей ее высокую проникающую способность. Наличие грунтовых вод не является противопоказанием к применению высоконапорной инъекции.
Этап 2 (рис. 5). Выполнение форшахт для устройства ограждения по периметру подземной части здания и для выполнения свай-баретт. Производство работ по устройству монолитной железобетонной плиты рабочего уровня с направляющими гильзами для устройства скважин цементации. Бурение скважин и цементация скального грунта. После цементации вдоль периметра ограждения котлована образуется слой скального грунта с достаточными противофильтрационными свойствами для разработки вертикальных траншей
Рис. 5. Этапы устройства форшахт ограждения по периметру и баретт, цементации основания и бетонирования плиты рабочего уровня
Рис. 6. Этапы устройства ограждающей конструкции, свай-баретт и экскавации котлована
под защитой бентонитового раствора. Водопроницаемость зацементированных грунтов контролируется по величине удельного водопоглощения, установленного при гидравлическом опробовании контрольных скважин. В основании баретт формируется непрерывный пласт сплошного зацементированного скального массива с нормативным пределом прочности на одноосное сжатие — R_с≥11,0 МПа. Для контроля прочности выполняется отбор образцов и их лабораторные испытания.
Этап 3 (рис. 6). Устройство траншейной стены ограждения подземной части методом «стена в грунте» гидрофрезерным оборудованием (единичная заходка — 2800 х 640 мм) в две очереди по захваткам с заведением в водоупор (ИГЭ-10) не менее чем на один метр. Устройство замыкающих грунтобетонных элементов, выполняемых по технологии струйной цементации грунта (Jet-1), между криволинейными захватками с заведением до отметки кровли скального грунта (ИГЭ-8).
Этап 4. Устройство баретт (2800 х 640 мм) с «сердечниками» под временные и постоянные железобетонные и стальные колонны и баретт под башенный кран по технологии «стена в грунте».
Этап 5. Демонтаж форшахт и железобетонной плиты рабочего уровня. Устройство фундамента башенного крана. Срубка шламового бетона верхней части ограждения котлована на высоту 500 мм. Устройство обвязочной балки и периферийной части плиты перекрытия на отметке (-0.100) по инвентарной опалубке.
Этап 6. Поэтапная экскавация котлована до отметки -4,550 м. Демонтаж временных колонн.
Этап 7. Устройство монолитной железобетонной плиты перекрытия на отметке (-4.550) по бетонной подготовке. Устройство вертикальных несущих конструкций минус первого этажа.
Этап 8. Устройство центральной части плиты перекрытия с технологическими проемами на отметке (-0.100). Эта конструкция позволяет вести работы по устройству надземной части здания, поскольку опирается на ранее выполненные сваи баретты и не требует устройства фундаментной плиты на минус третьем уровне. Начало строительства надземной части здания без ограничения скорости производства работ и этажности.
Этап 9. Разработка грунта котлована малогабаритной техникой до отметки -8.500. Устройство монолитной железобетонной плиты перекрытия минус второго этажа на отметке -8.200.
Этап 10. Разработка грунта котлована малогабаритной техникой до отметки -12,600 м. Срубка и оформление оголовков баретт. Устройство дренажной системы по дну котлована. Устройство монолитной железобетонной плиты пола минус третьего этажа.
Этап 11. Устройство вертикальных несущих конструкций минус третьего этажа.
Этап 12. Завершение работ по устройству монолитной железобетонной плиты минус второго этажа. Устройство пандусов и лестничных маршей. Устройство внутренней вертикальной гидроизоляции и прижимной монолитной железобетонной стенки на минус третьем этаже. Для устройства монолитной прижимной стенки в перекрытиях были предусмотрены технологические гильзы-направляющие.
Этап 13. Устройство вертикальных несущих конструкций минус второго этажа. Устройство внутренней вертикальной гидроизоляции и прижимной монолитной железобетонной стенки на минус втором этаже.
Этап 14. Ликвидация временного технологического проема в железобетонной плите на отметке -0.100. Демонтаж временных колонн.
Этап 15. Демонтаж башенного крана. Демонтаж ростверка и баретт башенного крана. Устройство внутренней вертикальной гидроизоляции и прижимной монолитной железобетонной стенки на минус первом этаже. Устройство наружной вертикальной гидроизоляции стилобатной части здания и благоустройство территории.
3. Геотехнический мониторинг
В ходе геотехнического мониторинга выполнялись высокоточные геодезические измерения отметок установленных деформационных марок, оценивалась динамика развития вертикальных перемещений зданий и проводилась визуальная оценка их технического состояния. Динамика развития наиболее интенсивных вертикальных перемещений показана на рис. 7. Вертикальные перемещения остальных марок имеют меньшие значения. Относительная разница дополнительных осадок фундаментов существующих зданий также не превысила предельно допустимого уровня.
Рис. 7. Динамика развития вертикальных перемещений деформационных марок
О стабилизации осадок зданий окружающей застройки можно судить по изменению скорости их развития, а она имеет явную тенденцию к снижению. Это можно хорошо проследить на графике построенных по данным наблюдений. Если в начальный период наблюдения она составляла 0,1…0,15 мм/сут, то через 90 суток она составила 0,03…0,45 мм/сут, следовательно, снизилась в 2,5 …3,0 раза. Такое снижение скорости развития абсолютной величины вертикальных перемещений свидетельствует о процессе их стабилизации.
Заключение
Выбор метода производства работ up-down по устройству здания в стесненных городских условиях оказался полностью оправданным. Использованные при реализации этого метода технологии позволили выполнить работы в установленные сроки, с качеством обеспечивающим механическую безопасность как строящегося объекта, так и окружающей застройки. Производство работ хотя и является технически сложным, но при надлежащем уровне мониторинга позволяет оптимизировать сроки проведения работ. Полученный в ходе строительства опыт может быть в дальнейшем использован при проектировании и строительстве объектов такого уровня сложности.
Литература
1. Абелев М. Ю. Особенности технологии проведения работ по устройству фундаментов: Учеб. пособие / М. Ю. Абелев, Б. М. Красновский. М.: Б. и., 1980. — 45 с.
2. Абелев М. Ю. Деформации сооружений в сложных инженерно-геологических условиях. М.: ЦМИПКС при МИСИ им. В. В. Куйбышева, 1982. — 290 c.
3. Строительство зданий и сооружений в сложных грунтовых условиях / [М. Ю. Абелев, В. А. Ильичев, С. Б. Ухов и др.]; под ред. М. Ю. Абелева. М.: Стройиздат, 1986. — 104 с.
4. Абелев М. Ю., Чунюк Д. Ю, Бровко Е. И. Выправление кренов высотных промышленных и гражданских зданий // Промышленное и гражданское строительство. 2016. — № 11. — С. 54–59.
5. Катценбах Р., Шмитт А., Рамм Х. Основные принципы проектирования и мониторинга высотных зданий Франкфурта-на-Майне. Случаи из практики // Реконструкция городов и геотехническое строительство. 2005. № 9. C. 80–99.
6. Конюхов Д. С. Строительство городских подземных сооружений мелкого заложения. М.: Архитектура, 2005. — 298 с.
7. Chang-Yu Ou. Deep Excavations. Theory and Practice. London: Taylor & Francis, 2006. — 532 p.
8. Щерба В. Г., Абелев К. М., Храмов Д. В., Сагалаков Г. В., Бахронов Р. Р. Особенности обеспечения объектов строительства монолитных многоэтажных зданий в стесненных городских условиях. //Вестник МГСУ. — 2008. — № 3. С. 146–149.
9. Юркевич П. Б. Возведение монолитных железобетонных перекрытий при полузакрытом способе строительства подземных сооружений //Подземное пространство мира. — 2002. — № 1. — С. 13–22.
10. Makovetskiy O., Zuev S. Practice device artificial improvement basis of soil technologies jet grouting. Procedia Engineering. — 2016. — Vol. 165: 15th Intern. sci. conf. Underground Urbanisation as a Prerequisite for Sustainable Development 12–15 Sept. 2016, St. Petersburg, Russia. — P. 504–509.
11. Маковецкий О. А. Зуев С. С. Опыт проведения испытаний баретты большой длины в условиях плотной городской застройки // Жилищное строительство. 2018. — № 9 —С. 13–18.
Авторы статьи:
М. Ю. АБЕЛЕВ, С. С. ЗУЕВ , Р. Р. АХМЕТШИН
Центр инновационных технологий в строительстве Института ДПО ГАСИС НИУ ВЩЭ
АО «Нью Граунд»
БКДК: стабильный рынок в ожидании взлета
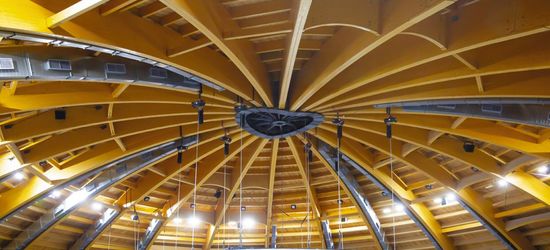
Большепролетные клееные деревянные конструкции (БКДК) –
уникальный материал, с каждым годом увеличивающий свою долю рынка по всему миру.
При этом на строительном рынке России БКДК занимают довольно скромное место, чему, по мнению экспертов, есть ряд объективных причин.
Долговечно, прочно, красиво
БКДК были изобретены еще в начале XX века в Германии, где их использовали при строительстве объектов железнодорожной инфраструктуры. Основным недостатком первых таких конструкций была высокая подверженность материала деформации под воздействием атмосферных осадков и агрессивных сред.
Поэтому массовое использование БКДК в строительстве началось лишь в середине ХХ века, после изобретения целого ряда химических составов для защиты древесины.
По словам директора по маркетингу ООО «Большепролет» Екатерины Фурман, БКДК целесообразно использовать в пролетах длиной от 8 м, что актуально для самых разных помещений, где нет возможности поставить опоры для устройства кровли и перекрытий.
Сегодня эти конструкции находят применение в самых разных областях строительства по всему миру. «БКДК имеют широкую область применения и активно используются при строительстве спортзалов, аквапарков, бассейнов, складов, жилых помещений. Помимо этого, они имеют повышенную химическую и огнестойкость по сравнению с металлическими и железобетонными конструкциями и могут быть использованы для складов материалов с повышенной химической активностью. Также клееные конструкции – стильный элемент декора, который, неся конструкционные нагрузки, отлично смотрится практически в любом интерьере, не требуя дополнительной отделки», – отмечает директор «Первой Загородной Компании» Андрей Кирюшин.
В России и в мире
По данным экспертов, в западных странах более 70% спортивных сооружений, концертных залов и стадионов и других крытых большепролетных зданий возводятся по технологии БКДК. Количество же таких зданий исчисляется тысячами.
К наиболее известным объектам можно отнести такие сооружения, как концертный зал Z´enith de Paris, испанский отель Metropol Parasol, железнодорожный вокзал в Берне (Швейцария), целый ряд куполообразных складских помещений (в Италии внешний диаметр купола одного из них составляет 144 м, а высота – почти 40 м), множество офисных и, конечно, жилых зданий.
Норвегия может похвастаться самым высоким в мире зданием, построенным по технологии БКДК. В марте 2019 года состоялось открытие делового центра Mjоstаrnet Tower в Брюмундале. Высота 18-этажного здания (площадью 11,3 тыс. кв. м) составляет 85,4 м.
В России объемы строительства объектов по данной технологии пока значительно отстают от зарубежной практики. О скромной востребованности таких конструкций на строительном рынке свидетельствуют и объемы производства – по данным экспертов Step Change Consulting, ежегодно в стране выпускается около 420 тыс. куб. м клееных конструкций из цельной древесины и 150 тыс. кв. м LVL-бруса – порядка 4–5% от мирового объема производства.
Между тем отечественные разработки в области БКДК начались еще в 1930-х годах. Но железобетон на время вытеснил «деревянные» технологии из массового строительства, однако постепенно они опять стали востребованы. Из них в военные и послевоенные годы по проектам Центрального НИИ промышленных строительных материалов в стране строились промышленные и производственные помещения, мостовые пролеты и т. д. После распада советской экономики такое строительство фактически прекратилось и получило новый виток развития лишь в новом веке.
По словам генерального директора Ассоциации деревянного домостроения Олега Паниткова, сегодня отношение к деревянному домостроению пусть небыстро и непросто, но меняется. «Мы уходим от образа некой баньки, простенького бревенчатого сруба к современным конструкциям и строительству, которое отличается качеством и скоростью, архитектурной привлекательностью и экономичностью, эффективностью и экологичностью, а главное – обеспечивает высокое качество жизни», – считает он.
Проблемы и перспективы
Одной из проблем, тормозящих развитие строительства с использованием БКДК в России, эксперты называют несовершенство законодательства.
«По нормам, действующим на территории РФ, эти конструкции должны иметь многократный запас прочности, из-за чего приходится увеличивать объем исходного материала, что ведет к удорожанию продукции. Нормы не менялись с советских времен, недавние поправки (сделанные в 2012 и 2014 годах) несущественны. Европейцы уже давно привели в соответствие с реалиями нормативную базу для применения БКДК, мы пока ожидаем», – говорит Екатерина Фурман.
Еще одной причиной низкой востребованности БКДК в России можно считать инертность мышления потенциальных заказчиков, которая сформировалась под влиянием многолетней самодеятельной работы компаний, занимающихся деревянным домостроением без соблюдения каких-либо технических норм и правил.
И, наконец, свою роль играет недостаток опыта, во многом утерянного за десятилетия. Так, если грамотно спроектировать объект с применением БКДК в стране может несколько организаций (ЦНИИСК им. В. А. Кучеренко, университеты Санкт-Петербурга, Москвы и Нижнего Новгорода), то вот архитекторов, готовых работать с данной технологией, пока недостаточно, говорят эксперты.
В ожидании взлета
Даже с учетом всех перечисленных проблем очевидные достоинства БКДК постепенно способствуют их возвращению на рынок. За последние годы в стране возведен целый ряд достойных объектов, не уступающих лучшим иностранным образцам.
Одной из первых ласточек стал казанский Дворец водных видов спорта, который построили к Универсиаде 2013 года. Далее с применением БКДК были построены аквапарк в Новосибирске, ледовая арена во Владивостоке, Олимпийская бобслейная трасса в Сочи, спортивно-концертный комплекс «М-1 Арена» в Петербурге и целый ряд спортивных объектов по программе «Газпром – детям». Компания Good Wood в 2014 году возвела самое высокое офисное здание из древесины в России – Good Wood Plaza, высотой 19,7 м.
Драйвером дальнейшего развития рынка БКДК могло бы выступить жилищное строительство. Тем более, что «увеличение применения деревянных конструкций» входит в число задач, ставящихся перед отечественной строительной отраслью нацпроектом в жилищной сфере. Но нока что здесь все упирается в недоработки российского законодательства. Тем не менее, проблема решается – участники рынка ждут завершения работы над целым пакетом необходимых документов.
По мнению технолога корпорации «Русь» Сергея Шинкаренко, еще одним из направлений развития российского рынка БКДК может стать мостостроение. Сегодня в России капитальных мостов из древесины практически не строится, даже в лесных районах страны, тогда как в Европе подобные сооружения весьма распространены, а их срок эксплуатации нередко превышает 50 и более лет.
Мнение
Екатерина Фурман, директор по маркетингу ООО «Большепролет»:
– Спрос на большепролетные конструкции сегодня достаточно устойчив, без значительных колебаний. Сказывается тенденция роста доверия к подобным зданиям – они сами себя демонстрируют, как, к примеру, внушительные по своим размерам и архитектурному исполнению спортивные дворцы. Заказчику БКДК при выборе поставщика в первую очередь следует обращать внимание на доверие рынка. Если в открытом доступе поставщик публикует информацию о выполненных объектах и устойчивой деятельности, то можно включить его в список претендентов. Далее обратить внимание стоит на удаленность предприятия от места строительства – транспортировка таких крупногабаритных изделий стоит дорого.
Андрей Кирюшин, директор «Первой Загородной Компании»:
– Заказчику стоит обратить внимание на репутацию поставщика, соблюдение им технологии производства, качество поставляемой продукции, а также на общую стоимость предложения. Нередки случаи, когда продавец манипулирует ценой кубометра, а она, как правило, не учитывает всех нюансов и неточно отображает стоимость заказа в целом.
«Зеленый» как доллар
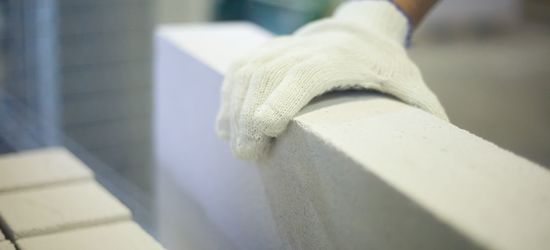
В последнее время при выборе строительных материалов как профессиональные застройщики, так и частники все больше внимания уделяют таким вопросам, как экологичность и безопасность для здоровья человека. И, по данным производителей, газобетон требованиям в этой сфере вполне отвечает.
Там не менее, в сети Интернет обнаруживается информация о неэкологичности газобетона и даже его вредности для здоровья. «Строительный Еженедельник» постарался разобраться в вопросе.
Экогазобетон
По утверждениям производителей, газобетон стопроцентно экологически безопасен. Просто по той причине, что не содержит в своем составе каких-либо вредных для здоровья веществ. «Газобетон является экологически безопасным – как для людей, проживающих в домах с ограждающими конструкциями из этого материала, так и для окружающей среды. В процессе производства автоклавного газобетона участвуют натуральные компоненты, такие как кварцевый песок, известь, вода и цемент. Газобетон является минеральным строительным материалом, который не поддается влиянию плесени и не гниет, к тому же он требует в своем производстве небольшого количества сырья. Из 1 куб. м сырья получают до 5 куб. м продукции», – говорит инженер по применению продукции YTONG Алексей Аверин.
«Газобетон считается высокоэкологичным материалом за счет сырья и технологии производства. В результате термобарической обработки газобетона в автоклаве (высокая температура и давление пара), образуется минерал тоберморит (силикат кальция). Это, по сути, искусственный камень, который не выделяет вредных веществ при эксплуатации – и даже при воздействии огня», – добавляет продукт-менеджер компании «Кселла-Аэроблок-Центр» Павел Коляко.
Коммерческий директор компании «ЕвроАробетон» Дмитрий Щуров подчеркивает, что, говоря об экологичности того или иного стройматериала, рассматривать нужно прежде всего два фактора: радиоактивность и горючесть. «Негорючесть газобетона дает возможность не учитывать столь опасный фактор, как токсичность выделяемых при сгорании веществ. Точно так же к этому материалу неприложимы такие критерии, как скорость распространения пламени или дымообразующая способность. Газобетон даже при высоких температурах ведет себя нейтрально – не поддерживает горение и не выделяет опасных для здоровья субстратов. После пожаров в домах, построенных из газобетона, сам материал остается неповрежденным», – отмечает он.
«По показателю радиоактивности газобетон относится к наименее опасным материалам (первый класс экологической безопасности). Его удельная эффективность естественных радионуклидов ниже 54 Бк/кг при норме 370 Бк/кг. Сходными характеристиками обладают только дерево и гипс, у всех остальных популярных стройматериалов показатель по естественной радиоактивности выше. При этом, в отличие от гипса, газобетон не гниет и не подвержен плесени», – добавляет директор по продажам Н+Н («Эйч плюс Эйч») Сергей Терехов.
По его словам, полную безопасность газобетона подтверждает и строгая экологическая сертификация, которую проходят крупнейшие российские и зарубежные производители. «В 2016 году компания Н+Н получила «зеленый» сертификат EcoMaterial GREEN, который свидетельствует, что ее газобетонная продукция соответствует требованиям стандартов экологической маркировки строительных и отделочных материалов EcoMaterial 1.3. По итогам независимого аудита действие экологического аудита ежегодно продлевается», – подчеркивает эксперт.
Алексей Аверин отмечает также, что после завершения эксплуатационного этапа жизненного цикла газобетон может являться вторичным сырьем. «Также ежегодно перерабатывается 95% образовавшихся отходов производства», – добавляет он.
Немного о мифологии
По словам экспертов, распространяемая в Интернете информация о низкой экологичности газобетона может иметь две основных причины появления. Во-первых, это может быть следствием элементарной некомпетентности в вопросе. Во-вторых – проявлением недобросовестной конкуренции со стороны производителей других стройматериалов, которые вместо того, чтобы отстаивать достоинства своей продукции, концентрируются на необоснованной критике чужой.
«Иногда возникающую в Интернете информацию о низкой экологичности газобетонных блоков можно объяснить незнанием сырьевой составляющей газобетона или технологии производства», – полагает Павел Коляко. «Следует сказать о разнообразных мифах, которыми некоторые пугают потребителей продукции. Например, иногда говорят, что газобетон – «химический материал». Оспорить это невозможно просто по той причине, что в природе все материалы – химические, состоящие из элементов таблицы Менделеева. Одним из таких «химических» компонентов газобетона называют алюминиевую пудру, которая добавляется в газобетон в малом количестве (0,1% по массе) для газообразования. Но этот материал после завершения процессов структурообразования конечного изделия находится в нем в связанном состоянии в составе комплексных соединений и никакого вредного влияния оказать не может. При этом какие бы то ни было синтетические вещества в составе газобетона отсутствуют», – подчеркивает Дмитрий Щуров.
О том же говорит Алексей Аверин. «Алюминий, являющийся основой порообразователя в газобетоне, в результате химической реакции образует гидроалюмосиликаты, индифферентные соединения, не более опасные, чем стоящая на полке кухонного шкафа алюминиевая кастрюлька», – отмечает он.
Мнение
Дмитрий Щуров, коммерческий директор компании «ЕвроАробетон»:
– Практически любой материал, даже дерево, содержит в мизерных объемах радиоактивные вещества. Их легкий «фон» никак не влияет на здоровье человека. Для материалов, применяемых в жилищном строительстве, норма радиоактивности составляет 370 Бк/кг. Таким образом, газобетон, «фон» которого ниже 54 Бк/кг, относится к наименее опасным материалам. Такой показатель соответствует условному первому классу (низкий уровень) экологической опасности.