«Баррикада»: ставка на результат

Стартовавшая чуть менее двух лет назад модернизация АО «ПО «Баррикада» принесла предприятию первые положительные результаты. Компания из Гатчины за несколько месяцев увеличила объемы и расширила рынок сбыта железобетонных изделий, а также снизила себестоимость производства продукции.
Производитель железобетонных изделий – АО «ПО «Баррикада», расположенное в Гатчине, – переживает свое перерождение. С приходом нового собственника на предприятии началось масштабное технологическое перевооружение. Это помогло компании сделать продукцию более конкурентоспособной и качественной, при этом снизить издержки на ее выпуск. Руководство производственного объединения «Баррикада» не собирается останавливаться на достигнутом и готово продолжать дальнейшую модернизацию предприятия.
Напомним, в марте 2018 года московский девелопер «ТОРОС» выкупил у ПАО «Группа ЛСР» 100% акций АО «ПО «Баррикада». Новыми собственниками была поставлена цель – существенное развитие предприятия. Для достижения этой задачи было инвестировано в производство и инфраструктуру более 120 млн рублей. Было приобретено современное оборудование известных мировых производителей из Германии, Финляндии, Италии, Франции, Швейцарии, необходимое для выпуска высококачественных железобетонных изделий.
Наиболее сложным нюансом проводимой модернизации, как отмечают специалисты, является то, что все работы проводятся без остановки производства. Предприятие связано договорными обязательствами, которые должны быть выполнены в полном объеме в установленный срок и без оглядки на проводимые мероприятия. Более того, загрузка производственных мощностей на протяжении последнего года была близка к максимальной, что также оказывает существенное влияние на организацию работ. Так, иногда приходилось полностью воссоздавать параллельную действующей систему-дублер, а потом в считанные часы переключаться со старой на вновь установленную.
В интересах Минобороны
Одним из важных направлений деятельности АО «ПО «Баррикада» является производство плит аэродромных гладких (ПАГ). В ноябре 2018 года предприятие было признано единственным поставщиком ПАГ в интересах Минобороны РФ и в настоящее время продолжает выполнять гособоронзаказ.
Для производства аэродромных плит в необходимом объеме была перепрофилирована действующая линия производства трехслойных стеновых панелей немецкой компании Weckenmann. При этом само демонтированное оборудование сохранено на случай возврата к выпуску предыдущего типа изделий. В рамках модернизации оборудования под изготовление ПАГ линия была доукомплектована специально разработанными для предприятия новыми формами итальянской фирмы Plan. На ней задействовали вибростол российской разработки и новые кантователи, переворачивающие плиты в рабочее положение, под изделия были адаптированы бетонораздатчик и система безопасности. В целом, отмечают представители предприятия, новая линия производства ПАГ, благодаря дублированию постов уплотнения бетонной смеси, участков армирования и предварительного натяжения арматуры, кантования и вывоза готовой продукции, получилась очень простой, надежной и технологичной.
В настоящее время «Баррикада» выпускает всю линейку номенклатуры ПАГ в соответствии с ГОСТ 25912-2015. Она подразделяется на ПАГ-14, ПАГ-18, ПАГ-20. Для достижения высоких качественных характеристик продукции на предприятии в полном соответствии с требованиями нормативной документации организованы входной, операционный и приемочный контроли. Входной включает строгий контроль качества поступающих сырьевых материалов и комплектующих. Операционный – контроль продукции на промежуточных этапах производства. Он проводится при изготовлении бетонной смеси, арматурных изделий, при подготовке формовочной оснастки, армировании и формовании изделий и осуществлении тепловой обработки. Приемочный контроль оценивает соответствие геометрических параметров и фактических характеристик бетона заданным проектным. Помимо этого, в обязательном порядке проводятся испытания готовых изделий на жесткость и трещиностойкость.
Системный подход
Стоит отметить, что на АО «ПО «Баррикада» модернизация коснулась не только линии, выпускающей в настоящее время ПАГ, но и других производств. Технологическое перевооружение носит системный подход. В частности, для удовлетворения спроса на сваи сечением 300х300 мм разработан и изготовлен специальный стенд. В данном случае все работы выполнялись без привлечения иностранных производителей, совместно с российскими компаниями. Проект был реализован за два месяца, многие инженерные решения формировались уже в процессе изготовления. Тем не менее удалось воплотить в жизнь максимально эффективную систему со сниженной потерей тепла. Сейчас стенд полностью загружен работой, однако спрос на сваи этого сечения не удовлетворен. Именно поэтому в марте на предприятии начинает свою работу второй подобный стенд, который сможет увеличить число выпускаемых свай в два раза.
Также на предприятии была проведена модернизация бетонно-смесительных узлов. Она коснулась системы разгрузки вагонов и подачи цемента. Ранее доставка цемента на этот участок производилась автомобильным транспортом, что существенно дороже. После технологического обновления предприятие может принимать цемент, поставляемый в вагонах, что снижает себестоимость материала и дает возможность оперативной поставки цемента от любых производителей, в том числе не представленных на рынке Северо-Западного региона.
В рамках модернизации бетонно-смесительного цеха, в связи с нестабильной работой системы приготовления и транспортировки бетонной смеси, что весьма чревато при жестком графике поставки, было принято решение провести полную замену системы. В качестве партнера для реализации этих целей была выбрана НПК «Сфера». К настоящему времени работы по замене системы выполнены на 70%. Окончательный ввод в эксплуатацию запланирован на весну этого года, но уже сейчас можно сделать вывод о существенном повышении ее надежности. Сегодня предприятие уже работает с удобной программой, которая достаточно проста в управлении. Стабильная работа всегда обеспечена круглосуточной технической поддержкой фирмы-изготовителя, что очень важно для предприятия.
Новые собственники АО «ПО «Баррикада» частично модернизировали и арматурный цех. Он уже был укомплектован надежным импортным оборудованием, но некоторые производственные процессы на нем требовали изменений. Так, рубка листовой стали для закладных изделий в арматурном цеху велась на гильотинах, это один из наиболее травмоопасных процессов на производстве. В качестве альтернативы был приобретен станок плазменной резки металла. Он заменил собой три старых гильотины. Данная установка имеет более широкие возможности резки листового металла, применяемого в качестве закладных во всех изделиях, ранее приобретаемых в сторонних организациях. Новый станок дает возможность изготавливать детали и запасные части для проведения ремонтных работ. Так, например, сейчас специалисты самостоятельно изготавливают отдельные части брони для бетоносмесителей и другие сложные изделия для ремонта оборудования.
Для усиления арматурного производства в части изготовления каркасов для производства свай была приобретена машина для стыковой сварки арматуры МСО 750.02 производства ТЦ «Техносвар». Отмечается, что МСО 750 уже имелась на производстве и зарекомендовала себя с положительной стороны. Новая машина подтвердила все ожидания, сейчас она смонтирована и запущена в работу в штатном режиме.
Ставка на энергоэффективность
В настоящее время на предприятии также проходит модернизация электрических инженерных сетей. Переход на энергоэффективные технологии является одним из важнейших факторов функционирования современного технологичного производства.
В 2019 году на предприятии уже была заменена основная часть осветительных приборов в действующих производственных цехах, а также уличное освещение территории предприятия, расположенного на площади 34 га. Было установлено более 450 электроприборов на сумму 5 млн рублей. Новое оборудование экономит порядка 800 тыс. рублей ежемесячно. В этом году планируется полностью перейти на энергоэффективное освещение, это позволит снизить нагрузку на линии освещения, трансформаторные подстанции, продлив их остаточный ресурс. Также в связи с новыми требованиями к энергетической эффективности АО «ПО «Баррикада» полностью отказалось от использования ртутьсодержащих ламп.
Стоит отметить, что в прошлом году была заменена система трубопроводов горячего водоснабжения (400 пог. м), отопительных приборов (230 шт.) в производственных и административно-бытовых помещениях завода. Изготовлено и смонтировано 100 греющих регистров. В 2018 году был произведен монтаж новой системы химической водоподготовки исходной воды, запущена в работу установка деаэрирования воды, используемой в качестве теплоносителя всей системы отопления. Ее применение значительно уменьшает процесс коррозии внутренних поверхностей системы отопления. По словам специалистов, эффект не столь очевиден, однако его сложно будет не заметить в дальнейшем. Установленные новые радиаторы и трубопроводы системы отопления не потребуют замены долгие годы. Да и остаточный ресурс существующих трубопроводов водоснабжения будет значительно увеличен.
Важно добавить, что за последние два года на ПО «Баррикада» произошла не только технологическая модернизация, но и существенно улучшена социальная поддержка всех сотрудников предприятия. Руководство компании постоянно проводит мониторинг рынка труда, что позволяет поддерживать заработную плату сотрудников на уровне, превышающем среднерыночный в регионе, тем самым обеспечивая стабильность состава трудового коллектива. Был открыт лицензированный медицинский здравпункт, модернизирован физкультурно-оздоровительный комплекс с бассейном, организовано бесплатное питание в столовой. В компании уверены, что качественная социальная политика является залогом успешной реализации производственных задач и мотивирует сотрудников на добросовестный эффективный труд.
Кстати
АО «ПО «Баррикада» имеет более чем вековую историю. В 1907 году в Санкт-Петербурге оно было создано как завод по производству цементных труб фирмы «Андрей Б. Эллерс». Производственные и складские помещения организации были построены на Кожевенной линии Васильевского острова. В 1922 году завод был переименован в «Баррикаду». В годы Великой Отечественной войны предприятие выпускало железобетонную продукцию, которая использовалась при обороне Ленинграда. В послевоенные годы предприятие, в состав которого входили несколько площадок, в том числе в Ленобласти, активно занималось изготовлением ЖБИ, необходимых для жилищного и промышленного строительства. В настоящее время на предприятии трудятся более 700 сотрудников. АО «ПО «Баррикада» выпускает полную номенклатуру продукции для строительства административных, промышленных и дорожных объектов. Предприятие является одним из крупнейших в СЗФО.
Мнение
Александр Кокарев, заместитель генерального директора по производству АО «ПО «Баррикада»:
– К особенности модернизации, осуществляемой на производственном комплексе, можно отнести принцип максимального импортозамещения в целях минимизации зависимости от комплектующих импортного производства и, как следствие, – сокращение времени простоя при возникновении неисправности оборудования. В результате очередного этапа модернизации, завершенного в 2019 году, предприятие закупило и ввело в работу оборудование отечественного производства: машина контактной стыковой сварки, станок плазменной резки и раскроя металла с ЧПУ, пара виброплощадок, интегрированных в автоматическую конвейерную линию, два кантователя аэродромных плит, формооснастка и многое другое. В то же время нельзя говорить о попытке полной замены импортного оборудования, да это было бы и неправильно. На предприятии установлены высокоточные и высокопроизводительные машины и линии, зачастую не имеющие аналогов и разработанные специально для наших потребностей, изготовленные ведущими производителями в области технологий производства ЖБИ, для примера: Weckenmann, МВК, Rosenberger, Prinzing, Schnell (Германия), Elematiс, Steel Kamet, Sal Product (Финляндия), Mep, Plan, Schlatter (Швейцария), Ravni (Франция) и др.
Алексей Картунен, главный инженер АО «ПО «Баррикада»:
– Без модернизации предприятия невозможно его устойчивое существование на рынке в условиях конкуренции. «Производи то, что можешь продать» – один из законов маркетинга. Конечно, любому инженеру приятно запускать новое оборудование и смотреть, как успешно работает то, что было написано на бумаге. Практически нет нерешаемых задач, необходимо найти разумный компромисс между инвестициями в модернизацию и получаемым результатом.
Игорь Коваль: «Действующие ГОСТы для добавок в бетон серьезно устарели»
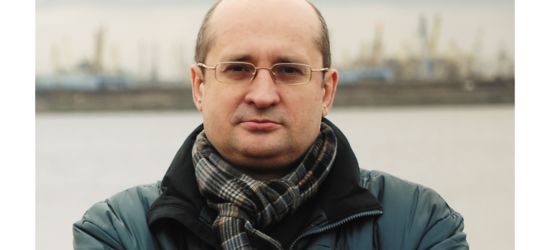
Существующая нормативная база по разработке и применению добавок в бетон требует коррекции. Такие выводы делает руководитель научно-технического центра ООО «Полипласт Северо-Запад» Игорь Коваль. По его мнению, устаревшие ГОСТы не только не позволяют оценивать фактическую эффективность современных добавок, но и тормозят развитие рынка.
– Игорь Валерьевич, действительно ли действующая нормативная документация, а именно ГОСТы на химические и минеральные добавки в бетон, не отвечает запросам производителей?
– К сожалению, это так. Поэтому коррекция нормативов, касающихся применения добавок в бетоне, необходима. Один из важных отраслевых ГОСТ 30459-2008 «Добавки для бетонов и строительных растворов. Определение и оценка эффективности» не пересматривается уже 12 лет. Ряд методик уже не соответствует реальности, они устарели по номенклатуре типов добавок, технологиям производства конструкций, применения бетонов в холодный период года.
В частности, ГОСТ 30459-2008 при оценке эффективности добавок для ЖБИ использует режим прогрева +80 °С. При этом сравнение ведут на контрольном бездобавочном бетоне с величиной осадки конуса ОК = 1–4 см (марка смеси П1) и бетонах с суперпластификатором с ОК = 21 см (марка смеси П5). Техническая проблема в том, что в бетонах с абсолютно разными марками смеси П1 и П5 и неизменной величиной водоцементного отношения в 95% случаев результаты не покажут идентичную прочность – в частности, за счет действия расслоения смеси и погрешности испытаний.
Кроме того, температура +80 °С практически не используется в ЖБИ, КПД, ДСК и отрицательно влияет на физико-механические характеристики бетона по прочности и особенно на параметр качества – долговечность. Производственные режимы на современных продуктах и технологических линиях ограничены +50–60 °С. В связи с этим методика с оценкой при +80 °С и марках смеси П1 против П5 (ОК = 21 см и более), которая в реальности также не используется на заводах ЖБИ (за исключением СУБ или «кассет»), не позволяет оценивать эффективность добавок, т. е. нарушены смысл и цели, декларируемые в данном ГОСТ.
– Какие еще есть несоответствия?
– Серьезные проблемы с методикой оценки эффективности противоморозных добавок по «теплому» и «холодному» методам. Если первый метод используется на практике, то по второму, «холодному», оценить противоморозный эффект добавок почти невозможно. Даже обычные добавки-пластификаторы и просто бездобавочный бетон часто оказываются противоморозными. «Секрет Полишинеля» заключается во времени выдерживания бетона при оттаивании в нормальной температуре (+20 °С). Причем разрешенное время оттаивания до испытаний – от 24 до 48 часов – принимается согласно ТУ производителя добавок. На практике при температуре в теле бетона –12-15 °С не существует химических компонентов, обеспечивающих гидратацию цемента при условии использования добавок в разрешенном нормативами количестве не более 5% от массы цемента. Из этого следует, что бетоны, выдерживаемые по «холодному» методу, не твердеют на проверяемой минусовой температуре и прочность набирают из пластичного состояния смеси сразу после оттаивания за 24 или 48 часов. Ряд технических возможностей и адекватная оценка поликарбоксилатных добавок, несмотря на их активное применение, остались «за бортом» нормативов.
– Помогает ли сертификация добавок в бетон качественному развитию рынка стройматериалов?
– Сертификация – это важно и нужно! Вопрос заключается в квалификации и опыте оценивающих продукцию (бетон). Это скорее вопрос доверия к проверяющим и контролирующим органам, чем к самой процедуре, которая введена правильно.
В формате замещения. Рынок пенополистирола
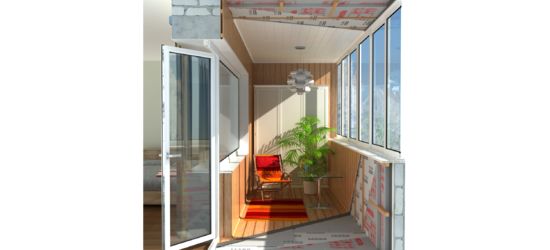
В настоящее время, по данным экспертов, продолжается сокращение производства и потребления вспененного пенополистирола. Освободившуюся нишу все активнее заменяет экструдированный вид этого теплоизоляционного материала.
Пенополистирол широко применяется в строительстве новых зданий и сооружений, а также при отделке помещений. В объеме потребления теплоизоляционных материалов его доля достигает 30%. По оценке экспертов, в ближайшей перспективе она будет постепенно увеличиваться и через 5-7 лет достигнет показателя в 40%.
Генеральный директор АПРИ «Флай Плэнинг» Владимир Савченков отмечает, что главными плюсами пенополистирола являются: широкая сфера применения (от утепления подвальных помещений до использования на балконах, лоджиях и фасадах), а также долговечность, высокие теплоизоляционные свойства, легкость в применении, экологичность и доступная цена. «В качестве недостатков можно указать следующее: это легковоспламеняющийся материал, он разрушается под долгим воздействием солнечных лучей, также он отличается хрупкостью. Поэтому при транспортировке и использовании нужно соблюдать меры предосторожности. Но стоит отметить, что указанные недостатки с лихвой покрываются достоинствами. Это современный технологичный материал с универсальными свойствами и широким перечнем возможностей», – считает он.
Путем продавливания
Отметим, что пенополистирол, как теплоизоляционный материал, подразделяется на два вида: вспененный (EPS) и экструдированный (XPS). Производители данных продуктов между собой достаточно жестко конкурируют.
Согласно исследованию аналитического агентства DISCOVERY Research Group, по итогам трех кварталов 2019 года, объем рынка (производство и потребление) EPS в нашей стране составил 5,49 млн куб. м, XPS – 6,21 млн куб. м. В том числе российскими компаниями за данный период времени было экспортировано 6 тыс. куб. м вспененного пенополистирола и 120 тыс. куб. м экструдированного.
Экструдированный пенополистирол, как рассказывает руководитель направления «Полимерная изоляция» корпорации ТЕХНОНИКОЛЬ Алексей Касимов, создается из полистирола общего назначения (ПСОН) методом экструзии (путем продавливания вязкого расплава материала). В результате получается равномерная мелкопористая структура, что придает материалу прочность, практически нулевое водопоглощение и низкий показатель теплопроводности.
«Экструдированный пенополистирол может применяться в заглубленных конструкциях: фундаменты, подвалы, подземные паркинги, где эффективно защищает фундамент от теплопотерь и разрушительных сил морозного пучения. Также особенностью экструзионного пенополистирола является то, что он может использоваться при температуре от –70°С до +75°С. Благодаря этому материал активно используют в холодильных установках, катках и пр. В целом мы отмечаем ежегодное сокращение рынка EPS, при этом освободившуюся нишу замещает XPS», – добавляет Алексей Касимов.
Отвечая новым требованиям
Эксперты считают, что рост потребления экструдированного пенополистирола связан с трендом повышения энергоэффективности зданий. В частности, стандартный слой плит из этого материала в 50 мм сохраняет тепло в помещении так же, как метровая кирпичная или бетонная стена толщиной 2,5 м. Также XPS все активнее применяется в дорожном строительстве для предотвращения морозного пучения полотна. Материал препятствует промерзанию грунта и значительно увеличивает срок эксплуатации дорожного покрытия. Кроме того, экструдированный пенополистирол более прост в переработке – и его производители могут заниматься выпуском вторичных продуктов.
В целом, как отмечают игроки рынка, применение XPS позволяет существенно усовершенствовать и ускорить технологию строительства, значительно снизить затраты при создании новых конструкций, отвечающих новым требованиям строительных норм.
При этом они подчеркивают, что EPS как теплоизоляционный материал не уйдет с рынка совсем. Он останется востребован в бюджетном строительстве и утеплении малоэтажных индивидуальных домов. Кроме того, за счет совершенствования технологий производства этого материала будут повышаться его качественные характеристики и расширяться область применения.
Кстати
С 1 января 2020 года, в соответствии с приказом Росстандарта, в общероссийском классификаторе ОКПД 2 выделены отдельные коды для теплоизоляционных плит из пенополистирола, сэндвич-панелей с пенополистиролом и сэндвич-панелей с минеральной ватой. Предполагается, что это новшество поможет лучше идентифицировать теплоизоляционные продукты в области их применения, а также повысит качество сбора статистической информации, необходимой в том числе для оказания мер господдержки. Изменения в классификаторы подготовлены на основании предложений технической рабочей группы «Ассоциация производителей и поставщиков пенополистирола» в рамках научно-технического совета по развитию промышленности строительных материалов, изделий и конструкций при Минпромторге РФ.