Москва выделила участок для строительства мебельного производства в Зеленограде
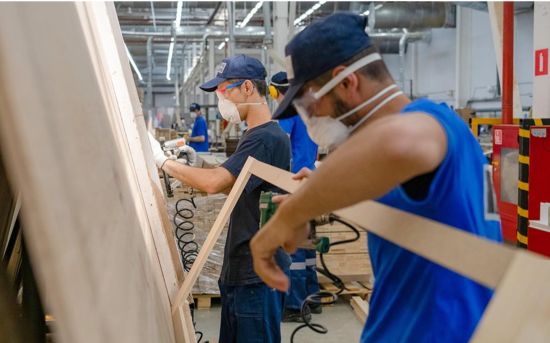
Город заключил с инвестором договор аренды земельного участка по ставке один рубль в год для возведения комплекса по производству мебели в районе Крюково.
Об этом сообщил заместитель мэра Москвы по вопросам градостроительной политики и строительства Владимир Ефимов.
«Город предоставил инвестору в Зеленограде почти 1,5 гектара земли по ставке один рубль в год для возведения комплекса по производству мебели площадью 11,6 тысячи квадратных метров. Компания вложит в проект около миллиарда рублей. На предприятиях будет создано примерно 160 рабочих мест», — рассказал Владимир Ефимов.
Договор заключен с фабрикой «Шарм-Дизайн», которая производит мягкую и корпусную мебель для дома и офиса.
«С 2016 года по распоряжению Сергея Собянина город предоставляет земельные участки для создания производств. Возведение нового промышленного комплекса в ЗелАО позволит увеличить производственные мощности московской мебельной фабрики и нарастить выпуск продукции. На новом предприятии будут изготавливать до 30 тысяч единиц мягкой и корпусной мебели в год», — рассказал заместитель мэра Москвы по вопросам транспорта и промышленности Максим Ликсутов.
Выделение земли по льготной ставке для развития производств — одна из мер поддержки бизнеса, которая действует в столице с марта 2022 года. Благодаря ей компании могут снизить затраты на создание рабочих мест и в короткие сроки наладить выпуск важной для столицы продукции. Договор заключается на пять лет, в течение этого времени инвестор должен завершить строительство.
Как отметил министр Правительства Москвы, руководитель Департамента городского имущества Максим Гаман, ранее в Зеленограде город предоставил восемь участков площадью около 40 гектаров по льготной ставке один рубль в год для развития производств. Инвесторы возведут предприятия по выпуску строительных материалов, одежды, мебели, косметики, внедорожных домов на колесах и другой продукции. Общая площадь недвижимости составит 352 тысячи квадратных метров.
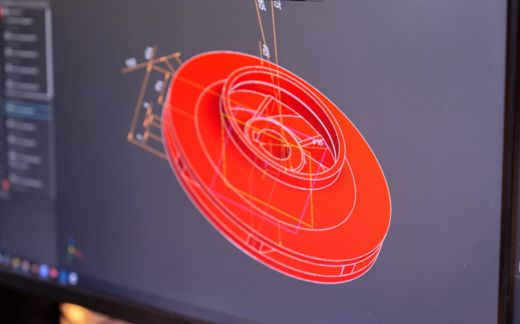
По итогам первого года применения аддитивных технологий в теплоэнергетике ГУП «ТЭК СПб» изготовило 200 деталей оборудования для котельных способом 3D печати.
За год на предприятии произведено более 210 единиц продукции 49 наименований. Среди выпускаемых деталей – механические комплектующие для автоматических горелок, крыльчатки охлаждения, торцевые уплотнения, уплотнительные кольца для насосов и другие запчасти.
3D-принтеры позволяют теплоэнергетикам создавать снятые с производства и недоступные импортные запасные части, менять их вне целого комплекта, избегать простоя оборудования. Так минимизируется зависимость от поставщиков и логистики, сокращается время ремонта. За год 3D-печать позволила сохранить порядка 20 единиц оборудования. Запчасти подтвердили свою надежность при длительной эксплуатации.
«Инновационные проекты петербургских энергетиков решают поставленные Президентом России задачи по достижению технологического суверенитета страны. Способствуют импортозамещению. Внедрение новых технологий в жизнеобеспечивающих сферах способствует повышению комфорта горожан, что соответствует приоритетам развития города на ближайшие годы. Речь о таких отраслях, как промышленность, здравоохранение, общественный транспорт, образование и наука, забота о детях и людях «серебряного возраста»», - подчеркнул губернатор Александр Беглов.
Он отметил, что новый способ производства комплектующих для теплоэнергетики уже повысил надежность теплоснабжения полумиллиона петербуржцев. Использование 3D-печати позволило оперативно и своевременно провести ремонт на источниках, снабжающих теплом и горячей водой 1940 зданий, в том числе 980 жилых домов, 170 детских садов, школ, больниц и других социальных учреждений.
При производстве деталей с помощью 3D-принтеров специалисты ГУП «ТЭК СПб» создают все запасные части с нуля. Эскизы строятся на основе ранее изготовленных, старых, а иногда и сломанных запчастей. Затем разрабатывается 3D-модель, которая загружается в специальную программу. Для печати необходимо задать до 600 параметров – каждый из них, как и материал для печати, подбирается под конкретную деталь. Принтер работает со скоростью 600 мм/сек, а печать занимает от 20 минут до нескольких часов. Так, порядка 16 часов ушло на производство крыльчатки охлаждения диаметром 35 сантиметров. Деталь успешно эксплуатируется в составе оборудования Приморской котельной.