ОАО «АБЗ-1» осуществило первую купонную выплату держателям облигаций на сумму 89,76 млн рублей
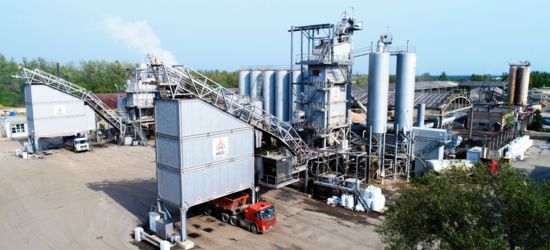
29 марта были произведены квартальные выплаты купонов по облигациям ОАО «Асфальтобетонный завод №1» (входит в ГК «АБЗ-1»). В общей сложности держателям облигаций выплачено 89 760 000 руб. Размер доходов, выплаченных по одной облигации за первый купонный период, составляет 29 руб. 92 коп. (12.00% годовых). Следующая ежеквартальная выплата купонов по облигациям ОАО «АБЗ-1» состоится в 28.06.2021 года.
Руководитель и основной акционер ГК «АБЗ-1» Владимир Калинин отмечает, что в условиях колебаний рынков и снижения ставок по вкладам внимание к инвестиционным продуктам со стороны частных инвесторов растёт. Держатели облигаций ОАО «АБЗ-1» приобрели высокодоходный и ликвидный биржевой актив. «Для Группы компаний выпуск ценных бумаг даёт возможность выстраивать долгосрочные надежные отношения с инвесторами и, как следствие, привлекать дополнительные денежные средства через новые выпуски облигаций на развитие технологических мощностей и реализацию перспективных проектов Группы», - добавляет руководитель ГК «АБЗ-1».
Напомним, что ГК «АБЗ-1» стала первым из региональных игроков инфраструктурного строительства, успешно вышедшим на публичный рынок долговых ценных бумаг в РФ, разместив на Московской Бирже дебютный выпуск 3-х летних облигаций серии 001Р-01 объемом 3 млрд. рублей. Организаторами размещения выступили Газпромбанк, BCS Global Markets, Совкомбанк и СКБ-банк. Действующий кредитный рейтинг облигационного займа серии 001Р-01 компании «АБЗ-1» - ruBBB- (Рейтинговое агентство «Эксперт РА», прогноз стабильный).
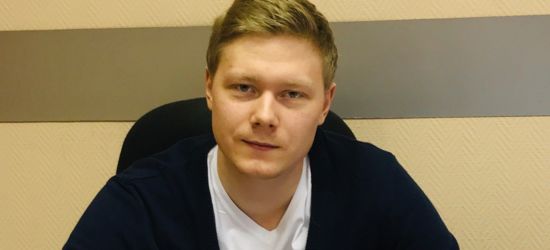
Ученые Санкт-Петербургского государственного архитектурно-строительного университета разрабатывают инновационные технологии строительства. Аспирант кафедры технологии строительных конструкций Александр Копосов выиграл грант в конкурсе, который проводил Комитет по науке и высшей школе Правительства Санкт-Петербурга.
Грант получен на научную разработку по теме «Одноэлементная плоская строительная система высокоскоростного монтажа многоэтажных полносборных зданий». Мы задали молодому ученому несколько вопросов.
– Александр, какие задачи решает ваша научная работа?
– Технической задачей моей разработки является снижение сроков строительства зданий, повышение качества строительства за счет создания элементов в заводских условиях, повышение энергоэффективности и расширение архитектурно-планировочных возможностей. Поставленная задача решается тем, что все здание изготавливается из одинаковых строительных элементов, которые производятся в заводских условиях и проходят ряд испытаний на прочность, гибкость и энергоэффективность. Строительный элемент состоит из стального каркаса, остекленения, элементов крепления остекленения к стальному каркасу. Последний снабжен болтовыми отверстиями для присоединения элементов друг к другу с помощью высокопрочных болтов и планок. Швы, заполненные герметиком, не превышают 3 мм.
Общая толщина строительного элемента составляет 5,85 см., внешний слой имеет термоотражающие свойства. Внутренний слой стекла каленый, что позволяет придать стеклянной составляющей особую прочность, а при повреждении минимизирует количество осколков. Выбор аргона в качестве воздушной прослойки обусловлен тем, что теплопроводность этого газа составляет 0,68 от воздуха. Также большим плюсом является большая вязкость аргона, что снижает скорость конвекции, и, соответственно, теплообмен между стеклами. Типовые элементы на основе стали и стекла позволят обеспечить наиболее эффективный способ возведения быстровозводимых энергоэффективных зданий и сооружений.
Моя научная разработка публиковалась в частных журналах, она представляет собой мою магистерскую работу.
– Почему вы выбрали эту тему для своего научного исследования?
– Она продолжает тему докторской диссертации моего научного руководителя доцента кафедры технологии строительного производства, к.т.н. С. А. Сычёва. Моя научная разработка представляет собой часть большой работы, которую он проделал.
– Заинтересовались ли производители вашими идеями?
– Я получил патент на свое изобретение не так давно. Сейчас мы ждем патент на монтаж, после чего появится возможность продвигать технологическое решение на строительном рынке. Пока что это теоретическая разработка, подтвержденная нашими расчетами и не имеющая зарубежных аналогов. В дальнейшем я планирую выходить на производителей и предлагать им свою разработку.
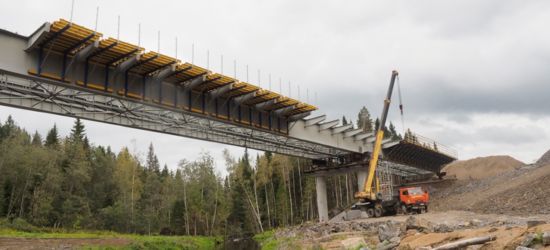
Строительные работы по возведению моста через реку Иййоки в Лахденпохском районе Республики Карелия перешли на новый этап – завершено бетонирование двух из пяти захваток монолитной железобетонной плиты пролётного строения моста.
Возведение моста на строящемся участке автомобильной дороги А-121 «Сортавала» ведется акционерным обществом «Карелстроймеханизация» (АО «КСМ»). Поставщиком опалубочных решений выступило ООО «Дока Рус» - представительство австрийского концерна Doka GmbH на территории РФ.
Строительство сталежелезобетонного моста общей длиной 162,85 м и шириной 13,22 м началось в марте 2018 года, чему предшествовало несколько месяцев подготовки. ООО «Дока Рус» было привлечено в качестве партнера с первых дней разработки проекта. Это позволило учесть все пожелания заказчика - АО «КСМ» - и найти решение самых сложных задач.
Например, скорость и простота сооружения консольных частей монолитной железобетонной плиты пролётного строения были достигнуты благодаря применению специальной опалубки для мостов ParaTop Doka. При использовании ParaTop нет необходимости в подмостях или лесах под плитой пролетного строения - все опалубочные работы и бетонирование выполняются сверху, что требует лишь работы крана. В данном случае бетонирование плиты пролетного строения происходит в пять захваток с использованием всего двух комплектов опалубки. Кроме того, большие габариты платформы ParaTop Doka обеспечивают высокую скорость процесса.
При строительстве моста использовался арендный материал Doka, что являлось требованием заказчика. Для возведения круглых стоек промежуточных опор моста диаметром 1,3 м была выбрана балочно-ригельная опалубка Doka Top 50. Это конструкция из крупнощитовых модульных элементов, форма и размер которых могут быть оптимально адаптированы к конструкции сооружаемого объекта. Для устройства ригелей промежуточных опор моста использованы опорные леса Staxo 100 Doka с прочными стальными рамами, которые специально рассчитаны на большую высоту и значительные нагрузки.
Вышеперечисленные опалубочные решения Doka в сочетании с глубокой экспертизой отрасли, тысячами реализованных проектов по всему миру и 150-летней историей компании позволили обеспечить высокую экономическую эффективность проекта для заказчика в части возведения монолитных конструкций.