Нашим строителям нужны российские трубы
Строительной отрасли и ЖКХ не грозит остаться без качественных полимерных изделий из-за ухода с рынка зарубежных поставщиков. На днях крупнейший производитель полимерных труб на Северо-Западе РОСТерм запустил новое производство по выпуску кабель-каналов из ПВХ и заявил об амбициозных планах на будущее.
Счет идет на миллионы
История производства РОСТерм начиналась в 2014 году с единственной линии по выпуску трубы из сшитого полиэтилена PE-Xb. С тех пор парк производственного оборудования многократно вырос, ассортимент продукции значительно расширился, а общий объем выпуска за прошедшие годы превысил 150 млн метров полимерных труб и 30 млн фитингов.
Основной производственный актив компании — завод в Санкт-Петербурге, выпускающий трубы и фитинги из полипропилена, трубы из сшитого полиэтилена PE-Xb и PE-Xa, термостойкого полиэтилена PE-RT, гофрированные трубы, фасонные элементы и комплектующие для монтажа — всего 25 тысяч товарных наименований. Предприятие может выпускать до 55 млн метров труб в год.
— Завод производит в сутки из сшитого полиэтилена примерно 20 км труб для теплого пола и от 10 до 20 км труб для отопления при горизонтальной разводке, — поясняет коммерческий директор дилерской структуры предприятия ООО «РТСЗ» Максим Кордюков. — Выпуск полипропиленовой трубы составляет 60—80 километров на четырех производственных линиях.
В 2022 году спрос на продукцию РОСТерм резко вырос: по итогам первых десяти месяцев поставки труб из сшитого полиэтилена увеличились втрое, фитингов — в шесть раз, переработка полипропилена — на 50% по сравнению с прошедшим годом. На руку отечественным производителям сыграл уход с российского рынка зарубежных поставщиков полимерных труб Uponor и Rehau. Свободную нишу уверенно занял флагманский продукт РОСТерма — аксиальная система PE-Xa, для которой трубы из сшитого полиэтилена, фитинги PPSU/PVDF и гофрированная труба изготавливаются на одной площадке. К началу 2022 года завод занимал второе место по выпуску труб PE-Xa, а сейчас является единственным в России производителем системы PE-Xa. В этом году РОСТерм запустил в производство фитинги диаметром до 125 мм и вывел на рынок новую продукцию из ПНД и ПВХ для электрики под торговой маркой MIRKL: гофрированные кожухи из ПНД и ПВХ, распределительные коробки и кабельные каналы.
— В марте 2022 года мы изменили стратегию развития предприятия и инвестировали в производство труб PE-Xa, — рассказывает генеральный директор ООО «РТСЗ» Александр Дядин. — Две дополнительные линии из четырех запланированных запустим уже в декабре, что увеличит выпуск самой востребованной строительным рынком трубы в два раза — с 6 млн метров в этом году до 12 миллионов в следующем — этого хватит на оснащение 400 новых жилых домов.
Сквозь огонь, воду и экструдеры
Производство РОСТерм — это 10 линий и 12 термопластавтоматов на одной площадке. Процесс производства всех полимерных труб состоит из схожих этапов: сырьевые гранулы загружают в бункеры с высокоточными дозаторами, смесь нагревают в камерах для получения пластичной массы, из которой с помощью экструдеров формируется готовое изделие заданного диаметра. После вакуумного калибратора трубу охлаждают в водяной ванне, которая тянется на десятки метров через весь цех. После охлаждения трубу еще раз калибруют, маркируют, разрезают и отправляют на склад.
Отличия между линиями в том, что для производства трубы PE-Xa используется технология сшивки молекул с добавлением пероксида в инфракрасной печи, а для PE-Xb — с добавлением кремния под действием высоких температур. Для получения полипропиленовой армированной трубы в экструдере формируется трехслойный композит, в котором средний слой из компаунда со стекловолокном соединяется под действием давления и температуры с частицами полипропилена. В итоге получается прочная монолитная конструкция, в которой прослойка из стекловолокна уменьшает коэффициент теплового расширения и служит дополнительным барьером для проникновения кислорода сквозь стенку трубы.
В этом году на заводе налажен самостоятельный выпуск компаунда из сырья с предприятий СИБУР и ЛУКОЙЛ. Теперь технологи могут контролировать качество всех компонентов полипропиленовой трубы, а качеству в РОСТерм уделяют огромное внимание. Так, для комбинированных фитингов закладные изготавливаются только из латуни 617, а не из оцинкованной стали, а сами фитинги формируются «с запасом» по толщине стенок. Основная номенклатура производится только из первичного сырья, хотя стандарты допускают использование отходов.
— Все дозаторы на линиях автоматизированы, — рассказывает Александр Дядин. — Это позволяет при запуске минимизировать пусковой брак. На линиях каждый час автоматически срезается кусок трубы, и оператор измеряет толщину, диаметр, овальность. Образцы из каждой партии поступают в лабораторию для углубленных испытаний.
Проверка на стрессоустойчивость
Аккредитованная лаборатория РОСТерм обеспечивает непрерывный контроль соответствия продукции заданным параметрам и требованиям ГОСТов при приеме сырья и комплектующих, в процессе производства, в ходе научно-исследовательских разработок, во время приемо-сдаточных испытаний.
Образцы материалов испытывают на растяжение и изгиб, кипятят в агрессивной химической среде, состаривают в гидротанке — все это для того, чтобы убедиться в качестве изделий и гарантировать им не менее 25 лет эксплуатации. Современное оборудование дает возможность определить точную геометрию трубы, степень сшивки полимерного материала, содержание летучих веществ, стойкость соединений под воздействием температуры и давления и другие характеристики в строгом соответствии с ГОСТами.
Лаборатория РОСТерм — одна из немногих в стране, где используется оборудование для ДСК, или дифференциальной сканирующей калориметрии. По словам директора производства Евгения Горбунцова, этот метод определяет «отпечаток пальца» любого полимера.
— Пластики разного качества обладают рядом схожих характеристик, — поясняет он. — А в нашей лаборатории можно не только определить все компоненты состава сырья, но и выяснить, смешал ли поставщик разные партии или добавил в него вторичку.
Подводя итоги
Сейчас линейка продукции РОСТерм из материалов PE-Xa, PE-Xb, PPSU, PVDF, PP-R составляет примерно 80% ассортимента изделий для внутренних систем отопления и водоснабжения. Но компания не останавливается ни на достигнутых объемах производства, ни на ассортименте. Если в начале года на заводе работало 10 единиц оборудования, то сейчас их уже 22, а в следующем году может стать более 30. Под новое оборудование построен цех площадью 2500 кв. м, идет строительство автоматизированного складского комплекса. Дополнительные площади позволят увеличить выпуск трубы PE-Xa и гофрированного кожуха как минимум втрое в 2023 году. Планируется увеличить количество термопластавтоматов до 33 единиц, расширить ассортимент PPSU-фитингов, нарастить количество гильз PVDF в два раза.
— Для нас наступило время возможностей, и мы стараемся его использовать, — считает Александр Дядин. — На рынке востребована продукция, которую еще никто не заместил. Можно переключиться с европейских на китайских или турецких поставщиков, но мы хотим, чтобы строители могли возводить дома из российских материалов.
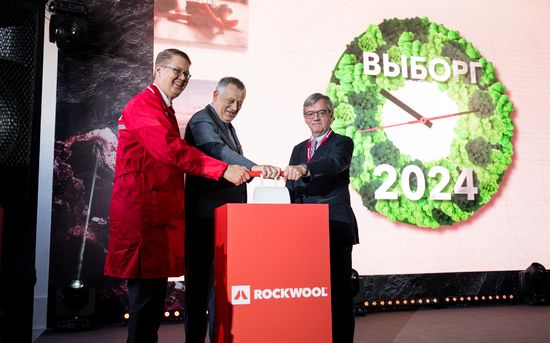
В 2024 году завод ROCKWOOL в Ленинградской области расширится: здесь появится новая инновационная линия по выпуску продукции из каменной ваты. В сочетании с возобновляемыми источниками энергии, это позволит сократить суммарный углеродный след предприятия на 50%. Это отвечает мировому, а теперь и российскому тренду устойчивой экономики.
19 октября старинный Выборг, где расположен один из четырех российских заводов ROCKWOOL, встретил многочисленных гостей первым снегом. Зато внутри предприятия их ждала теплая и дружеская атмосфера: почетным гостям, деловым партнерам и журналистам показали весь цикл производства и познакомили с разными видами выпускаемой продукции. Все они стали участниками торжества, посвященного 15-летию завода и старту нового инвестиционного проекта стоимостью 17 млрд рублей. Благодаря этой инициативе через три года на предприятии будет запущена производственная линия, которая не только увеличит мощность завода, но и будет отвечать принципам устойчивого экологического развития группы ROCKWOOL.
Символический рычаг, который дал старт новому проекту, привели в действие губернатор Ленобласти Александр Дрозденко, посол Королевства Дания в РФ Карстен Сендергорд и президент Группы компаний ROCKWOOL Йенс Биргерссон.
На передовой современных технологий
Группа компаний ROCKWOOL отметила 15-летний юбилей производственной площадки в Ленобласти. Построенный в 2006 году, завод ROCKWOOL — это полностью локализованное высокотехнологичное предприятие по выпуску тепло- и звукоизоляции из каменной ваты. Производственное оборудование позволяет на одной линии выпускать разную по назначению, габаритам и плотности теплоизоляцию.
Плитами из каменной ваты утеплены многие знаковые объекты Санкт-Петербурга: Лахта-центр, здание Конституционного суда РФ, здания Государственного Эрмитажа и многие другие. Теплоизоляция выборгского завода востребована на Северо-Западе и в Центральном регионе, часть продукции экспортируется в Финляндию.
— Ни одна строительная площадка в Ленинградской области не обходится без продукции ROCKWOOL, — рассказал губернатор Ленобласти Александр Дрозденко, отметив, что качественный и долговечный материал давно заслужил уважение у строителей и технологов.
Сегодняшний спрос на продукцию ROCKWOOL огромен: завод работает безостановочно в режиме 24/7. По словам генерального директора компании ROCKWOOL в России Марины Потокер, такой высокий спрос послужил основанием для принятия решения руководством компании по дальнейшему инвестированию в российское предприятие.
17 миллиардов на новое производство
С момента открытия завода за пятнадцать лет работы предприятия группа компаний ROCKWOOL уже инвестировала в его развитие 5,73 млрд рублей, создав производство, которое отвечает всем стандартам безопасности и экологичности с точки зрения как технологических процессов, так и выпускаемой продукции. Сегодня здесь трудится более 230 специалистов. С вводом новой производственной линии будет создано еще около 70 рабочих мест непояредственно на производстве, а также в отделах продаж и логистики ROCKWOOL Россия.
Первый заместитель главы областного Комитета по экономическому развитию и инвестиционной деятельности Егор Мищеряков со своей стороны подтвердил, что регион поддержит проект налоговыми преференциями, так как по объемам инвестиций он включен в реестр региональных инвестпроектов.
— Когда завод был основан, многому предстояло обучиться, и сотрудники проделали большую работу. За пятнадцать лет мы достигли больших успехов, — подчеркнул президент группы компаний ROCKWOOL Йенс Биргерссон. — Завод в Выборге является самым высокопроизводительным и показывающим самый высокий уровень качества из всей группы компаний. Мы благодарны за поддержку и доверие, которые были оказаны на протяжении пятнадцати лет. Инвестиции компании являются в первую очередь подтверждением нашей веры в перспективы развития, в нашу команду, а также желанием стать компанией, работающей по принципам экологичности, устойчивого развития и циркулярной экономики. Многие технологии, которые применяются здесь, уникальны.
— Одно из важных направлений ROCKWOOL — это устойчивое развитие, — отметила Марина Потокер. — На протяжении пятнадцати лет мы внедряли многие проекты, направленные на экологичность производства: это сбор и применение в производстве ливневых вод, вовлечение во вторичный оборот технологической воды, переработка отходов производства. В прошлом году мы объявили проект «Вторая жизнь» и предлагаем нашим клиентам возвращать на завод отходы фасадной и кровельной изоляции, которые образуются при строительстве и ремонте зданий в Санкт-Петербурге и Ленобласти.
Каменную вату можно перерабатывать без потери качества бесконечное количество раз. Срок службы материала составляет не менее 50 лет, а с внедрением технологии переработки стремится к бесконечности.
На пути к устойчивому развитию
Новый инвестиционный проект — еще один значимый шаг к созданию устойчивого производства и сохранению окружающей среды. К 2024 году компания планирует построить линию по выпуску каменной ваты, на которой будет применяться одна из самых передовых технологий электрического плавления. Планируется, что в качестве источника электроэнергии будет использоваться возобновляемая генерация. Действующие мощности в дальнейшем будут также переведены на экологичные технологии. Это позволит сократить производственные выбросы углекислого газа всего предприятия на 50% по сравнению с сегодняшними показателями.
Посол Королевства Дания в РФ Карстен Сендергорд высоко оценил появление в России передовых предприятий, которые будут вносить свой вклад в мировые планы по декарбонизации.
— Дания давно находится на передовой «зеленого развития», и это отражается в нашей стратегии, согласно которой страна планирует стать углеродно нейтральной к 2050 году, — отметил он. — Инвестиции компании ROCKWOOL являются замечательным примером целостного подхода к экономии ресурсов. Решения ROCKWOOL интересны с точки зрения энергоэффективности в промышленности и жилом строительстве во всем мире, они экологичны и пожаробезопасны. Дания невероятно гордится тем, что одна из наших компаний представляет современные технологии, которые являются краеугольным камнем экологического перехода и усиленной борьбы с изменением климата.
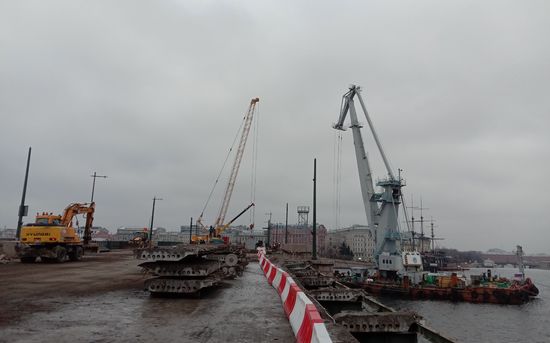
Биржевой мост через Малую Неву, идущий от Стрелки Васильевского острова до Мытненской набережной, впервые в своей истории закрылся на капитальный ремонт. Об идущих работах и том, что предстоит сделать в ходе реконструкции, журналистам рассказали в ходе визита на стройплощадку.
«Биржевой мост был закрыт для движения автомобилей и пешеходов 9 октября. Несмотря на то, что работы фактически только начались, темп набран хороший. Дело в том, что на «раскачку» времени совершенно нет. В ходе капремонта предстоит выполнить огромный объем различных работ, а уже в начале мая 2023 года объект должен быть введен в эксплуатацию. Более того, рабочее движение транспорта планируется запустить еще раньше – в ноябре 2022-го», - рассказал глава Комитета по развитию транспортной инфраструктуры Санкт-Петербурга Андрей Левакин.
По его словам, к настоящему времени выполнены все предварительные работы (организована альтернативная схема движения транспорта, сформированы и огорожены строительный городок и стройплощадка, демонтированы светильники наружного освещения). Кроме того, удалено асфальтобетонное покрытие проезжей части и тротуаров.
«Сейчас рабочие осуществляют устройство конструкции ледореза с помощью плавучего крана, формирование временной опоры разводного пролета, демонтаж плиты проезжей части, а также разбираются противовесы разводных пролетов. Подрядчик – ПО «Возрождение» организовал на объекте двухсменную работу. Всего на стройке занято более 120 специалистов. Работы идут в соответствие с графиком», - отметил Андрей Левакин.
В целом подрядчику при проведении реконструкции моста предстоит осуществить ремонт береговых и промежуточных опор, а также разводных и стационарных пролетных строений, замену разводного механизма с электрического на гидравлический, укладку нового асфальтобетонного покрытия, восстановление исторических элементов декора.
«Несмотря на то, что мост не является объектом исторического наследия и, соответственно, не подлежит надзору КГИОП, он давно стал привычной составной частью облика Стрелки Васильевского острова, которая является одним из классических «открыточных видов» Петербурга. Поэтому, хотя работы и называются капитальным ремонтом, а не реставрацией, перед нами стоит задача сохранить исторический облик переправы. Соответственно, мы постараемся, насколько это возможно, сберечь декоративные элементы моста, а также восполнить утраченные и полностью деградировавшие», - отмечает генеральный директор АО «ПО «Возрождение» Михаил Клобертанс.
По словам Андрея Кочина, директора СПб ГБУ «Мостотрест» (которое выступает заказчиком на объекте), такой подход к ведению работ предопределяет используемые технологии. «Даже несмотря на то, что это несколько увеличивает временные и трудозатраты на реализацию проекта, поскольку имеющиеся конструкции переправы выступают в качестве технологического моста и по ним перемещается строительная техника. В определенном смысле, используя современные технологии мостостроения (в частности, надвижку пролетных конструкций с разных берегов), его можно было бы построить проще и быстрее», - считает он.
Сумма контракта, подписанного с подрядчиком 28 июля 2021 года, по итогам проведенного тендера, превышает 2,37 млрд рублей. Проект работ был разработан АО «Институт Гипромост – Санкт-Петербург» и получил положительное заключение ФАУ «Главгосэкспертиза России».
«Могу отметить, что наши предшественники работали на совесть. Этот капремонт моста – первый за время его существования, а, напомню, существующая переправа была введена в строй в 1960 году. При работах становится ясно, что часть конструкций, могли бы служить и дальше, но решение задачи по капремонту объекта в целом делает необходимым полноценную перестройку всего моста. Ведь механизмы устарели и сильно изношены, а часть конструкций деградировала», - говорит Михаил Клобертанс.
По словам Андрея Левакина, важнейшей частью проекта является замена разводного механизма моста с электрического на гидравлический. «Новый тип оборудования, который планируется здесь установить, обеспечит надежную разводку, а также позволит более экономно расходовать электроэнергию. Биржевой мост является последней большой переправой в Петербурге, на которой до недавнего времени функционировал разводной механизм с электроприводом. На остальных в ходе проводившихся работ по реконструкции уже работают гидравлические системы», - рассказал он.
В настоящее время, параллельно с работами непосредственно на мосту, идет изготовление новых разводных механизмов. «Уже размещены заказы на производство специальной техники. Гидравлическое оборудование выпустит компания «Промтрансавтоматика» на своем заводе в Луге (Ленобласть). Известный холдинг «Алмаз-Антей» изготовит для Биржевого моста гидравлические цилиндры-толкатели. Ко времени, когда мостовые конструкции будут готовы к установке новой техники, она уже будет произведена и доставлена на стройплощадку. Отмечу, что почти все оборудование – российского производства. Исключение составляют некоторые специализированные датчики, выпускаемые крупными мировыми концернами, аналогов которых у нас изготавливают», - сообщил Андрей Кочин.
Все участники брифинга уверены в успешной реализации проекта в заявленные сроки, и заверяют, что примерно через год по Биржевому мосту будет запущено рабочее движение транспорта.
Справка
Биржевой мост (в 1923-1989 годах – мост Строителей) перекинут через Малую Неву – от Стрелки Васильевского острова до Мытненской набережной. Первая переправа в этом месте – еще деревянная была построена в 1894 году по проекту Николая Мазурова. Это был 25-пролетный мост сложной балочно-подкосной системы с двукрылым разводным пролетом посередине. Длина составляла 328 м, ширина – 21 м.
Идея строительства капитального металлического сооружения появилась еще до революции, но из-за нее была надолго отложена. Проект был разработан в 1940 году, строительство началось только в 1957-м. Разработчиками выступили архитекторы Лев Носков и Петр Арешев. Интересно, что продольная ось нового моста была смещена на 300 м ниже по течению Малой Невы, что обеспечило завершение оформления симметричного облика Стрелки Васильевского острова. Появился пятипролетный металлический мост с двукрылым разводным пролетом посередине. Длина переправы составила 252 м, ширина – 21 м.