Вартан Авакян: «Мослифт растет вместе с Москвой»
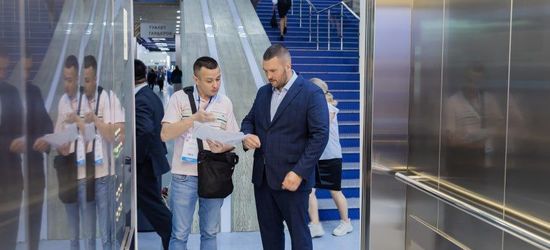
Генеральный директор АО «Мослифт» Вартан Авакян провел брифинг по вопросам развития лифтовой отрасли и компании в условиях санкций. Мероприятие проходило в рамках Международной выставки лифтов и подъемного оборудования «Russian Elevator Week-2023» на ВДНХ.
«Санкции – витамин роста для промышленности. Они создают возможности для тех, кто готов двигаться вперед и развиваться. Компании вынуждены запускать новые процессы и искать новые точки приложения силы. Кроме того, санкции могут подтолкнуть к развитию новых технологий и инноваций, чтобы адаптироваться к нынешним условиям и сохранить свою конкурентоспособность. Мослифт за год сделал серьезный прорыв и мы продолжаем и дальше работать в этом направлении», - отметил Вартан Авакян.
Мослифт в сжатые сроки разработал и запустил в серийное производство четыре новых вида лифта: панорамные, больничные, малые грузовые и лифты на тяговых ремнях. Кроме того, специалисты компании приступили к разработке скоростных лифтов до 2,5 м/с при нынешнем показателе до 1,6 м/с.
Мослифт начал собственное производство комплектующих. Инженеры компании разработали рекуператор электроэнергии на суперконденсаторах. Это устройство позволяет накапливать высвобождаемую энергию во время движения загруженной кабины вниз или пустой кабины вверх, а также во время торможения лифта. Разработали и вводное устройство для лифтов, которое предназначено для подачи и снятия напряжения с питающих линий на вводе в лифт. Первая опытная партия уже выпущена предприятием. В ближайшее время вводные устройства собственного производства полностью заменят импортные аналоги.
«Организация собственного производства комплектующих поможет убрать зависимость от импортных производителей. Реализуя программу импортозамещения, компания достигла доли российских комплектующих в стоимости лифта 95%. Стоимость комплектующих при собственном производстве выходит меньше», - уточнил Вартан Авакян.
Большое внимание в АО «Мослифт» уделяется и социальному направлении. «Мы представляем наши разработки для маломобильных и слабослышащих пассажиров, которые помогут им сделать поездку в вертикальном транспорте комфортной», - подчеркнул Авакян, говоря о новой разработке дополнительного оборудования кабины лифта для слабослышащих жителей.
В такой кабине устанавливается специальный LCD экран. В обычном режиме на нем воспроизводятся информационные видеоролики, а при необходимости связи с диспетчером слабослышащий пассажир, касаясь экрана, видит виртуальную клавиатуру и форму для ввода обращения. Для диспетчера для такого контакта устанавливается также отдельный монитор. Причем диспетчер может инициировать одновременно несколько чатов с пассажирами разных лифтов.
Мослифт предлагает и новые технологические решение по модернизации лифтов, которые подверглись вандальному действию и имеют неэстетичный вид. Теперь по заявке собственника, желающего произвести замену облицовки кабины, не дожидаясь конечного срока эксплуатации лифта, можно обновить без демонтажа всего за пару дней. Предлагаются различные варианты от эконом до бизнес отделки.
«Ранее, для проведения подобных работ, мы выполняли полный демонтаж и транспортировку компонентов кабины на свою производственную площадку. Это занимало много времени, и требовало значительных трудозатрат за счет множества логистических и производственных операций. Теперь мы можем это сделать на месте очень быстро», – сообщил Вартан Авакян.
Мослифт продолжает искать новые решения в условиях ограничений, широко используя современные подходы в области цифровизации, искусственного интеллекта и анализа больших данных. В настоящее время активно развиваются проекты по расширению номенклатуры модулей автоматического мониторинга для станций управления лифтами различных моделей, предиктивной аналитике данных, внедрению новых каналов связи с пользователями лифтов с целью повышения безопасности, комфортности лифтов и качества их обслуживания.
Главная задача компании - обеспечить безопасность лифтов, комфорт для пассажиров и гармоничную организацию всех процессов, связанных с лифтовой отраслью, начиная с проектирования и заканчивая эксплуатацией и утилизацией.
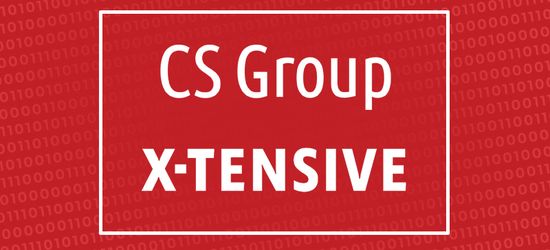
Российские компании-разработчики «СИЭС Групп» и X-tensive (ООО «Экстенсив-Автоматизация») заключили соглашение об интеграции платформы TechnologiCS (разработано АО «СиСофт Девелопмент») и комплекса DPA (разработано ООО «Экстенсив-Автоматизация»).
DPA – это система мониторинга класса MDC (Machine Data Collection, автоматизированного сбора данных) и управления производством, отражающая картину процессов в реальном времени. Решение позволяет подключать любое оборудование и получать данные в едином нормализованном виде. В систему входят восемь модулей: мониторинг оборудования, технологии, управляющие программы, управление инструментом, сигналы и тикеты (сообщения о проблеме), оперативное планирование, аналитика, KPI. DPA может быть масштабирована на любой объем парка оборудования.
Сочетание DPA с цифровой платформой TechnologiCS для автоматизации и информационной поддержки процессов подготовки, планирования и оперативного управления ускорит процесс внедрения и создаст дополнительные возможности для пользователя.
Александр Воротников, генеральный директор АО «СИЭС Групп»:
«Наше внимание привлек масштаб присутствия решений X-tensive на рынке ПО для автоматизации машиностроения. Объем заказов среди предприятий в данном секторе растет. Интеграция продуктов – это инструмент, который позволяет нам еще точнее, быстрее и эффективнее отвечать на запросы заказчиков, создавать уникальные проектные решения, ускорять и расширять процесс автоматизации российской промышленности. И, тем самым, способствовать появлению новых ниш для отечественной разработки».
Алексей Белов, генеральный директор ООО «Экстенсив-Автоматизация»:
«Для нашей компании взаимодействие с АО «СИЭС Групп» – значимый шаг вперед. Он чрезвычайно важен для воплощения стратегии роста и развития. В сегодняшних непростых условиях взаимная эффективная интеграция усилий крайне необходима для того, чтобы приносить максимальную пользу заказчикам в области автоматизации промышленного производства.
Совмещение DPA и TechnologiCS – это настоящее инновационное решение, предоставляющее полноценный набор инструментов в рамках концепции Индустрии 4.0. Мы уверены, что наши совместные продукты и услуги превзойдут ожидания заказчиков и позволят им значительно повысить эффективность производства, сократить издержки, грамотно и на основании достоверных данных проводить изменения, в том числе – организационные.
Мы верим, что создание новой цифровой культуры производства и снижение влияния человеческого фактора на эффективность работы предприятий – это достойные цели. Вместе с тем, интеграция DPA и TechnologiCS позволяет превзойти их и максимизировать экономический эффект от проведения мероприятий по автоматизации и переходу к цифровому управлению на основании данных».
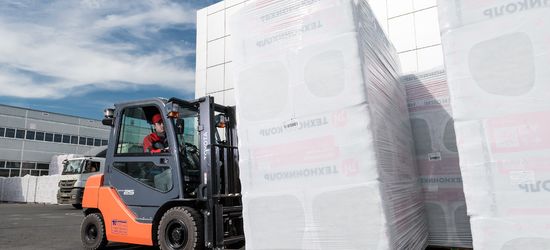
Производительность труда на складах заводов каменной ваты ТЕХНОНИКОЛЬ увеличилась на 28%. В целом в 2022 этот показатель достиг 22,8 млн руб./чел. в год. Рост произошел за счет автоматизации складов готовой продукции, а также улучшения организационных процессов. Общий объем инвестиций в проекты составил 8 млн руб. В планах компании – внедрение системы автоматической идентификации товаров и беспилотной техники, в том числе БПЛА. Это повысит производительность труда еще на 180%.
Производительность труда выросла благодаря автоматизации логистики на всех «Заводах ТЕХНО» в России. Максимальные показатели по итогам 2022 отмечены на заводах в Юрге (Кемеровская область) – 30,5 млн руб./чел. в год, в Красном Сулине (Ростовская обл.) – 30,1 млн руб./чел. в год и в Рязани – 28,6 млн руб./чел. в год.
На предприятиях внедрили систему автоматизированного управления складами готовой продукции на базе WMS. Это ускорило выполнение логистических операций, повысило качество управления складскими запасами и оптимизировало сроки хранения. В частности, работа складов была настроена по принципу FEFO (First Expired – First Out), согласно которому первым отгружается товар с наименьшим запасом срока годности. Это исключает появление неликвида.
WMS позволяет сгладить сезонные колебания и привлекать к работе необходимое количество персонала в периоды повышенного спроса, в том числе обращаться к аутстаффинговым компаниям. Благодаря автоматизации сроки обучения и адаптации как временных, так и постоянных кадров значительно сократились.
«Одно из важнейших преимуществ автоматизации – возможность профессионального роста и развития компетенций для сотрудников. Низкоквалифицированные, рутинные, физически тяжелые операции могут выполнять машины, а люди, пройдя дополнительное обучение, работать в более комфортных условиях, решать творческие, интересные задачи, заниматься интеллектуальным и безопасным трудом», – прокомментировала Татьяна Бертова, директор по логистике направления «Минеральная изоляция» компании ТЕХНОНИКОЛЬ.
Внедрение WMS на заводах каменной ваты ТЕХНОНИКОЛЬ началось в 2018 году. Пилотной площадкой стал «Завод ТЕХНО» в Рязани. Склады готовой продукции всех предприятий были оснащены системой уже к концу 2021, и с 2022 года WMS вышла на полную мощность. Реализация проекта увеличила производительность труда на 28%.
«К подготовке проекта мы приступили еще в 2011 году. Прежде чем автоматизировать логистические процессы, их нужно правильно организовать, а также устранить ошибки. В противном случае все недостатки автоматизируются вместе с системой: мы просто переведем несовершенный бизнес-процесс на язык машин. Поэтому мы проделали предварительную работу: ввели систему адресного хранения, выполнили зонирование склада, нанесли разметку, сократили маршруты погрузчиков, запустили программу обучения кадров, начали использовать принципы бережливого производства и т.д. Все это еще до внедрения WMS позволило нам увеличить производительность труда почти в 2 раза», – отметила Татьяна Бертова.
К 2025 году ТЕХНОНИКОЛЬ собирается повысить производительность труда на заводах каменной ваты еще на 20%, а к 2030 этот показатель планируется увеличить на 180%. В течение ближайших 2 лет компания закончит внедрение технологии RFID (способ опознания объектов с помощью радиочастотной идентификации). За счет нее уже сейчас на 10% ускорены прием, размещение, отбор и отгрузка готовой продукции.
К 2030 году склады оснастят беспилотной техникой. Уже завершен тестовый проект инвентаризации складов с помощью беспилотных летательных аппаратов (БПЛА), компания готовится к его масштабированию на все минераловатные производства. Опытная эксплуатация показала, что БПЛА в 30 раз повышает эффективность этой операции: если раньше на инвентаризацию требовалось 192 человеко-часа (ее проводили 16 сотрудников за 12 часов), то с дроном – 6 человеко-часов (3 сотрудника и 2 часа). Кроме того, ТЕХНОНИКОЛЬ начала разработку проекта по использованию беспилотных погрузчиков.